CMMs are used for positioning welding workpieces.
Built a system that performs workpiece positioning and welding by robot without using a dedicated jig for each car model.
The predecessor of Aisin Shiroki Corporation was Shiroki-Kinzoku Kogyo K.K., founded in 1946. It was established as a subsidiary of Shiroki-ya, a long-established department store located in Nihonbashi, Tokyo. Initially starting out by manufacturing pots and kettles, the company now manufactures and sells door frames and window regulators used in automobiles, and operates in Japan and overseas.
Our major customers include Toyota, Nissan, Suzuki, Honda, Daihatsu, Isuzu, Mitsubishi, SUBARU, and most other domestic automakers. “Roll forming”, which creates hollow parts from a single metal plate, requires difficult curved surface machining and this Aisin Shiroki’s technical capabilities have been highly evaluated for many years.
However, in recent years, the speed of technological innovation in the automotive industry has increased, and in addition to providing parts processing that is fast, inexpensive, and of high quality, it is necessary to respond to a wide variety of vehicle models and devise manufacturing technologies. In addition to improvements in physical machining technology, new machining processes and equipment must be developed in conjunction with DX and IoT.
To meet this requirement, Aisin Shiroki launched a “welding jig-less project” utilizing laser-type CMMs and robots, starting with the machining of door frames for an old model that had finished mass production. The devices selected from a variety of devices were the Leica Laser Tracker AT960, Leica AS1 scanner, and Leica T-Mac from Tokyo Boeki Techno- Systems and the 3D measurement solution PolyWorks Inspector™.
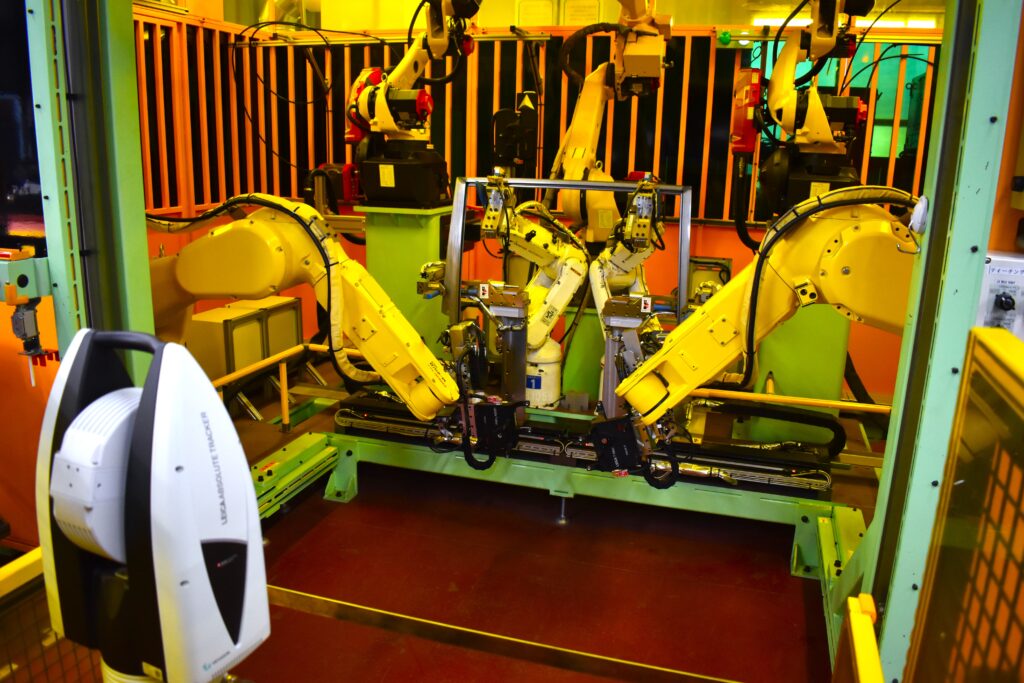
Measuring with Leica Laser Tracker AT960 and Leica T-Mac
The introduction of the system was in July 2021, but more than a year before, Tokyo Boeki Techno Systems and three other companies supported the new project as a team, and a robot-based jig-less system was realized. Full-scale operations began in the spring of 2023. In this interview, we asked for more details about the project’s background and data application.
- The Challenge
-
- Welding jigs for old models after mass production require long-term storage and take up a lot of space.
