2025.04.18
構造解析のCAE(Computer Aided Engineering)は、製品や部品が外力(荷重、振動、圧力など)を受けたときの変形、応力、反力、座屈、疲労、破壊などの挙動をシミュレーションで予測する技術です。ソフトウェアの開発やコンピュータの高速化に伴い、現在では設計者が使用するツールとして普及しました。主に有限要素法(FEM)に基づき、設計段階で製品の信頼性や安全性を事前に評価するために使用され、大きな成果をあげています。さらに従来の試作や実験にかかる時間やコストの大幅な削減に期待できます。この記事では、構造解析CAEの特徴や利点、精度向上のポイントについて解説します。
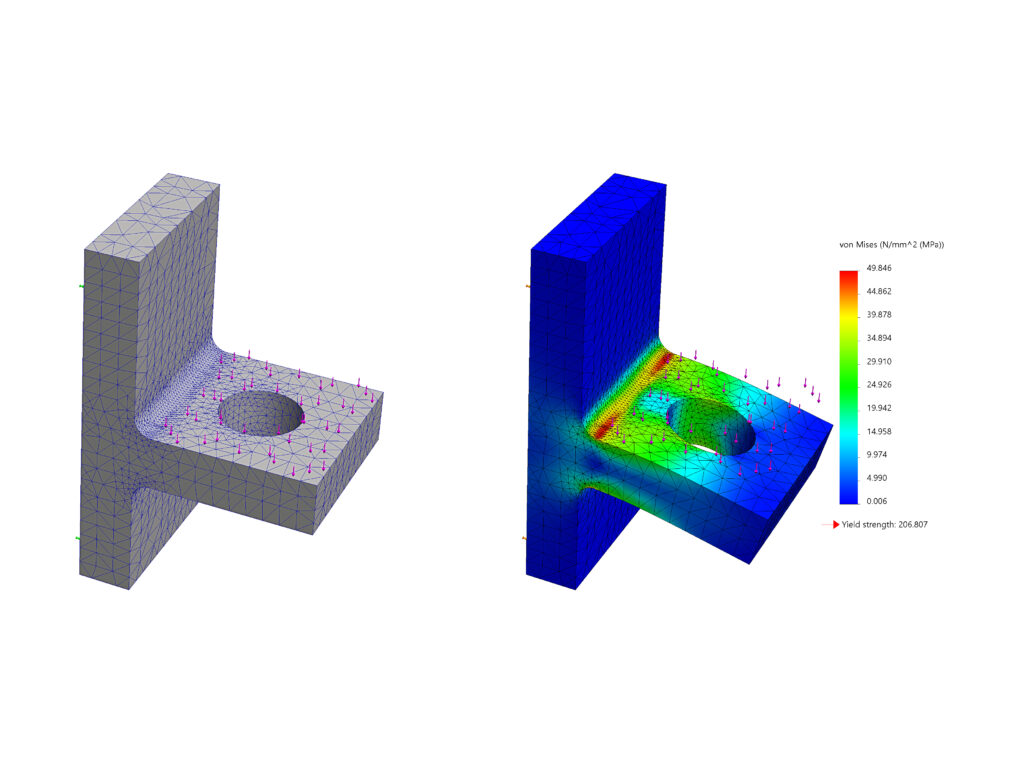
構造解析CAEの基礎である有限要素法
構造解析CAEの基礎となる有限要素法(Finite Element Method)は、1950年台の後半から理論研究などが発展しました。
- 1970~1980年代:
商用ソフトが登場し、ユーザがプログラムを組まなくても利用できるようになった - 1990年代:
PCの高性能化とソフトウェアのユーザビリティの向上
CAEがより広範囲な業種の企業にも導入
3次元CADとの統合が進み、設計と解析が密接に連携ができるようになった - 2000年代~:
各種の業務に適用され、なくてはならないソフトウェアの一つとなった
CAEは、ものづくりの現場における設計・開発プロセスを大きく変革してきた技術です。今後は、シミュレーションの自動化やリアルタイム解析、さらにはAIとの連携によって、さらに高度なエンジニアリングツールへと進化していくことが期待されています。
構造解析CAEの特徴と利点
変形や応力分布の可視化
構造解析CAEの特徴として、製品に加わる荷重や拘束条件を仮想環境で設定し、変形や応力分布を数値で可視化できます。使用者は、各種の条件を変更して解析を行い、その結果を見て製品の設計や製作工程に活かしていくことができます。そして、実験では見えにくい内部応力や集中応力も解析可能です。
CADで作成された製品形状のデータの解析
ユーザがCADで作成された製品形状のデータを、複雑な形状を多数の小要素(メッシュ)に分割して解析し、そこに境界条件と呼ばれる、荷重や変位の条件を設定します。そしてソフトウェア内に、物理現象を高精度で模擬計算できるようにプログラムされたソルバーに計算データを読み込ませて、アウトプットとして変位・ひずみ・応力の分布を得ることが出来ます。ソルバーは、線形解析から非線形(大変形・材料非線形・接触)まで幅広く対応しており、適応範囲はさまざまな構造・材質にわたります。特に解析精度に直結する材料モデルは、金属・樹脂・複合材料など、幅広く使用可能です。
開発期間の短縮、コスト削減、信頼性向上に寄与
構造解析CAEは、設計品質を高めながら開発の効率化を実現する、現代のものづくりにおいて欠かせない技術です。特に強度・剛性・安全性が重要な製品分野(自動車、航空機、建設機械、精密機器など)では、CAEを活用することで開発期間の短縮、コスト削減、製品の信頼性向上のすべてに貢献できます。
開発期間の短縮とコスト削減
試作品を作る前に構造の強度や安全性を事前評価できるため、設計の初期段階で問題点を発見しやすくなります。事前の検討をCAEで実施することで開発コストの削減にも貢献します。つまり、試作回数の削減とコストダウンに貢献するツールとなります。そこで得られた結果、CAEの結果のみならず、実験(試作)結果を踏まえて設計にフィードバックを行えば、軽量化や構造合理化など、性能とコストのバランスを取る設計判断が可能になります。さらに不要な剛性と判断した場合や、生産工程の見直しを行えば、一案として材料の無駄を削減なども考えることができるでしょう。このように、設計や生産工程の最適化に貢献します。
