The 3D measurement with a micron-level precision shines in a large-scale experimental system that supports fundamental physics.
Tokai-mura village, Ibaraki Prefecture, has a research facility with the world’s top performance in a huge ground of 65 ha, equivalent to 14 times the area of the Tokyo Dome. It is called Japan Proton Accelerator Research Complex (J-PARC). It launched its operation in 2009, as a joint project between the Japan Atomic Energy Agency (JAEA) and the High Energy Accelerator Research Organization (KEK).
This facility has been used for experiments and studies using “high-energy proton beams.” Protons, which are created with hydrogen gas, are accelerated in a large accelerator to 99.98% of the speed of light and are used for irradiation to a target atomic nucleus. Various secondary particles generated from the collision energy between the protons and nucleus are used for cutting-edge science.
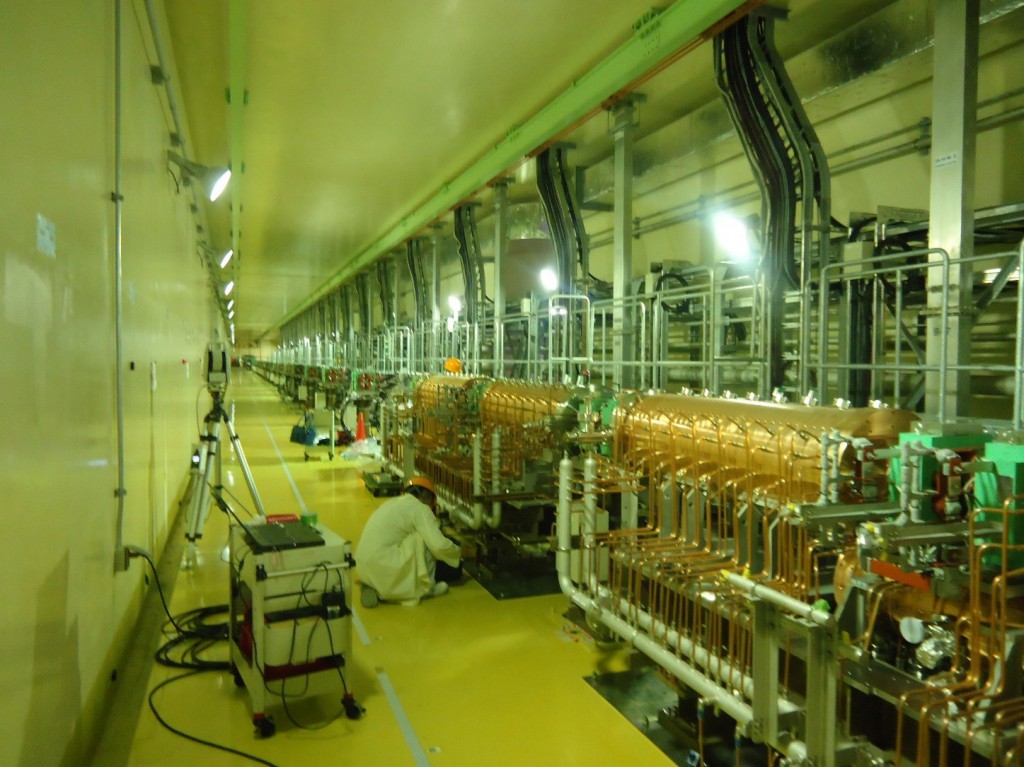
Dr. Takaaki Kajita at the Institute for Cosmic Ray Research of the University of Tokyo has proven that neutrinos have mass using “Super-Kamiokande,” a neutrino observatory in Kamioka-cho, Gifu Prefecture. It is widely known that he was awarded the Nobel Prize in Physics in 2015. At J-PARC, researchers are currently using high-energy proton beams to create artificial neutrinos and shoot them into Super-Kamiokande located 295 km away for advancement of neutrino research.
In order to accelerate high-quality as well as high-energy proton beams, it is necessary to align several hundreds of electromagnets precisely for a long distance (called precision alignment). If the alignment precision is low, the beam quality decreases, being unable to generate high-energy beams. As a solution to this problem, they are using Tokyo Boeki Techno-system’s Leica Laser Tracker AT401. They have adopted the equipment since 2011, with a total of four devices including a high-end model within J-PARC.
