工程管理は、製造業において高品質な製品を生産し続けるために不可欠な管理手法です。工程管理をおこなうことで、業務の効率化や品質の向上が期待できます。そのためには、工程管理の手順やポイントを押さえることが大切です。
この記事では、工程管理について、生産管理との違いやメリット・デメリット、効率よく工程管理を進めるための方法などを詳しく解説します。
工程管理とは?
工程管理とは、生産や業務の各段階を計画・実行・監視・改善するプロセスのことです。
具体的には、各工程の進捗や実績管理、納期を守るための生産調整、品質や生産効率の維持管理などが挙げられます。
工程管理では、Quality(品質)、Cost(コスト)、Delivery(納期)の最適化をおこなって、プロジェクトの成功へ導きます。
製造業においては、高品質な製品を低コストで製造し、納期を守り続けることが求められます。その責任を果たすためにも、QCDの各要素をバランスよく管理する工程管理の考え方は重要といえます。
工程管理と生産管理の違い
工程管理と似た言葉に生産管理がありますが、その範囲と目的にはそれぞれ違いがあります。
工程管理では製造プロセス自体の効率化や納期遵守に重きを置き、生産品の数量、工程のスケジュール、生産ラインの配置など、各製造プロセスを管理します。
一方、生産管理は生産活動を通じて、安定・継続的に利益を挙げることを目的とし、原材料の調達や在庫管理、製造、出荷など、生産活動全体を管理します。つまり、工程管理は生産管理の範囲の一部に含まれているのです。
製造業で工程管理が必要な理由
製造業で工程管理が重要な理由は、前述したように製造工程全体の管理をおこなうことで、作業効率化や品質保全が見込めるためです。
製造業では、製品の品質を一定の水準で維持し続けることや、作業者に過度に負担をかけずにより効率的に製造工程での適切な作業配分を、検討することが常に求められています。
もし工程管理が適切におこなわれず、進捗状況や品質の把握が不十分となり納期遅れが発生すれば、企業の信頼を大きく低下させる恐れがあります。
そのような事態を引き起こさないよう、細かい部分までしっかりと工程管理をおこない、日々発生する問題を最小限に抑えながら、生産を円滑に進めなければなりません。
工程管理が必要となる現場例
どのような生産現場でも工程管理は重要ですが、大規模プロジェクトのように複数の生産工程が存在する場合や、製品によって生産工程が異なる場合は、特に工程管理が必要となります。
大規模プロジェクトでは、現場の作業員はもちろん、それ以外にも多くの人が関わり作業が進められます。そのうえ、大元のプロジェクトの下に細分化されたプロジェクトが紐づいていることも多く、一つひとつの工程や作業数もさまざまです。また、製品によって生産工程が異なる場合も同様に、工程数や作業内容が個別に変わってきます。
このような場合、工程管理が適切におこなわれないと、全体に対する各作業の位置づけがわからなくなってしまったり、スケジュールの乱れや遅延につながったりして、大きな問題に発展する恐れがあります。
仮に、工程管理において、進捗や作業内容がリアルタイムで更新されない場合、状況を把握するために各担当者に確認を取ることになるため、作業時間とは別に追加で工数がかかります。また、工程管理が属人化すると、担当者が不在の場合に他の担当者が進捗状況を把握するのが難しくなります。
そのような状況が続くと、特定の人材にのみ知識やスキルが集中し、作業員のレベルにばらつきが生じて、生産品の品質低下を引き起こす恐れがあります。また、突発的な問題に対処できなくなるなど、業務の継続自体が難しくなる場合も出てきます。
このような問題を未然に防ぐためにも、適切かつ正確に工程管理をおこなう必要があります。
工程管理を実施するメリット
では、工程管理をおこなうと、どのようなメリットが得られるのでしょうか。5つに分けて解説します。
製造工程を見える化できる
工程管理を実施することのメリットとしては、まず製造工程の見える化ができる点が挙げられます。
製造工程の見える化は、効率化を促進し品質管理を強化するうえで重要です。
製造工程を見える化することで、社内コミュニケーションの改善や意思決定のスピード化につながるでしょう。
