A non-contact 3D scanner was used to make precise model of cultural asset in Wakayama,
and produced a “substitute Buddha statue” in cooperation with a museum.
The activity was awarded the Furusato-zukuri Grand Prize Group Award by the Ministry of Internal Affairs and Communications.
Wakayama Technical High School was founded in 1914 as a prefectural technical school.
In 1948, the school merged with the Prefectural Nishihama Technical School, and in 1953, it was renamed to its current name, and is known as one of the largest public technical high schools in Japan.
The Industrial Design Department, newly established in 2007, teaches the importance of connecting not only to design but also to manufacturing, and has been producing human resources to support local industry. Since 2009, classes using 3D printers and non-contact 3D scanners have been developed, and the weekly research class, which is mainly attended by third-year students, includes a wide range of activities that go beyond on-campus training.
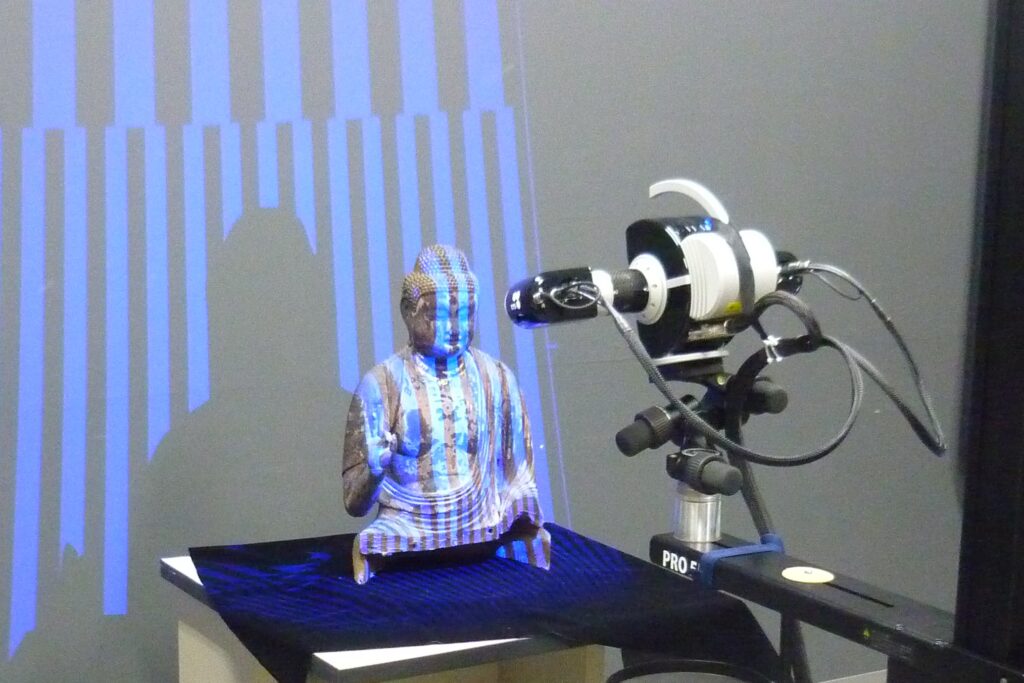
One of the school’s unique and unusual activities is its use of 3D technology to protect cultural assets. In Wakayama Prefecture, which is home to many historic temples, shrines, and cultural heritage sites, a recent surge in thefts of Buddha and God statues have been source of concern. The Industrial Design Department, in cooperation with the Wakayama Prefectural Museum, has begun to produce “substitute Buddhist statues” to replace those stolen statues.