- Processing old models parts for repairs istime-consuming and difficult in small quantities, making it difficult to make a profit.
- Machining work requires detailed positioning for each car model, and eventually the company would like to fully automate the process.
- Solution
-
- Using a 3D measurement system to adjust the space between parts, eliminating the need for fixed welding jigs.
- Work efficiency is improved based on measured values, rather than on the skills of individual technicians.
- Achieve full automation by combining CMMs, analysis software, and robots
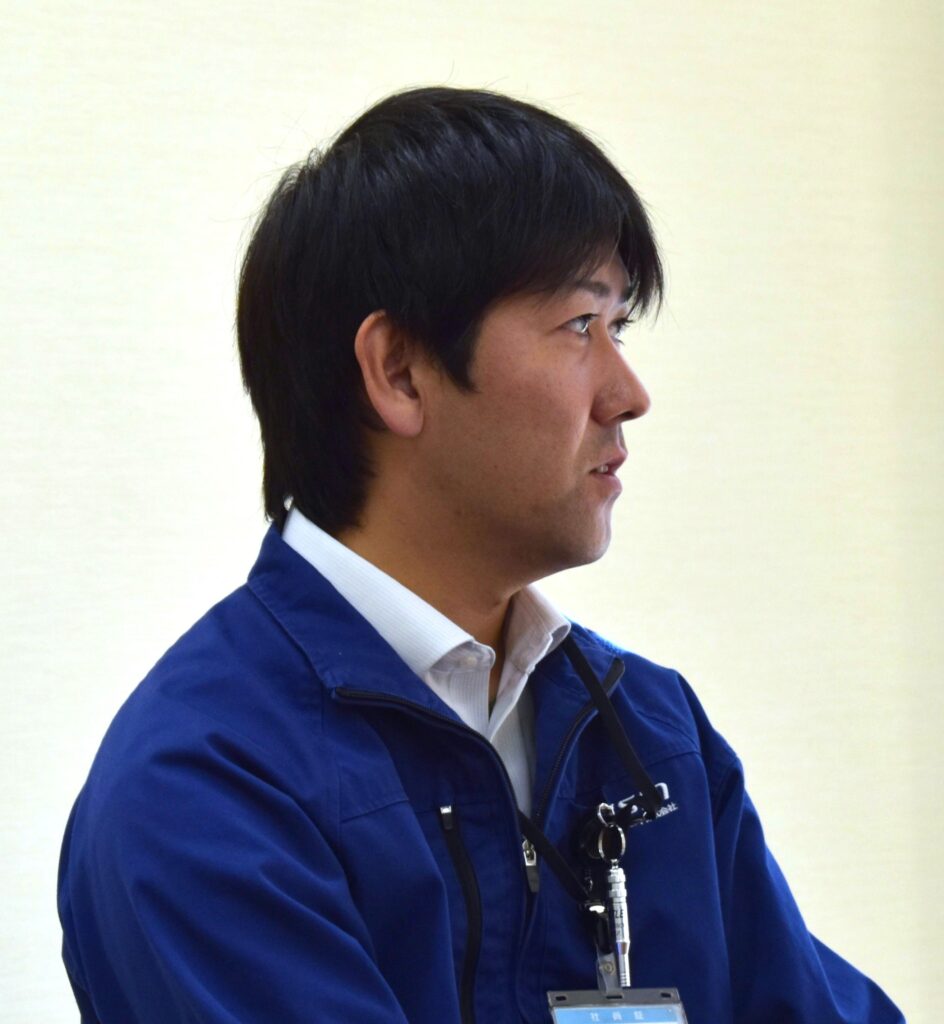
Mr. Uchiyama, Door Frame Development Office, Exterior Components Production Engineering Department
Mr. Uchiyama is engaged in the development of manufacturing equipment and lines for door frames (window frames) attached to automobile side doors, and has researched how to efficiently, inexpensively, and with high quality manufacture frames of different shapes for each car model, and realized a jig-less welding system built with a 3D scanner and robot.
Not for Quality Measurement, but for Spatial Measurement of Machining Processes
This time, we have introduced the Leica Laser Tracker AT960, as well as the Leica AS1 scanner and the Leica T-Mac, which enable precise non-contact measurement. What kind of work are they used for?
Our usage may be unique. Normally, it would be used for quality measurement after the product is completed, but we have introduced the laser tracker in our parts welding process.