製造工程が属人化すると、知識やスキルが特定の人材に偏ったり、業務が集中したりして、生産効率の低下を引き起こす恐れがあります。また、そのような人材が休暇を取ると突発的な事態に対応できなくなるほか、最悪の場合、生産自体が滞る恐れもあります。
品質の向上と安定化につながる
工程管理をおこなうと、品質の向上や安定化が実現します。
前述したとおり、工程が見える化されるため、トラブル発生時も迅速な対応を取ることが可能です。また、現状を見ながら人員や工程の配置を効率的かつ適切におこなえるため、作業が標準化され、製品の品質を維持しやすくなります。
品質を保つためには、歩留まり率(原料から良品がどれだけ作れるかの割合を示す指標)や、直行率(最初の工程で不良品を出さずに合格する割合)などの指標を見ながら効率よく製造することが重要です。少量生産においては、多少品質のばらつきや不良品が発生しても、そこまで大きな問題にはならないでしょう。
しかし、大量生産において不良品の増加は、歩留まり率や直行率の低下につながります。そのような問題が発生した場合には、工程管理を通じて現状の製造工程を正しく把握し、課題の要因を調査・分析することが求められます。
製品の品質管理についてさらに詳しく知りたい方は、以下の記事をご覧ください。
生産性の向上につながる
適切に工程管理を実施することは、生産性を高めることにもつながります。
例えば、各作業におけるムダを洗い出すことができれば、作業員や設備の稼働率を高められます。
また、各工程の進捗状況を確認しながら調整や改善をおこなえば、生産にかかるリードタイムを短縮できます。ひいては、工場全体における1日あたりの生産能力向上にもつながるでしょう。
リードタイムについてさらに詳しく知りたい方は、以下の記事をご覧ください。
無駄なコストの削減ができる
工程管理をおこなうと、製造工程の無駄を洗い出すこともできます。出てきた無駄を省けば、製造原価などのコスト削減につながるでしょう。
製造業では「7つのムダ」がよく知られており、これらを特定し改善していくことにより、生産性の向上やコストの削減につながるといわれています。具体的には、製造工程の加工・在庫・不良や手直し・手待ち・作りすぎ・動作・運搬の7つのムダに着目し、生産性の低下やコストアップを引き起こす要因を特定していきます。
例えば、各工程で必要な原材料の種類と量を明確に管理できれば、「ある製品を製造するのにどの材料がどれだけ必要か」という情報が可視化されます。これにより、材料不足や過剰に在庫を抱えるリスクを防ぐだけでなく、維持管理に必要な倉庫代のようなコスト削減にもなり、効率的な生産体制が構築できます。
納期遅延を防止できる
工程管理をおこなうことで、納期遅延を防止することが可能です。
また、工程管理を通じて製造工程が可視化できると、各工程の作業時間や必要な人員数を正確に把握できるようになります。
その結果、より効率的な人員配置や作業の振り分けが可能となり、生産性の向上へとつながります。また、作業に必要な期間も短縮でき、納期に対して余裕を持った生産が可能となります。
ニーズに合った製品を期日どおりに納品することは、顧客満足度を最大化するうえで重要です。納期遅延の防止のためには、工程管理の状況をもとに綿密な生産計画を立てましょう。
工程管理をおこなう手順
工程管理では、PDCAサイクルの考え方が応用されています。
PDCAサイクルとは、Plan:計画、Do:実行、Check:監視(振り返り)、Action:改善のそれぞれの頭文字を取ったものです。これらは前述した工程管理の考え方に直結しているため、PDCAサイクルを回すことは工程管理の改善につながります。
ここからは、PDCAサイクルに基づいて工程管理をおこなう手順をご紹介します。
【Plan】生産計画を立てる
工程管理を実施するためには、まずは上流にあたる生産計画を立てる必要があります。生産計画とは、何を、いつまでに、どれくらい生産するのか考えることです。前述したとおり、生産ライン全体の状況を把握する生産管理に対し、工程管理では特定した製造工程の管理をおこないます。