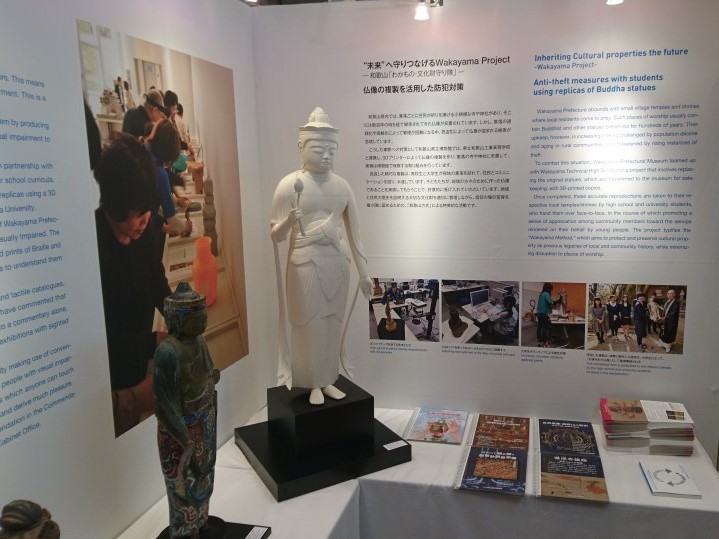
Wakayama Prefecture’s exhibition booth in the main venue
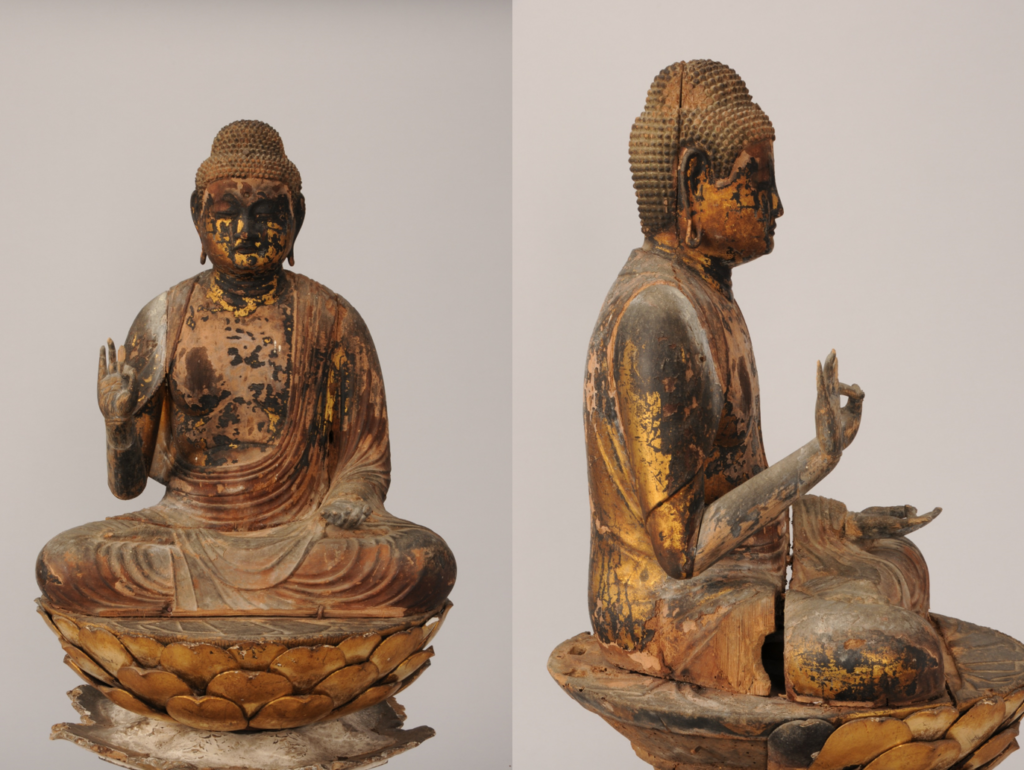
The Industrial Design Department has long been involved in activities such as “universalization of museum exhibits” that are friendly to the visually impaired through the “creation of replicas of cultural properties that can be touched,” and since 2012, the “substitute Buddha statue” project has been promoted in full-scale collaboration among museums, local residents, and schools.
In February 2023, Wakayama Technical High School received the “2022 Furusato-zukuri Grand Prize Group Award (Commendation by Minister of Internal Affairs and Communications)” from the Ministry of Internal Affairs and Communications in recognition of these activities. The activity is supported by Tokyo Boeki Techno Systems’ FLARE System, a camera-type non-contact 3D scanner.
