Traceability required in the aerospace industry
VECTORON, an arm-type 3D measuring system
Trusted by makers as “If measured by this.”
Allex Japan was established in 2009 and now is an outstanding company that has already a strong presence in the field of developmental testing or measurement conducted by major maker-companies in the aerospace industry. The areas to which they provide jigs or technology are not limited to the private sector but also they have joined in the making of airplanes for national defense or space projects. The headquarters and Technology Development Center are placed in Nagoya of Aichi Prefecture, where many of relevant enterprises gather.

Their main business at present is the design of jigs and parts used in the tests that are conducted in the course of development. Accuracy and safety that assure precise operation in harsh environments are required in the aerospace industry, and to confirm performance, tests during development must be passed.
It goes without saying that jigs and parts used in tests are expected to show required performance accurately in imposed tests. So, orders are likely to be made for jigs that are customized for a certain test and used only once rather than used in other tests many times.
Allex Japan’s strength lies in such situations. “We hope to conduct this kind of test” –to such requests from makers, it is a rare case that there already exists a jig suitable to conduct the test in question. The number of companies is very small that are involved in the whole process from a hearing with customers to learn their needs, without any prior material to embody them in design, to production to delivery. The company’s flexibility and superior technology have contributed to the company’s high reputation since the foundation.
“VECTORON,” a three-dimensional measurement device provided by Tokyo Boeki Techno-System Ltd., is used at measurement to confirm that produced jigs and parts satisfy required specifications. It was introduced in December, 2016 to enable a rapid, accurate measurement of complex figures. A test team was accordingly newly set up to arrange the in-house measurement environment.
We interviewed Masanobu Yoshihara, one of the founders and now the head of the Technology Development Division, about the motivation for choosing VECTORON, the method of its use, and its effect after its introduction.
Masanobu Yoshihara, Executive Director & Head of the Technology Development Division
After working in the aerospace and automotive industries, he established Allex Japan Inc. with Takanori Amaki, a representative director, in 2009.
Currently he takes the leadership role in the Technology Development Division. The ultimate objective of the company that he started up with Amaki from its foundation has been “to develop and produce airplanes on our own.” He believes that every job carried out each day marks steps toward that goal.

Investment necessary to survive in the aerospace industry
Could you tell me specifically the businesses your company conducts at present?
Masanobu Yoshihara(referred to as “Yoshihara”): Our main business is tied to airplanes and space technology. We are involved in design and production of jigs and parts used in developmental tests. The test types are various, including strength test, vibration test, functional test and electrical component test. Basically, we deal with all work relevant to hardware developmental tests.
After receiving an order from a customer for a specific type of test, our work starts from conceiving the jig that accomplishes their purpose. Next, we propose the figure that makes the test conductible with illustrations or other media to gain their approval, and draw the figure using CATIA, a three-dimensional design software, to prepare a drawing and go into production. In some cases, we outsource production to another company, but finally the jigs are assembled in-house and measured before delivery to confirm their satisfaction of the required specs.
VECTORON from Tokyo Boeki Techno-System Ltd. is used for the measurement in the final stage to check if jigs and parts are produced according to the drawing.
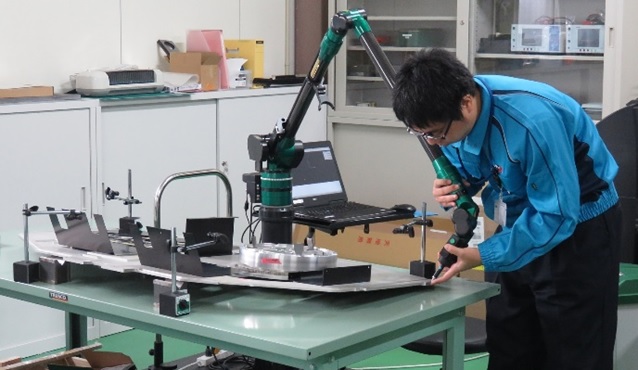
Basically, many parts undergo machining. If such machining process is outsourced, the machining precision largely depends on that of the machine in the outsourced company. Since the degree of precision is usually different from ours, we determine by measurement that the range is acceptable.
What led you to introduce VECTORON?
Yoshihara: At first, we didn’t fully appreciate the measurement in-house of products that we were involved in making. This made us initially arrange an outsourcing process for measurement, thinking that those products would be judged impartially from the viewpoint of the third party.