What kind of measurement is conducted at the cutting-edge research facility J-PARC? We talked to Mr. Norio Tani and Mr. Takatoshi Morishita at the accelerator division in charge of design and management of equipment.
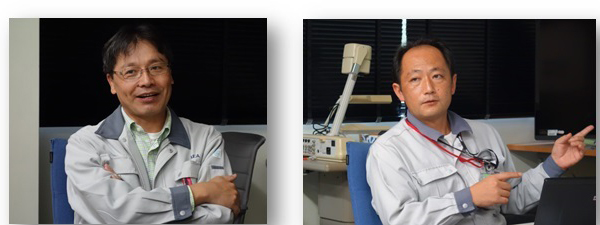
They are involved in design and development of large accelerators: Mr. Tani is in charge of a cyclic accelerator, “3 GeV Rapid Cycling Synchrotron (RCS),” and Mr. Morishita is in charge of a linear accelerator, “Linac.” They conduct regular maintenance and adjustment to maintain the beam lines of the high-energy proton accelerator.
Covers not only industrial applications but also researches about the mysteries of space as well as material science
Interviewer: What kind of research institute is J-PARC?
Mr. Tani (T): Everything surrounding us consists of invisible particles, called atoms. Each atom has a nucleus, which has protons and neutrons in it. Since these are extremely small pieces of matter, it is very difficult to investigate them. J-PARC allows us to study structures and movements of matter at an atomic level.
For that purpose, we use high-energy proton beams. At J-PARC, we use a large accelerator to accelerate protons generated from an ion source and make the proton beam collide against a target at a speed close to the speed of light. Then, the nucleus of the target dissociates into smaller secondary particles, including neutrons, mesons, and neutrinos. Using these secondary particles, you can investigate inside an atom or the structure of an item of matter.
For example, light elements, such as lithium, are hard to be visualized using an electronic microscope and also hard to capture with an X-ray. However, neutrons can capture these elements. In the research of lithium batteries, neutrons are generated and used to follow detailed reaction processes of lithium. Once we understand more about a phenomenon that has been invisible, we will be able to obtain a higher-performance lithium battery.
Mr. Morishita (M): When you take a photo, the amount of light is key. For this research, the amount of the secondary particles dictates the quality and speed of experiments. If you could generate a large amount of neutrons, you would be able to complete an experiment, which has been taking several days, in one day or even a few hours. The stronger the proton beam, the more the amount of the secondary particles. Therefore, J-PARC is aiming to supply high-energy beams accurately.
I: When I first came here, I was surprised by the size of the premises, in which we need a car to get around. I guess the accelerators must be huge.
T: On the premises, there are three large accelerators and three experimental facilities. These accelerators are connected with each other. We gradually increase beam energy from the upstream accelerator and divide the beam to each experimental facility based on their demands.
The linear accelerator, ”Linac,” is located upstream of the other ones. With a total length of about 330 m, this accelerator generates protons from an ion source, accelerates them to about 70% of the speed of light, and hands the beam over to the next cyclic accelerator “RCS.”
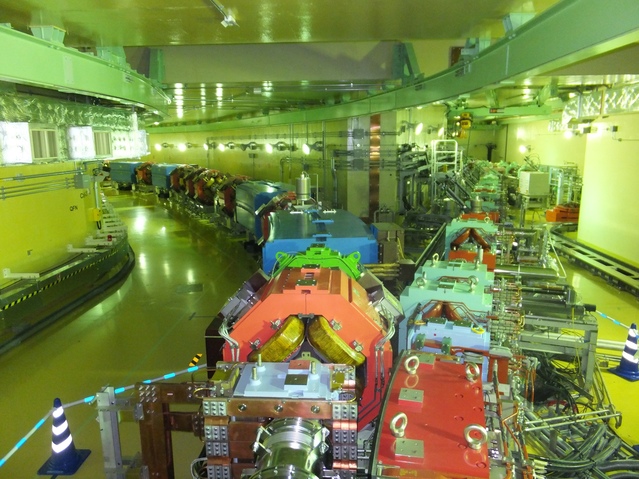
RCS’s complete circuit is about 350 m, which allows a beam to be accelerated to 97% of the speed of light. From this point, the beam line is divided into two beam lines. One goes to the Materials and Life Science Experimental Facility, where researchers use neutrons and muons to conduct industrial research, such as the above-mentioned lithium battery, as well as other research, including protein structure elucidation and agricultural studies.