工程管理を効率的におこなうためには、データに基づいた事前計画が重要です。過去の製造期間、生産量、不具合発生の有無と解決に要した時間などを総合的に分析し、計画を策定しましょう。
計画を作成する際には、まず全体のスケジュールから各工程の所要時間を見積もり、そこから月間・週間の詳細な作業スケジュールへと落とし込んでいきます。具体的な作業内容のほか、手順や必要な人員・資材などを明記しておくことも大切です。
【Do】計画を実行する
実行段階では、計画に基づいた作業指示や日々の進捗管理をおこないます。基本的には計画にしたがって製造を進めますが、ときには計画外の問題を見つけ出すことも重要です。
製造中に想定外の箇所で新たな問題が発生した場合は、できる限り早期に対処することが求められます。そのうえで、発生した課題を記録に残し、計画の振り返りに活かすことが大切です。
【Check】工程管理計画の取り組み結果を見直す
製造工程で明らかになった課題を可視化し、全社で共有することで、よりよい改善策の立案につなげていきます。
ただし、無理に改善する必要がない箇所まで手を加えないようにしましょう。変更箇所を明確にし、重点的に見直すことで、現状の課題に対する立案した改善策が有効かどうかが見極められます。
例えば、作業員や設備の稼働率の低さが要因で、生産効率の低下を引き起こしているとしましょう。このときに、無駄な作業や動作、待ち時間などがないかを確認することで、作業手順や人員配置の見直しをおこなうなどの改善策が立案できるでしょう。
【Action】改善策を実施する
改善策を実行したあとは、その結果をさらに次の計画へ反映させることが大切です。当初立てた計画に固執せず、状況に応じて柔軟に対応することが求められます。
細かく評価をつけてPDCAサイクルを繰り返し回し、現状の作業工程を継続的に見直すことで、よりよい作業工程の構築が実現します。
工程管理を効率化する方法
工程管理を効率化する方法もチェックしておきましょう。主要な2つの方法をご紹介します。
工程表を活用する
工程管理を効率的におこなうには、工程表の活用が有効です。工程表の活用を検討する場合は、作成方法と工程表の種類をそれぞれ検討します。
工程表を作成する方法には、紙で作る方法とExcelで作る方法の2つがあります。
紙で作る場合は特別なスキルは不要で、その場で容易に修正できます。また、思いついたまま直感的に書き込んでいけるのも魅力です。しかし、データとしてリアルタイムで更新するのが難しく、複数の工程を並行して管理する必要がある大規模プロジェクトなどには不向きです。また、手書きである以上、計算ミスが発生する可能性もあります。
一方、Excelで作る場合は、データとして保存や共有ができる、自動計算によりミスを防げる、テンプレートを別のプロジェクトでも再利用できるなどのメリットがあります。
しかし、Excelの関数や使い方をある程度理解していることが求められます。該当するプロジェクトの規模や目的、担当者のスキルレベルを考慮したうえで、適切な方法を選択しましょう。
工程表の作成方法を決めたら、次にどのような工程表を作成するかを検討します。工程表には主に、「バーチャート工程表」「ガントチャート工程表」「グラフ式工程表」の3つがあります。
ここから、それぞれの工程表の特徴やメリット・デメリットを解説します。
バーチャート工程表

バーチャート工程表は、視覚的に理解しやすいのが特徴です。縦軸に作業項、横軸に時間を記載し、各作業の開始から終了までを棒状で表示します。
バーチャート工程表のメリットは、以下のとおりです。
- 作成が容易
- スケジュールの変更に柔軟に対応可能
- 進捗状況を把握しやすい
一方、デメリットは以下のとおりです。
- 工程同士の関連性がわかりにくい
- クリティカルパス(プロジェクトの最長期間を決定する一連の作業)の把握に向いてない
ガントチャート工程表

ガントチャート工程表は、各製造工程の達成率や、進捗率がわかりやすいのが特徴です。バーチャートと同じく縦軸は作業項目ですが、横軸に進捗率を使用します。
ガントチャート工程表のメリットは、以下のとおりです。
- 進捗率の把握が容易
- 複数作業の同時進行時に有効
一方、デメリットは以下のとおりです。