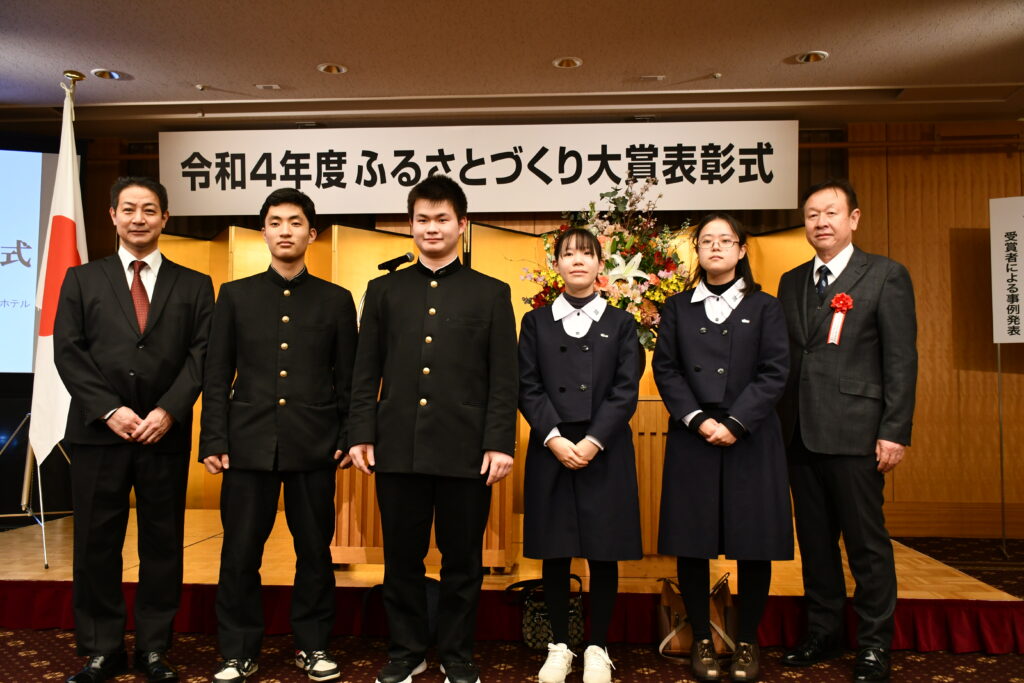
We interviewed Mr. Kodama, who is in charge of guiding the activities, and asked him about the use of FLARE in the educational field and the “Substitute Buddha Statue” project in detail.
- Challenges
-
- To establish a new industrial design department, introducing new equipment that is socially acceptable.
- To create shape data of objects (cultural assets) as precisely and accurately as possible.
- To make the equipment useful also for high school students’ education.
- Solution
-
- Introduced a 5M non-contact 3D scanner along with a 3D printer when the department was newly established in 2007.
- In 2021, a new model capable of scanning at 12M was introduced to enable more precise reproduction.
- Combining practical training in the classroom with cultural heritage preservation activities, activities that foster student satisfaction becomes possible.