The other one goes to a cyclic accelerator “50 GeV synchrotron (MR),” which has a complete circuit of about 1,600 m and a diameter of 500 m, making it Japan’s biggest proton accelerator. Further down, there is the Neutrino Experimental Facility and Hadron Experimental Facility, where researchers are engaged in basic studies, such as those on the origin of the universe and the birth of matter.
This arrangement of various facilities diverging the main beam line is unique to J-PARC.
Laser Tracker for precision measurement in a large range
I: I didn’t know Laser Tracker AT401 is used in such a cutting-edge science.
M: We perform maintenance on all of the whole accelerators, taking three months per year. I am in charge of the linear accelerator, which is set in a place 13 m below ground, which includes about 60 components for beam acceleration and about 300 large electromagnets for transporting the beam. I always had a difficult time to align them precisely in a straight line.
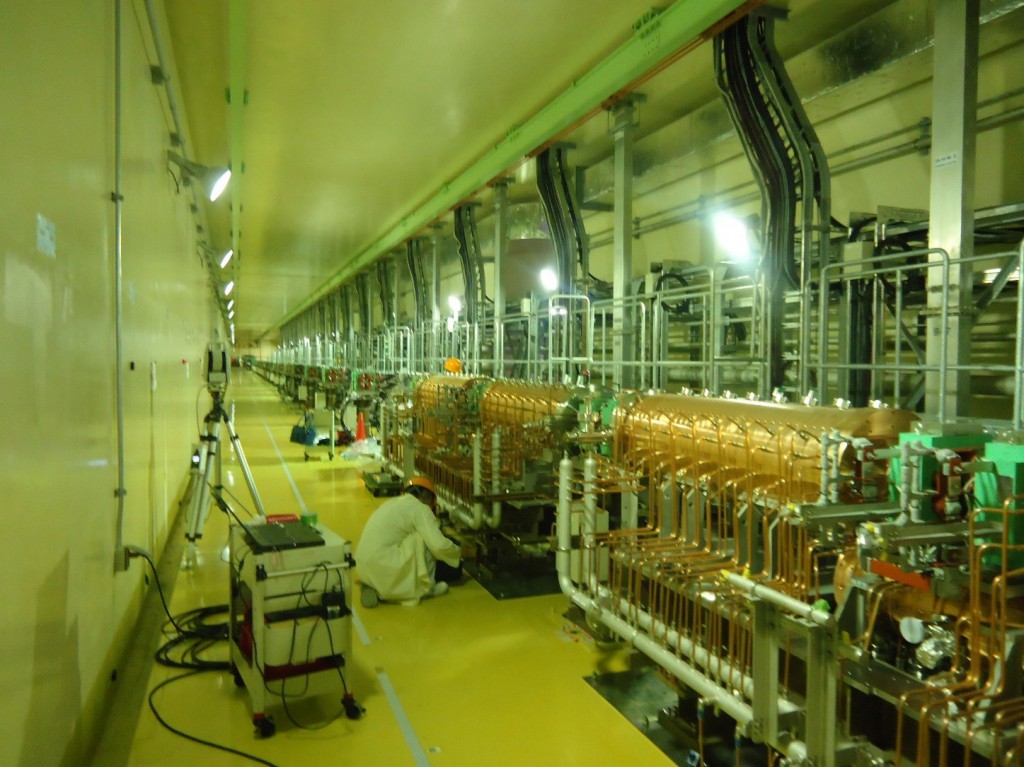
Before we introduced the laser tracker, we used to use a type of telescope, called “alignment telescope,” which was developed to align objects in a straight line. This telescope-based method is useful when I want to align equipment at intervals of about several micrometers within a zone of about 10 m.

