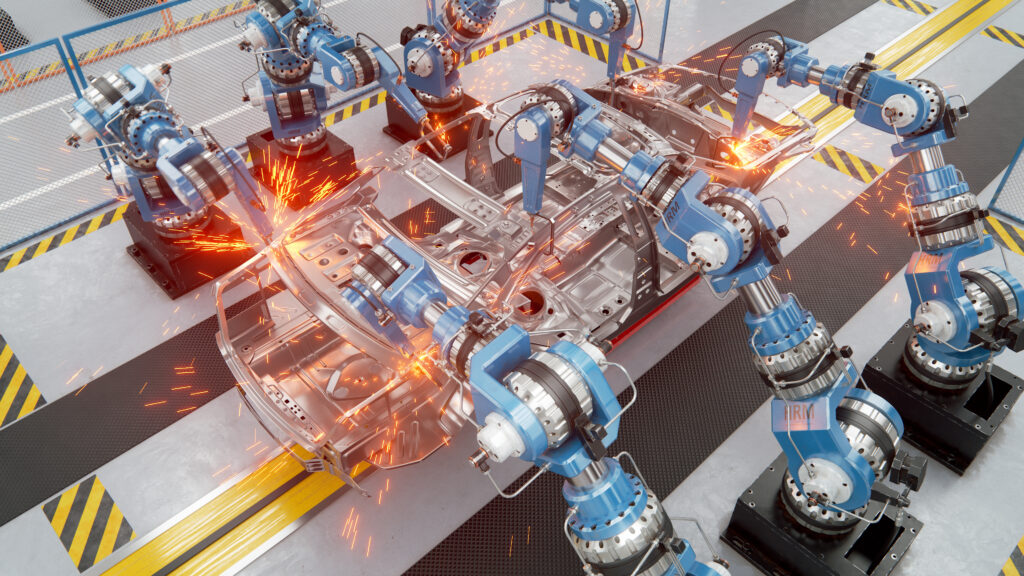
自動車製造におけるプレスパネルのスポット溶接プロセスでは、スポット溶接を実施する打順により、パネル変形に及ぼす影響が変化します。打順だけでなく、パネルを保持している溶接治具のクランプ位置や強さによってもパネルは変形します。このようなパネル変形を最小限に抑えるために、どのような打順でどのような治具を用いてどこをクランプするかを探索するのは大きな課題となっています。
課題
溶接シミュレーションを用いて打順とクランプの条件探索をされているお客様は多くいらっしゃいます。しかし、溶接シミュレーションの予測精度には課題があり、初期プランは決定しても、結局は現物の試作部品を溶接し、トライアンドエラーによる修正が必要で、生準工数増大の要因となっています。
例えば、ホワイトボデーにおける溶接シミュレーションの条件探索期間は約1.5年~2年、試作車は十数台作られてるのが現状です。1台のホワイトボデーを作るのにおよそ3カ月要し、下図の2~5のサイクルを十数回繰り返すことになるため、条件探索期間は長期化してしまいます。
- 【現状のホワイトボデーの溶接プロセス】
-
- 1. 溶接シミュレーションによる初期検討
スポット溶接の打点場所は強度に関係するため設計側、スポット溶接の打順は生産技術のため現場で決め、その初期検討を溶接シミュレーションで実施。 - 2. 試作パネルによる溶接
- 3. 変形測定
実際の変形具合を現物測定 - 4.設計値との評価
設計値(正寸)との評価をし、誤差を確認 - 5. 打順とクランプ位置の再検討
- 6. 新たな試作車を作って、実際に溶接を打つという2~5のサイクルを回している。
- 1. 溶接シミュレーションによる初期検討
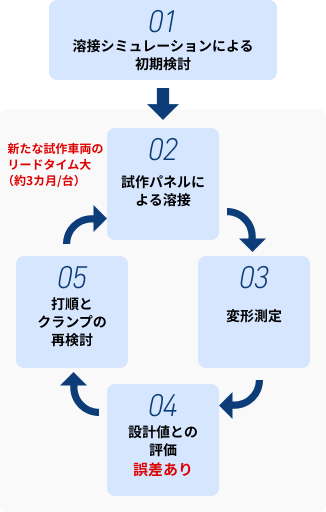
ソリューション
溶接シミュレーションの高精度化
溶接シミュレーションの予測精度を高めて、現物での条件探索をバーチャルでの探索に置き換え、圧倒的な生準期間の短縮につなげます。
- 開発工程よりも寸法評価基準が厳しい