- 工程間の関連性がわかりにくい
- 時間軸での把握が難しい
グラフ式工程表
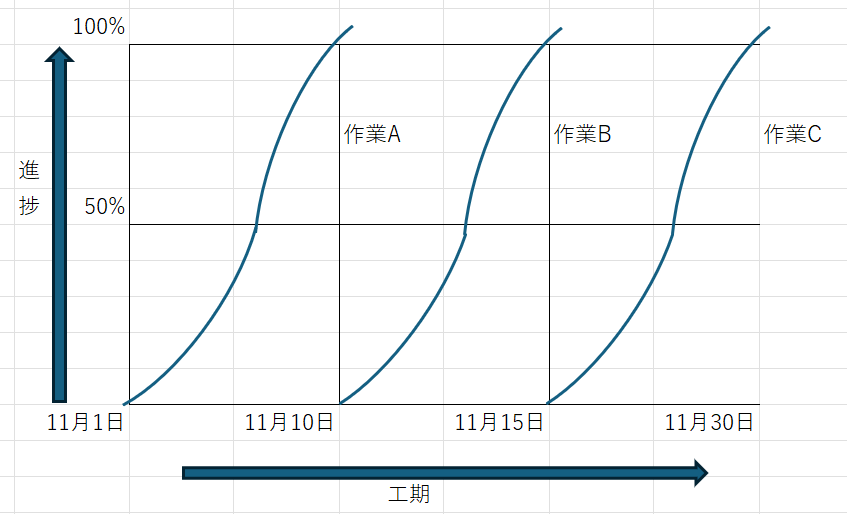
グラフ式工程表は、縦軸に進捗率、横軸に日数をとったグラフ形式で、進捗率と時間の両方を同時に把握できるのが特徴です。
グラフ式工程表のメリットは、以下のとおりです。
- 作業の進捗状況と予定日数を一度に把握できる
- 複数の作業の進捗を簡単に確認できる
- 多くのチームやプロジェクトを同時に進める際に有効
一方、デメリットは以下のとおりです。
- 表が複雑で、慣れるまで作成に時間がかかる
- 一目で内容を把握しづらい
工程管理システムを活用する
工程管理システムの活用も有効な手段です。
工程管理をシステム化すれば、タスクの進捗状況がリアルタイムにデータで確認できます。導入するシステムによっては、アラート機能による早期の問題発見や蓄積されたデータの分析など便利な機能を搭載しているものもあります。
ただし、紙やExcelで工程表を作成する場合と比べ、初期コストがかかる点には注意が必要です。
専用の工程管理システムを導入すれば、前述したように現状をリアルタイムに把握できるため、工程の見直しや改善をスムーズにおこなえます。結果として、管理の手間やミスを削減でき、プロジェクトそのものの質を向上できるでしょう。
製造業で工程管理システムを導入する際のポイント
工程管理システムの導入が決定したら、以下のようなポイントを押さえてシステムの選定を進めましょう。
自社の生産方式に適したシステムか
導入するシステムは、自社の生産方式に適しているかどうかという基準で選定する必要があります。製品数や生産量、部品数など、自社の生産体制をきちんと把握することが重要です。
例えば、製品の種類が多い場合には、柔軟に工程を変更できる機能があるものを選ぶ、生産性向上と品質管理強化のどちらに重きを置くかで比較検討する、などの視点でシステムを選定していくとよいでしょう。
他のシステムと連携しやすいか
一つのシステムで製造工程をすべて管理できるのが望ましいですが、既存の原価管理や品質管理、業務管理など個々のシステムとの連携するケースもあります。そのため、システム間の連携が容易なシステムを選ぶようにしましょう。
機能性とコストのバランスはどうか
一つのシステムで工程管理をおこなうのであれば、進捗管理や在庫管理、品質管理など多くの機能が搭載されているものが理想です。しかし、高機能なシステムを求めるほど、導入や運用の費用もかかります。加えて、保守が必要になる場合もあるでしょう。自社に必要な機能と導入にかけられるコストのバランスを考慮して、システムを選定することが大切です。
東京貿易テクノシステムの工程管理システム「Ignition」のご紹介
専用システムを導入すると、紙やExcelで工程管理をするよりも効率的に工程管理をおこなうことができます。
しかし、コスト面で不安に感じている方もいるのではないでしょうか。そんな方におすすめなのが、東京貿易テクノシステムの工程管理システム「Ignition」です。Ignitionは、生産ラインの監視や制御に必要なさまざまなインターフェイスとコンポーネントを搭載しており、リアルタイムでの監視や不具合発生時のアラートなど、工程管理にも役立つ機能も提供しています。その他、ユーザー自身で簡単にシステムのメンテナンスができるよう開発環境も提供しています。
また、ライセンス数の制限もないため拡張性に優れており、低コストで長期的な運用が可能です。このようにIgnitionは、お客様のニーズに合わせたシステムを短期間かつ低コストで構築できます。
Ignitionの詳細な機能は、以下のリンクからご覧ください。
まとめ
高品質な製品を生産し続けるためには、工程管理の考え方が重要です。そして、その工程管理を効率的におこなうには、専用システムの導入がおすすめです。
システム導入をご希望の方は、ぜひ一度東京貿易テクノシステムの工程管理システム「Ignition」の導入をご検討ください。
お問合せ
(メールまたはお電話にて回答させていただきます)
(オンライン会議ツールを使って直接お話しいただけます)