For the accelerator, however, the installation interval is also important. Without proper periodic alignment, the beam cannot be accelerated. Therefore, we need to use a tool to measure distance and interval, such as Total Stations and micrometers.
T: Within the zone of beam transport, a beam is bent, so we need a tool that can measure both angles and distance at the same time, such as Theodolites and Auto-Levels. In other words, since the above-mentioned devices have different advantages and disadvantages in different applications, we used to use the most suitable one for a particular purpose. I could show my skill as a person in charge of alignment, but it was time consuming.
In that regard, the Laser Tracker AT401 is very reliable when I have to efficiently align components at a high accuracy in a large-scale facility. This tracker can measure angles and distance at the same time, with the measurement range over 100 m and measurement accuracy of several dozen µm or less. AT401 is also used for position measurement of electromagnets and cavities at the cyclic accelerator that I am in charge of.
M: Another deciding factor to adopt AT401 was the combination of the implementation timing and the features. This facility was badly damaged by the Great East Japan Earthquake in 2011, with the beam lines ruptured and the building cracked. The most serious problem was that the floor of the linear accelerator tunnel became under water.
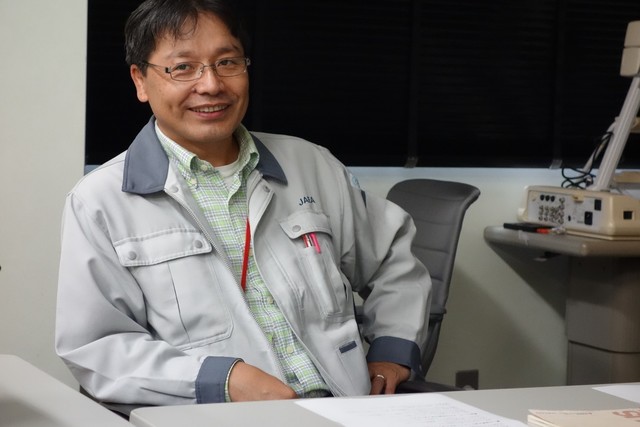
We had to restore the facility for our research, but the device we used to use, Leica LT600, couldn’t be used as the device body and the power controller are connected with a cable. If it is used in a water-soaked place, it could cause a power failure. So, when I heard about a battery-based laser tracker, I immediately went for it. I believe there were no other suppliers who had a high-performance wireless type. I think I almost immediately decided on it.
AT401 is lighter yet higher performance, which attracted me the most.
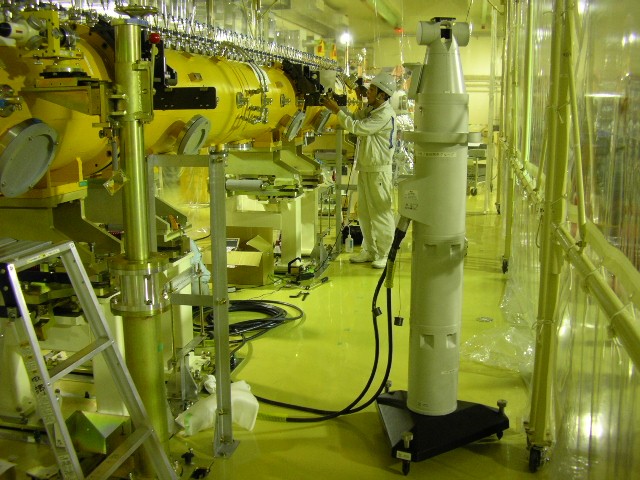
I: What did you think once you actually used AT401?
M: As our maintenance time is limited, we are still using both AT401 and LT600 to shorten the time. But I can tell the amount of work AT401 can complete is way above that of LT600. During measurement, if a reflector is out of sight from a laser tracker even at a blink, we have to re-capture the laser. With the old model, a small error occurs in this situation. Therefore, we have to deliberate about how to move reflectors so that laser capture won’t get cut off during measurement on complicated components.