Mr. Yukimune Kodama, Head of the Industrial Design Department
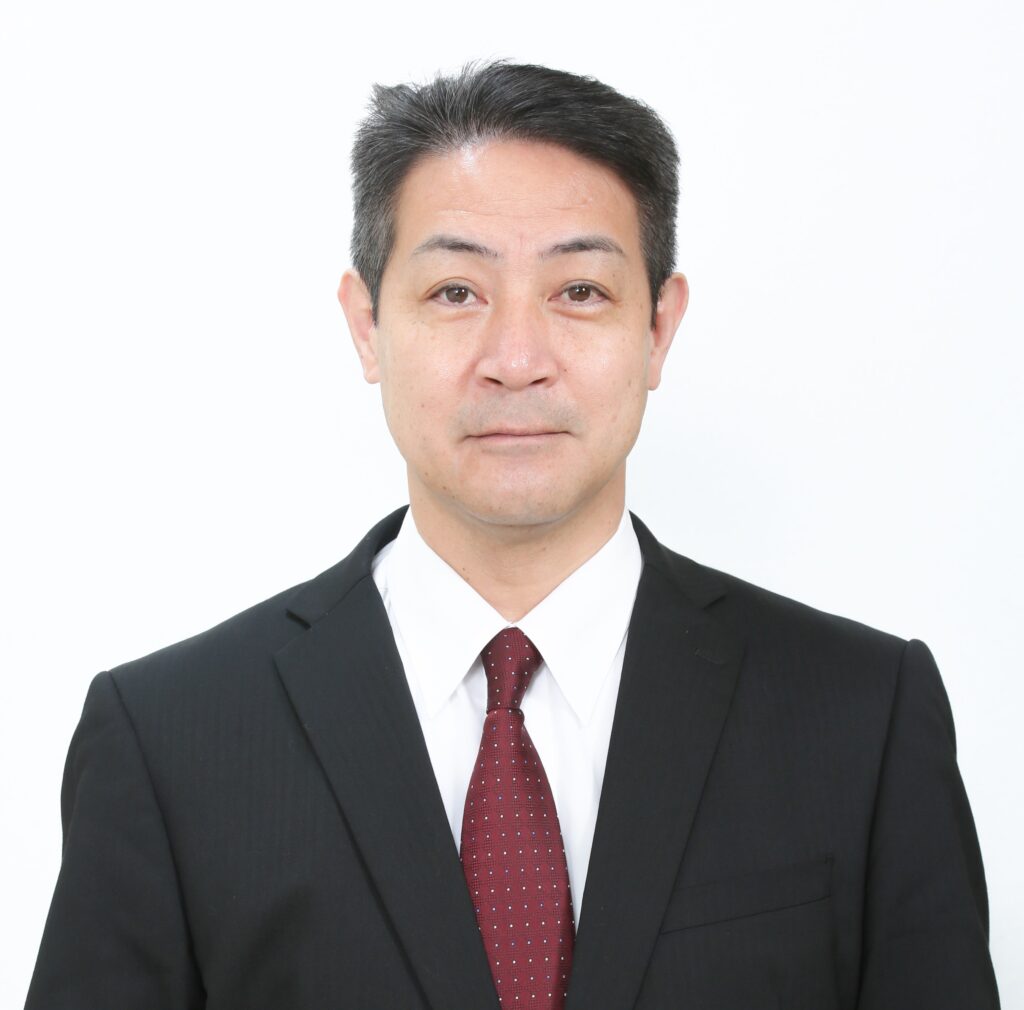
Mr. Yukimune Kodama was appointed to this position in 1994. After teaching in the Electronic Machinery Department and Interior Design Department, he has been in charge of the Industrial Design Department since it was newly established in 2007. He teaches students how to operate the 3D printer and FLARE in the weekly research class, and is also in charge of the school’s cultural asset preservation activities.
Project to Protect Wakayama’s Cultural Properties and Beliefs: “Omigawari-Butsuzou (substitute Buddha image)” Project
Congratulations on receiving the “2022 Furusato-zukuri Grand Prize Group Award” from the Ministry of Internal Affairs and Communications. You mentioned that your school is using 3D technology to protect cultural properties.
In Wakayama Prefecture, “Sacred Sites and Pilgrimage Routes in the Kii Mountain Range” was registered as a World Heritage Site in 2004, and along with the historic Koyasan and Kumano Sanzan, there are many temples, shrines, and cultural heritage sites including many small temples and shrines in the villages. That is why they are very popular as tourist destinations, but recently theft of cultural assets has become a major problem. The depopulation of the region and the aging of the local population make it difficult to manage the cultural assets of these temples and shrines, and in some cases the theft itself goes unnoticed.
The curator of the prefectural museum wondered if something could be done about the frequent thefts, so he announced that he would create “substitute Buddhist statues” in cooperation with our school. First, a 3D scanner is used to photograph real Buddhist and Shinto statues to obtain precise data, which is then modeled with a 3D printer and colored in the same way as the real one. We thought that if the replica was dedicated to the site and the real one was kept in a museum, we could both protect cultural assets and maintain the environment of faith.