製品の信頼性向上
またCAEのメリットは、様々な設計案をバーチャル(仮想的)にトライアル出来ることです。そして構造強度・応力分布の違いを迅速に比較でき、最適案の選定が効率的に行えます。これは、製品のトラブルを事前に予測できることになり、製品の信頼性・安全性の確保に大きく寄与します。
CAEの解析精度向上
構造解析CAEは、実物の現象を正確に再現することで、大きな効果を発揮します。つまり、解析精度が重要なポイントとなります。一方で、解析精度と一言でいっても、解析の内容や目的によっても様々です。近年は、CAEソフトウェアのブラックボックス化が進んでおり、ユーザが数値計算の専門的な知識を有していなくても、簡単な操作である程度適切な結果が得られるようになってきていますが、基本的なポイントをおさえて使用することで、より一層便利なツールとして効果をあげていけるでしょう。経験者には当たり前のことかもしれませんが、復習をかねてお読みいただければと思います。
形状モデルとメッシュの作成
解析モデルの形状は、現実の物理現象を再現できるように、必要なディテールは残しつつ、不要な部分は適切に簡略化することで解析時間を短縮できます。ただし、必要な詳細を省きすぎると解析精度が低下しますので、注意が必要です。有限要素法では、形状CADデータをメッシュに変換する必要がありますが、その品質が解析精度に大きな影響を与えます。局所的に応力集中が見込まれる箇所には細かいメッシュを適用する一方、メッシュのアスペクト比や歪みを最小限に抑えると良いでしょう。
材料特性や境界条件の設定
解析に使用する材料データは解析精度に大きな影響を与えます。使用する材料の非線形特性(弾塑性、粘弾性など)や温度依存性がある場合は、それらを考慮した材料モデルを設定することが重要です。ソフトウェアに事前に組み込まれている材料データベースの値を使用するだけではなく、よく使用する材料については、材料試験を行い、データを構築しておくと精度向上が見込まれます。そのときに材料パラメータのばらつき等も見ておくと参考になります。境界条件や荷重の設定ミスは、CAEの信頼性を大きく損ねますので、適切な設定が必要です。過去の実験や実測データに基づいた現実的な条件設定を行いましょう。
解析結果の検証と妥当性確認
CAEの解析結果は実験結果や理論解と比較して妥当性を確認することが重要です。このとき材料モデルや境界条件を変化させた結果などを確認しますが、パラメータスタディや感度解析を通じて結果の信頼性が高まるでしょう。そして、それらの検証を通して、いわゆる解析ノウハウを得ることができます。その際のポイントについて以下に示します。
- CAEで精度の良い結果を得るためのノウハウ
- ソフトウェアの知識だけでなく、対象とする物理現象や設計分野に関する深い理解
- 解析目的に応じて、静解析・動解析・線形 / 非線形解析などの適切な手法の選択
上記の知識がバックボーンとしてあるととても有効です。そしてCAEはあくまで近似解であるため、過信せず、エンジニアの判断と経験も加味することが重要です。
CAE解析結果と実測結果を比較・検証する際のポイント
CAEは、設計段階で製品の性能や挙動を予測する有効なツールですが、実際の物理現象を完全に再現するものではありません。そのため、解析結果の信頼性を高めるためには、実物の測定結果との比較検証(コリレーション)が欠かせません。そのコリレーションのポイントとして今回は自動車のプレス部品における板成形CAEを取り上げます。具体例は下記に示しております。
- 自動車のプレス部品(ドアパネル、フロアパネル、ピラー部品など)は、軽量化・剛性確保・量産性の観点から非常に厳しい品質要求
- CAEと実測の比較は単なる「一致確認」ではなく、部品設計・金型設計への量産性向上・品質性向上・立ち上げ期間短縮などのフィードバックを目的とする非常に重要なプロセスの生産技術