But as we proceeded, we found it more and more difficult to find companies that met maker’s requirements, which increase their severity year by year. So, we came to think that we must control every level including measurement on our own and started to consider the introduction of a high-precision measuring instrument.
In fact, I have experience using VECTORON in the previous workplace. Both managers in this company, I and the other manager, used to use VECTORON for collision tests in the automotive industry. We choose this company because they responded more promptly than the other companies.
We handled various types of measurement instruments at the workplace. When a part of instrument is broken, we want to get a replacement part, though we can hardly expect a prompt response from overseas companies. In the case of VECTORON, they send us spare parts in a few days or in a week. This follow-up was a great help for us at the time. It did mean a lot to us that we could receive support or customization service domestically when we needed.
Another motivation for the introduction was that I knew that the functions we wanted were equipped as default settings. I could anticipate that we could fully make use of it once it was introduced.
What functions do your company expect?
Yoshihara: At least, a measuring function to check if the dimensions are according to the drawing is satisfactory. Some measurement devices can work just by placing products in them, though for us their measurable range is narrow. On the other hand, an arm-type instrument like VECTORON can measure very large objects by displacing the position. Sometimes we want to know a coordinate rather than investigating the whole. Just knowing an accurate positional relationship is enough even if we don’t know all the aspects. VECTORON meets our such needs.
It cost a lot, but we thought we should own a high-precision measuring system to think of surviving in the aerospace industry. In the field of aerospace and defense, there is JIS9100, a very severe standard of JIS, which is also applied to our products. We can outsource the production of parts, but it is Allex Japan that is regarded as the final checker and an accountable manufacturer. We have to arrange an environment in which we can answer to the questions regarding the reliability of test or precision. If we are to engage with the aerospace industry seriously, we judged that it would be an investment that we had to make.
Trust from customers enhanced by the reliability of this instrument.
It seems that the required levels of safety and precision are high for aerospace products.
Yoshihara: In the aerospace industry, traceability, that is, being able to trace the course of manufacturing, transportation and delivering, is very crucial. You must issue a “Traceability Chart” to show that you use the machines that have passed a test certified by the test institution for inspection. This makes outsourcing of some parts impossible.
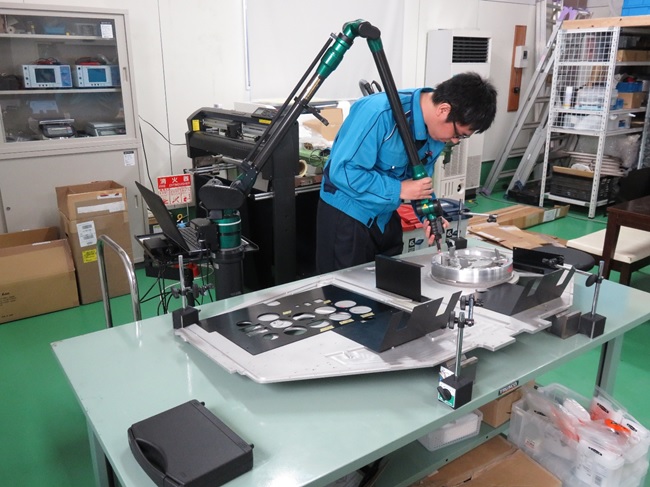
To be precise, we can do outsourcing, but the procedure becomes very complex. We are asked to submit a large amount of documents, increasing the preparation cost. Preparing works for outsourcing takes time that is already limited by deadline as well. If defects are found in parts, time will be consumed for returning, resending and reexamination of the parts. Operations were often bogged down in such conditions, so we wanted to establish traceability in-house, too.
You mean it is also useful to make customers convinced.
Yoshihara: Yes. In the past, we conducted measurements that passed the test, but since it was analog we now have a feeling that trust from customers has been enhanced since the introduction of VECTORON. Examining with the accurate instrument to output a reliable test performance certificate. This makes customers feel more confident in the results than before. It is safe to say that VECTORON is a device that makes customers convinced of the reliability of the measurement.
Have you found any merits through the actual measurement performance?
Yoshihara: It is very useful when measuring angles. When measuring an angle in a certain place, it is much quicker to measure the planes to calculate the angle rather than directly measure the angle in analog.
As another merit, by setting referential planes and measuring distances to set a coordinate, we can easily find planes by assembling them. As I became accustomed to using the instrument, I came to be able to assemble spaces in my mind, which makes work more and more efficient. Even when there is something lacking or a need to add a convex-shape element, decision-making became quicker since their positions are grasped instinctively.
Could you tell me your future vision for the company?
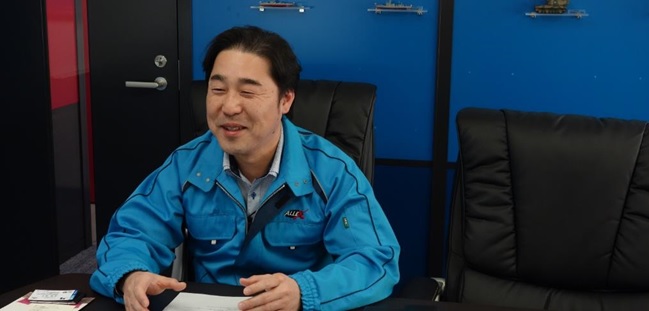
Yoshihara: Regarding measurement, to be able to measure more accurately and quickly, we need the sense and capability of humans, not only high-performance equipment. So we endeavor to improve the measuring skill of the test team so as to fully make use of the features of VECTORON. Actually, Allex Japan does not employ a sales person. This company is operated only by engineers who receive contacts from customers and make sure to get results. That is to say, ideas, technology, and the resourcefulness of personnel constitute this company.
Our final aim since the foundation is “to be a company that is capable of producing airplanes by itself.” If you try to build airplanes in Japan today, you have to procure many components such as engines, air-conditioning systems, or fixtures from overseas. The major motivation to establish this company was to get free of that situation and build airplanes on our own.
Recently, we have installed a 3D printer with the purpose of making a flight simulator for pilot training in-house. We regard every project as one step toward the goal. We would like to further develop our skills to join in more difficult projects for the growth of the company while continuing to deliver good services to customers.
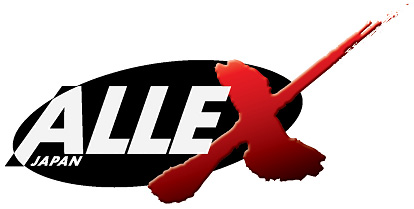
Allex Japan Inc.
Established in 2009, the company has been involved in developmental test and measurement contracted business, jig design and production, aircraft electrical work, rigging, design, test consulting, and measuring device proposal and sale in the aerospace industry. Its three principles, “to bring about innovation for the creation of a better future,” “to challenge a new field where natural science and technology are integrated,” and “to grow and prosper together with the society at large for its general welfare,” are being steadily realized and the company, working behind the scenes, has become a support for the domestic aerospace industry.
【Product used in this case study】VECTORON