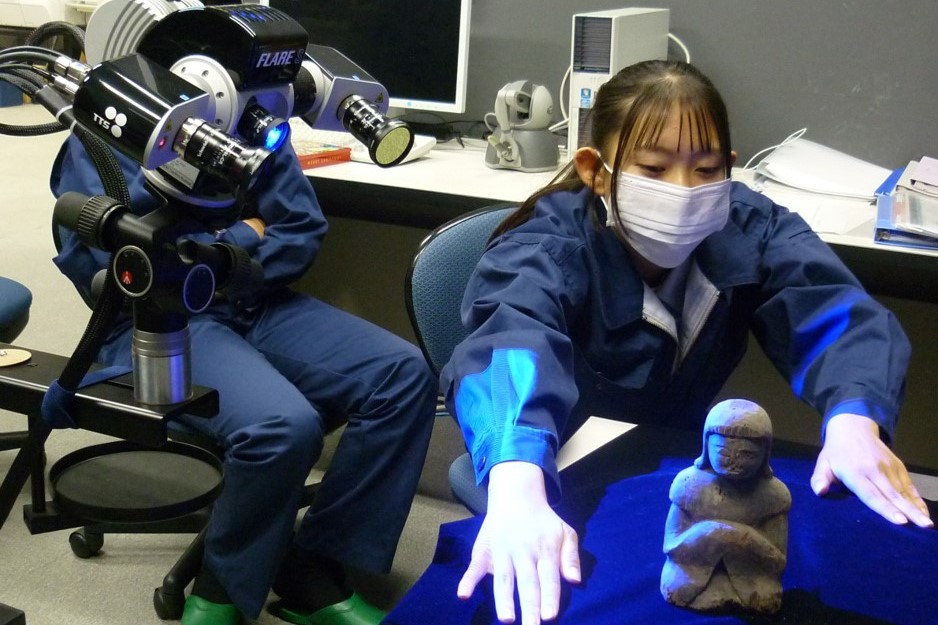
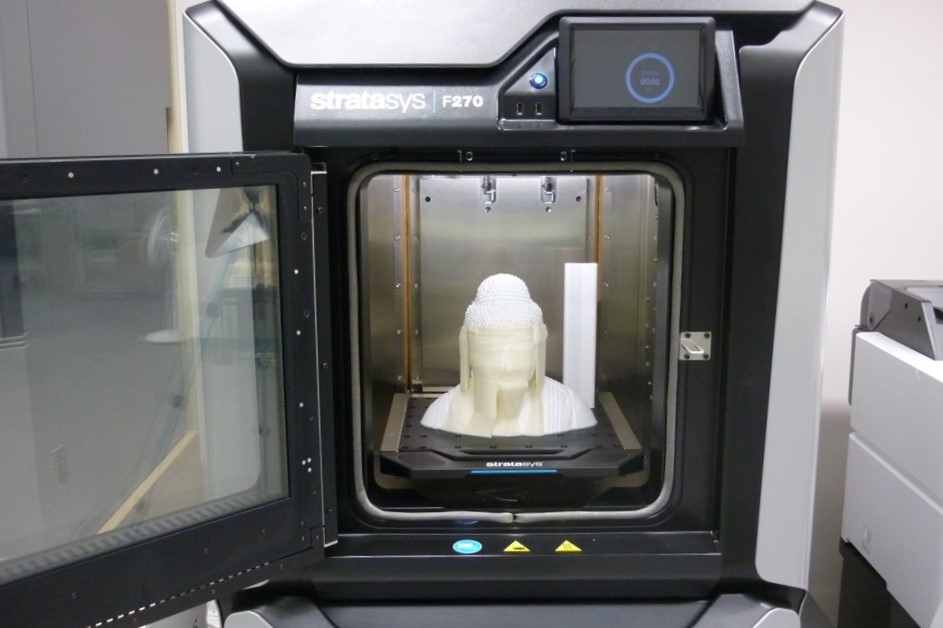
Of course, there are those who think, “If you don’t worship the real statue, there is no point. The curator will discuss this with the local people, and if they agree, we will be asked to do the work. We do all the modeling, with the help of art students from the Faculty of Education at Wakayama University for coloring, and recently we have been getting help from members of the art club at a nearby high school.