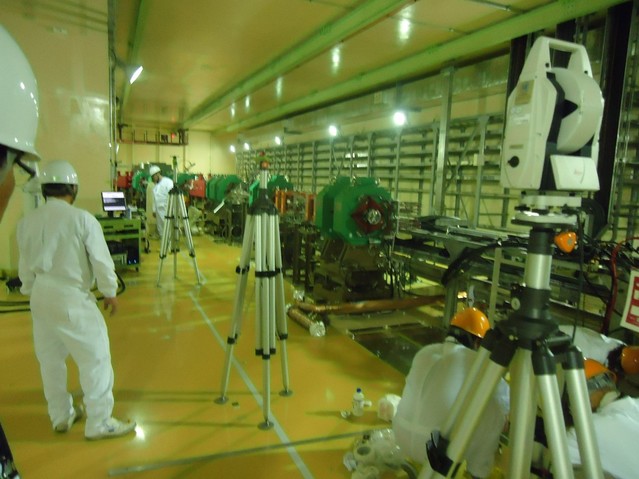
But thanks to the improvement of tracking performance, the problem of errors at the laser re-capturing is gradually being resolved. With AT401, the PowerLock technology prevents the laser tracker from losing reflectors. It is very convenient.
T: What I really appreciate about AT401 is that the maintenance can be almost completely done within the country. Laser trackers are convenient, but in the past, the maintenance for them had to be done outside the country, which made me worry about the availability at a time of emergency. However, I heard that Tokyo Boeki Techno-system can provide all the maintenance work under the same conditions as Leica, including laser exchange and prism correction. If something happens, I can consult with the company and they can support me. This is the biggest support for me.
I: The linear accelerator is more than 300 meters long. How many measurement points do you have to set?
M: A total of about 300 points. In order to achieve accuracy of several dozen µm, we have defined “a measurement zone” as being “within 10 m front and back of a tracker.” After completing measurement of one zone, we have to move a laser tracker so that some measurement points can overlap, and then connect the coordinates to see the whole linear shape.
There are about 15 measurement points in one zone. We repeat measurement to eliminate any large error and/or average the measurement values to reduce any error. At the 300-m linear part, we measure 60 zones while moving the tracker, resulting in measurement of a total of close to 1,000 measurement points.
T: At J-PARC, before installation of the accelerator, we determine and mark observation points required for maintenance. After the installation, we use the observation points for maintenance and management. The accuracy for the 3 GeV Rapid Cycling Synchrotron is highest; we adjust it at an accuracy level with an error within ±0.2 mm.
I: Is the error really only within ±0.2 mm for the system of more than 300-m in length?
T: Yes. We discuss the installation accuracy of the system at the early stage of the project and in general, it should be set to the highest achievable accuracy level for the times. It is because, just like the system production accuracy and operational stability, alignment error can affect the performance of the accelerator. At research facilities, we research available measurement technology under existing conditions, at the time of design, so that the high accuracy can be maintained for a long time. We have to think “how the equipment should be placed in order to successfully utilize the technology” to create a system while considering the highest level of maintenance from the start.
M: However, it is impossible to achieve accuracy with zero error, so we also have to test and place a tool to correct any adverse effect on a beam by alignment error. The smaller the expected error, the lower the number of tools for correction and their performance, thereby leading to cost reduction.
T: In addition, the measurement conditions keep changing due to several factors, such as temperature, humidity, and the earth’s crust; therefore, error is inevitable even if we aim for 100% performance in the stage of design. Design development researchers including me try to make a design that can accept some level of conditional changes. However, it is true that the more accurate the position of a system, the higher the output intensity we can apply. The laser tracker is vital for us to maintain the quality of the facility.
About the Japan Atomic Energy Agency
Established in October 2005 as an independent administrative agency by merging the Japan Atomic Energy Research Institute and Japan Nuclear Cycle Development Institute (Cycle Institute, former Power Reactor / Nuclear Fuel Development Corp.), the agency was reorganized as a National Research and Development Corporation in April 2015. As Japan’s only comprehensive nuclear research and development organization, it conducts research and development on nuclear safety improvement and nuclear fuel cycle. There are five R & D departments and nine bases in Japan.
【Product used in this case study】Leica Laser Tracker