- ツールやノウハウが異なるため、前工程のデータを利活用できない
- 現物とは異なる形状で解析している
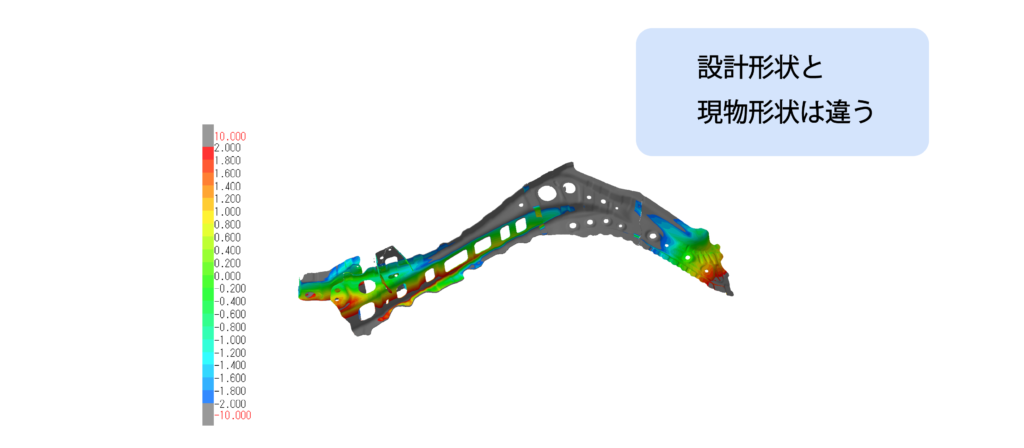
ホワイトボデーの精度目標値は±1mm、最終アセンブリでは±0.5mm。
しかし、現実の部品精度は、設計値との誤差が大きい状況も散見される。
ソリューション:REGALIS Fusion モーフィングモジュール
前工程であるプレスや、サブアセンブリの現物部品を3D測定し、その測定データにより、設計値から作成されている解析モデル(FEメッシュ)に現物の形状を反映します。
現物と誤差のない解析モデルで溶接シミュレーションを行うことで、解析の予測精度を高めることができます。
Fusionのモーフィングモジュールは解析モデルを作成するところまでをご提供しているため、お客様はこれまでお使いの溶接シミュレーションを使って現物と誤差のない解析モデルを取り込み、溶接打順や治工具の調整等によるクランプ条件を修正し、その修正案にて現物加工を行っていただけます。
これにより試作台数を大幅に削減し生準期間の短縮を実現します。
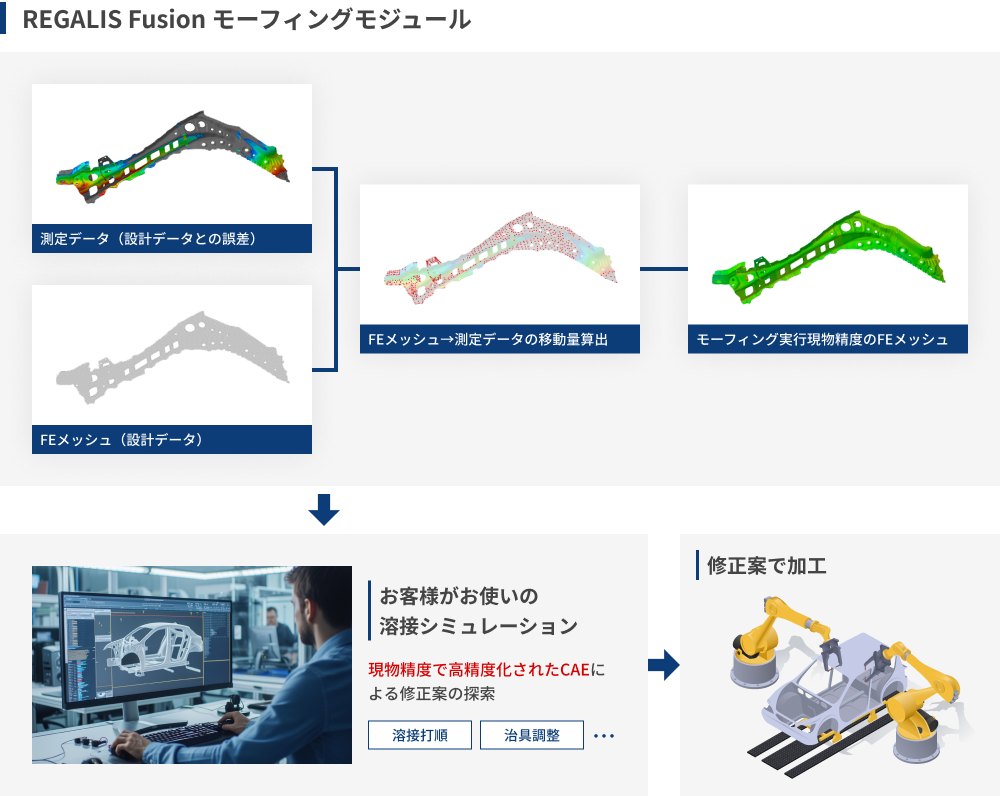
システム構成(提案例)
REGALIS Fusionに関する製品情報はこちらをご覧ください。
まとめ
このように、REGALIS Fusionを使って、はじめから現物と誤差のない解析モデルで溶接シミュレーションを実施するというプロセスチェンジを起こすことで、トライアンドエラーの回数を激減し、圧倒的な生準期間の短縮を可能にします。
実際に試作台数を3台への削減、および生準期間を半年への短縮を目指しているお客様もいらっしゃいます。REGALIS Fusionのモーフィングモジュールを追加するだけで、お客様の溶接シミュレーションの高精度化を実現し、多大な付加価値をもたらします。
詳細につきましてはお気軽にお問合せください。
弊社ではご提案できるソリューションを多数用意しております。
ぜひ、お困りごとをお聞かせください!