Automobile door frames are assembled by welding several types of workpieces. The shape of the workpiece varies in detail from car model to car model, and the welding angle and position must be adjusted each time. For many years, a fixed jig dedicated to each car model was used on site to ensure accurate welding. The workpiece was fixed on the jig and welding was performed on it.
However, this jig was necessary for each door of each car model, and its size was large. Even after the mass production of a certain car model was finished, we needed to keep the jig because we needed to produce service parts for repair parts, etc. Whenever we received small orders, we had to pull out the jig, adjust it, and produce it. Storage must be an issue for all companies because the number of jigs increases with the number of car models.
To solve this problem, we decided to build a new system that does not rely on fixed jigs dedicated to a specific car model. The key to this was the application of CMMs.
Could you tell us more about how you are using it?
First, the workpiece to be welded is gripped by a robot hand or general-purpose jig. Here, a 3D measurement system is used to measure the spatial coordinates of the parts by comparing the dimensional values from the CAD data of the workpiece and the tracker’s measurements. By using these values to position the workpiece, it is possible to weld at the exact angle and position every time without necessarily relying on a fixed jig dedicated to the car model.
Even a fixed-type jig dedicated to a specific car model needs to be adjusted as it wears out over time or parts are replaced, and the level of adjustment differs from operator to operator.
However, if the coordinates are based on measured values, they are not affected by the condition of the jig or environment, and the operator’s skill level is not affected due to the nature of the calculation based on numerical values. If data is transferred to a robot to automate the process from positioning to welding, efficiency can be greatly improved since there is no need for a jig dedicated to a specific car model.
You can build very convenient system.
I have heard that this system itself has been conceived and challenged by various companies for some time. However, it has been difficult to realize this system due to several issues.
First, there is the issue of the accuracy of 3D measurement system. One of the characteristics of the device is that it can measure a small area with high accuracy, but the accuracy drops when the area is large. Since door frame workpieces are relatively large, the issue is how to ensure accuracy.
Second is the issue of accuracy on the part of the robot receiving the data. Even if we can give numerical instructions, it is difficult to keep the robot’s movements within the range of error we require. Continued use of the robot will cause wear on the robot’s own gears, so misalignment and other factors must also be taken into consideration. It would be nice if the robot could perform high-precision positioning from the start, but the technology is very advanced.
We consulted several companies that had the technology, but they all refused, saying, “We can’t do that. ” However, there was one company that was willing to give us a try. That was Tokyo Boeki Techno-Systems.
You got offer with flexible ideas to solve the problem.
Only one company had a positive response.
We discussed with them what kind of system we wanted to build, and they introduced us to the combination of Leica laser tracker and “PolyWorks Inspector™”. At the time, it was before we had purchased the laser tracker, so we were not even a customer. Even so, we really appreciated the fact that you were so accommodating and did your best to find a way to help us.
For the first challenge, we were offered and adopted the Leica Laser Tracker AT960, which can measure a wide area with high precision together with a small camera-type 3D scanner. By calculating data from both, all 3D scan data can be displayed in the Laser Tracker coordinate system. We felt sorry because the camera-type 3D scanner is not a product of Tokyo Boeki Techno-Systems, but they said, “If it improves the accuracy,” and thanks to them, we also have more freedom and it is easier to handle.
Regarding data handling, it was Tokyo Boeki Techno-Systems that suggested a way to match the original CAD data with the measured point cloud using “PolyWorks Inspector™”. They gave us detailed tips on how to set up the system so that even those of us with no technical knowledge could use it.
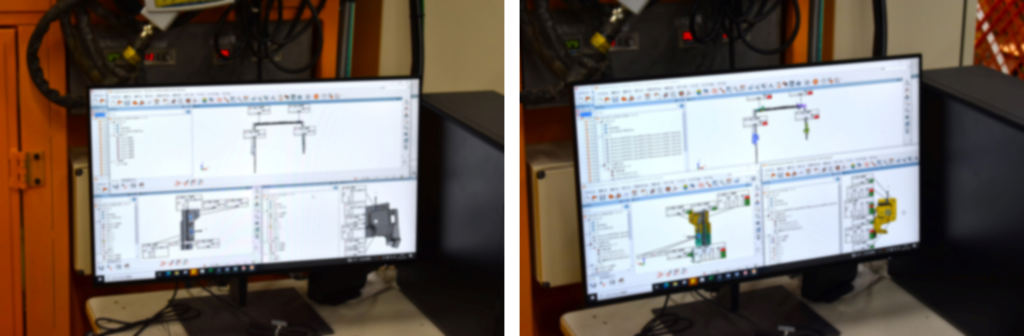
You were provided specific solutions that fit the site.