これらはCAEの解析精度と実物との整合性が極めて重要です。現実との整合性を高めるためには、測定条件の統一、ばらつきの考慮、材料特性の精密な把握がカギとなります。
評価の目的に応じた測定項目の選定
評価目的によって測定項目と比較するべき物理量が変わりますので、以下の表にまとめます。製品の物理量測定には、何を測るかによって、3Dスキャナ、DIC(デジタル画像相関法)、接触式ゲージなどを用います。CAEと正確に比較するためには、同一の評価点・断面を設定する必要があり、基準座標の統一をきちんと行う必要があります。さらに的確に比較を行うには、制作された製品のバラツキ・再現性も考慮することが望ましいです。つまり、自動車部品は量産を前提とするため、1個体の実物ではなく複数部品の測定値を統計的に処理することで、CAEの解析精度について総合的な判断ができます。
成形性評価 | 製品に発生したしわ、ワレの発生状況を実物とCAE結果で比較する。 製品では、ひずみ(板厚減少量)を測定する。CAE結果からしわやワレの判定には、成形限界線図(FLD)などもよく用いられるので、評価方法が適切かどうかも含めて検討すると良い。 |
|
---|---|---|
寸法精度 | 成形後に発生したスプリングバックの予測がCAE解析の精度のポイントになる。製品形状を測定し、その座標データとCAE解析結果を直接比較する。関連して、最終形状の輪郭について精度をチェックすると効果的である。 |
CAE解析の特性や現象に合わせたコリレーション
板成形CAEの場合、その現象は3つの非線形性を伴います。それは、材料が弾塑性である材料非線形、材料と金型が接触して変形する接触非線形および材料が大変形を伴う幾何学的非線形です。そのため変形履歴をきちんと追跡して検証することが、コリレーションのポイントとなります。例えば、3次元測定機で成形前および成形後の形状は測定して、CAD製品形状データを用いてスプリングバック量を算出することはできますが、その要因特定には刻々と変化する材料の変形(ひずみ)を追跡することが必要であります。この変形(ひずみ)履歴を追従するには、ひずみゲージやDICが有効になります。
CAE結果とDIC結果の比較
ひずみゲージはポイントで測定する場合には有効ですが、任意の方向のひずみや面全体でひずみを測定する場合にはDICを使用することが非常に有効になります。DIC結果と比較する際のポイントについて下記に示します。
- ひずみなどは基準の長さをいくつにとるかによって、局所的なひずみを見逃したり、そもそも値が異なる
- CAEでもメッシュサイズがひずみ値に影響を与える
- 座標系を揃えることや的確な位置合わせにより、CAEとDICで正確に比較する
またCAE結果と測定結果を比較する場合、一つのシステム内で行えることが重要になります。DICシステムの「MatchID」は、FE-VALというCAE解析結果の読み込みDICの測定結果と比較する機能を有しています。測定したDICと読み込んだひずみの基準サイズ(解析のメッシュサイズ)調整や位置合わせなどが簡便に行える、とても便利なツールとなります。そして、変形履歴に沿って刻々と変化するひずみ量の差を定量的に比較することができます。
誤差要因の特定と対策
誤差は、製品種、成形方法、材料などによって異なりますし、複合要因である場合も多いです。よって、一つ一つ丁寧な検証が必要ですし、現象のメカニズム、ソフトウェアの特性や専門知識、製造の経験やノウハウと合わせて、比較検証を行う必要があります。CAEの誤差をなくすのが理想的ですが、CAE結果には誤差があるものとして、運用面を含めて総合的な活用方法の検討対策を行うのも一案です。
主な誤差要因 | ||
---|---|---|