Yes, we were. For the robot control, we asked other companies to join us, and a team of five companies worked on the project. The 3D measuring machine and analysis software from Tokyo Boeki Techno-System, robot control technology from ROBOSHIN, concept proposal and collaboration from TAMADIC, and support of general-purpose figs and equipment from TACT SYSTEM , made this technology a reality.
In terms of robot control, which was the second challenge, ROBOSHIN was able to put together a high-precision positioning program that utilized a laser tracker to enable high-precision positioning of the robot. We believe that this would not have been possible without this team.
A difficult development project was carried out by a fun team.
The project required a lot of budget and space, with laser trackers, non-contact and contact options, and the introduction of a fully automated system, but did you have any internal opinions?
When we were considering building a system in 2020, the former president encouraged us to take on the challenge, no matter how much money it would cost. The current president and board members also continue to strongly support us. I believe that they foresaw that new technology would always be required in the ever-changing automotive industry and that highly versatile technology could be applied to other mass production lines.
In April 2023, we will be in full-scale operation and have begun replenishment production of older models. Since the process will change from adjusting physical objects to making adjustments based on numerical calculations, we are in the process of adding models and promoting production activities together with the understanding of everyone on site. This is a technology that will surely come to life in the future, so we are asking them to understand this as a transitional period of change.
You made the decision to introduce this technology as a future technology.
Yes, we did. In addition, it was a great experience for me to be able to enjoy the development process with my team. Usually, when a project has a major development challenge, we tend to look backward or shrink away from the project because of the fear of failure. In this project, we all discussed development ideas in a congenial manner and proceeded with the mindset that even if an error occurred, we could solve it, and if we couldn’t, we could find another way.

At first, I myself thought, “If everyone says it’s impossible, it may be impossible, but let’s just try until we can determine whether it is possible or not. However, now I feel a sense of accomplishment that I was able to build a new system that is not yet available anywhere else, through repeated trial and error while talking with the sales and technical staff of Tokyo Boeki Techno-Systems as well as people from other companies.
I was taught from almost zero knowledge and technology. I think Tokyo Boeki Techno Systems’ strength is their deep knowledge not only of devices but also of analysis software. We were greatly helped by their application skills and ideas.
I think the timing of the project, company’s decision, and my encounters with Tokyo Boeki Techno-System, ROBOSHIN, TAMADIC, and Tact System were all fateful. There is no doubt that we could not have done it without any of them.
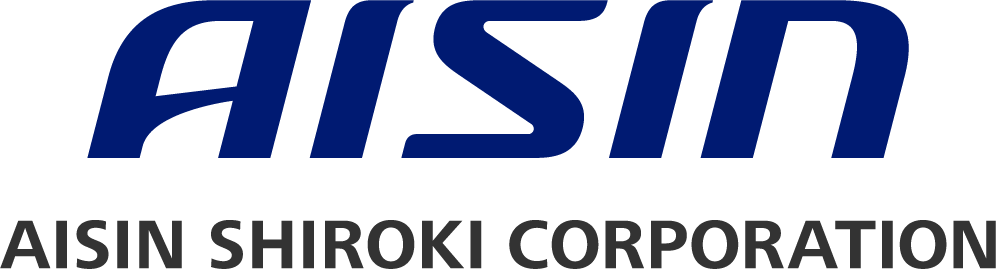
AISIN SHIROKI COPRATION
The company was founded in 1946 as “Shiroki Metal Industry Co., Ltd.”, a subsidiary of the long-established department store “Shiroki-ya” in Nihonbashi, Tokyo, and changed its name to “Aisin Shiroki Corporation” in 2023. Currently, the company manufactures and sells automotive interior and exterior parts such as door frames (window frames), window regulators (window lifting devices), door locks, and moldings in Japan and overseas. The company emphasizes production technology and monozukuri (manufacturing) capabilities, and is also working to develop new technologies to keep pace with the rapidly changing automotive industry.