材料モデルおよび材料パラメータ | 解析に使用した材料モデルが適切であったかの比較検討を行う。特に軽量化対応の新材料では、重要となる。合わせて、その材料モデルに使用する材料パラメータの取得・運用方法の検討も行うと良い。 | |
材料ばらつき | 材料のロットによる、ばらつきデータを事前に取得しておく。 CAE解析に使用するデータ(材料パラメータ)の、上限、下限、中央値などを把握し、それらの値の運用方法を決めておく。 |
|
摩擦・潤滑条件 | 成形時の油種類や量を測定し、摩擦係数を現実に近づける。 製品や成形方法毎にパラメータスタディを実施する。 |
|
解析パラメータ | 多くの解析精度比較検証を行い、ソフトウェアに合わせたパラメータチューニングを行う。そのとき統計手法を用いると効果的である。 | |
測定誤差 | 測定機器の校正と再現性の確保、評価点の定義明確化を行う。 | |
評価方法 | CAE結果から、しわやワレの評価判定方法を見直す。成形のメカニズムからの分析や、これまでの経験値との比較も重要である。 |
材料評価とVFM(Virtual Field Method)
薄板(自動車用の高張力鋼板やアルミニウム合金板など)を対象としたCAE解析では、材料モデルの正確さが解析精度に大きく影響します。特に板成形や構造強度評価では、板材特有の異方性や履歴応力の再現が不可欠です。近年では、材料モデルやCAE解析に使用する材料パラメータについて、理論面および実験(測定)面の研究開発が進められています。以下は、CAE精度向上のために材料モデルの観点から考慮すべき主なポイントです。
適切な材料モデル
CAE解析に使用する機械的特性値のみならず、材料の異方性を考慮して精度よく解析するためには、必要に応じて高次の降伏関数など、適切な材料モデルを適用することが必要です。
高次の降伏関数を用いる場合
CAEでインプットするには材料パラメータが必要となり、一般的な材料試験の短軸引張試験では取得できないデータが含まれます。この場合は、二軸引張試験などデータ取得に対応する材料試験を行う必要があり、いくつかの方法が提案されています。
一般にこれらのデータを取得する場合
ユーザがこれらに対応した試験機を作成するか、一材質当り数百万円の委託試験を実施するなどの方法が考えられます。CAEの高精度化に必要なコストですが、やはりできるだけ削減は図りたいものです。
DICデータを使用した弾塑性CAE精度向上の取り組み事例
上部をクリックいただけますと資料のダウンロードが可能です。
「MatchID」は、VFM(Virtual Field Method)という独自の機能があります。これは、様々なひずみ履歴を含むDICデータを分析して、高次の降伏関数や非線形の応力―ひずみ線の各種モデルの材料パラメータを同定する手法です。DICデータを取得するのに材料試験機は単軸引張で対応できますので、データ取得のコスト削減を実現できます。
東京貿易テクノシステムのDICソリューション「MatchID」のご紹介
東京貿易テクノシステムがお届けするMatchIDは、デジタル画像相関法(DIC)により簡単にかつ高精度での形状・変位・ひずみのデータ取得をします。MatchIDは、豊富な分析機能も搭載しています。DICデータを活用したVirtual Fields Methodによる材料特性パラメータの同定や、CAEの解析結果(特に構造解析)と測定結果の定量的な差分評価が可能なFE-VALです。これらが、CAE解析精度向上に貢献できることは、これまでに述べてきました。MatchIDは、高度な材料評価や、CAEと併用して、より詳細な分析を必要とする方におすすめの製品です。詳細は、以下からご覧いただけます。
お問合せ
(メールまたはお電話にて回答させていただきます)
(オンライン会議ツールを使って直接お話しいただけます)