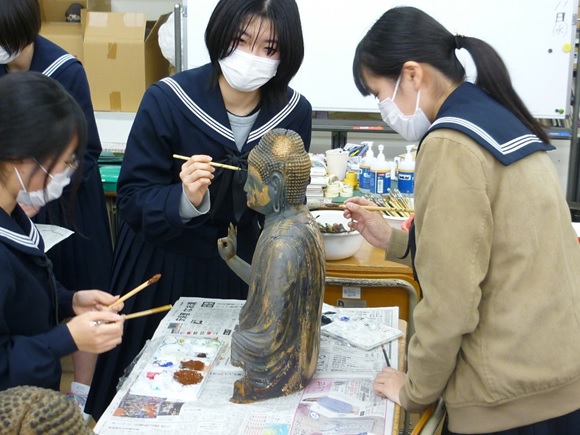
We usually do about two sculptures a year, and in some cases, the main Buddha and the side Buddha are paired together, so in total, since 2012, when we started this activity, we have received commissions from 21 locations in 9 cities and towns to create 40 sculptures. These led to this year’s award, which promotes “activities to make our hometown better.
Are the students involved in the measurement and modeling work?
Yes, the research project is an elective class for third-year students, so new students choose the 3D modeling group and join the class every April. We teach them the basic usage of FLARE and how to operate the modeling software before the Golden Week holidays in May, and after the holidays, we start the modeling work by scanning the real object.
Since we are not allowed to touch cultural properties directly, we ask curators to help us when scanning. If it is a small statue, we ask them to bring it to the school and measure it with “FLARE”. We ask curetors to “turn it a little sideways” or “show us the back,” while we measure the necessary parts. It is the students who determine the angle of the shot and give instructions.
Modeling and correction are also done by the students. If they are able to borrow the actual object, they look at it, otherwise they look at the photos they took with their smartphones and make corrections down to the smallest details.
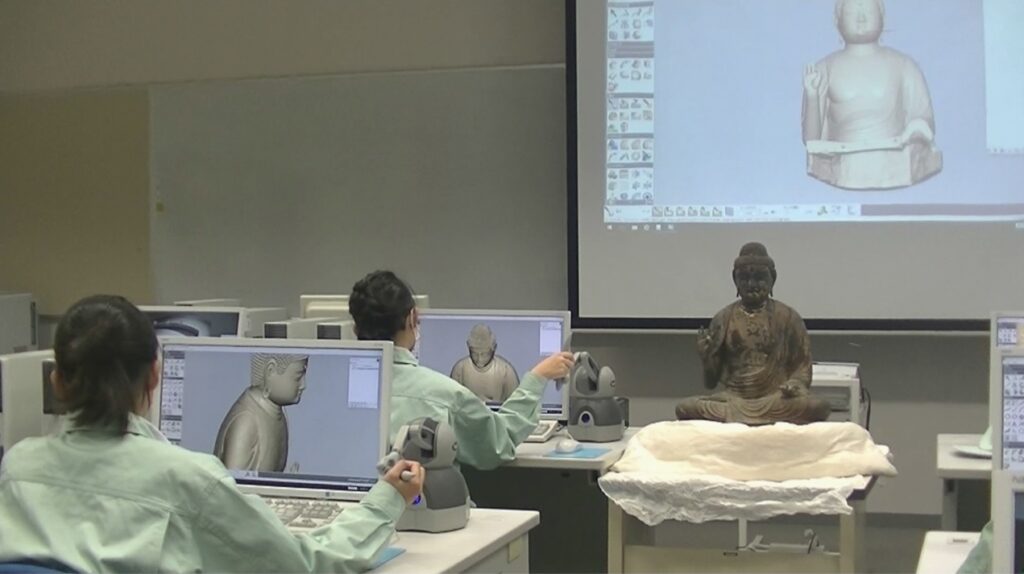
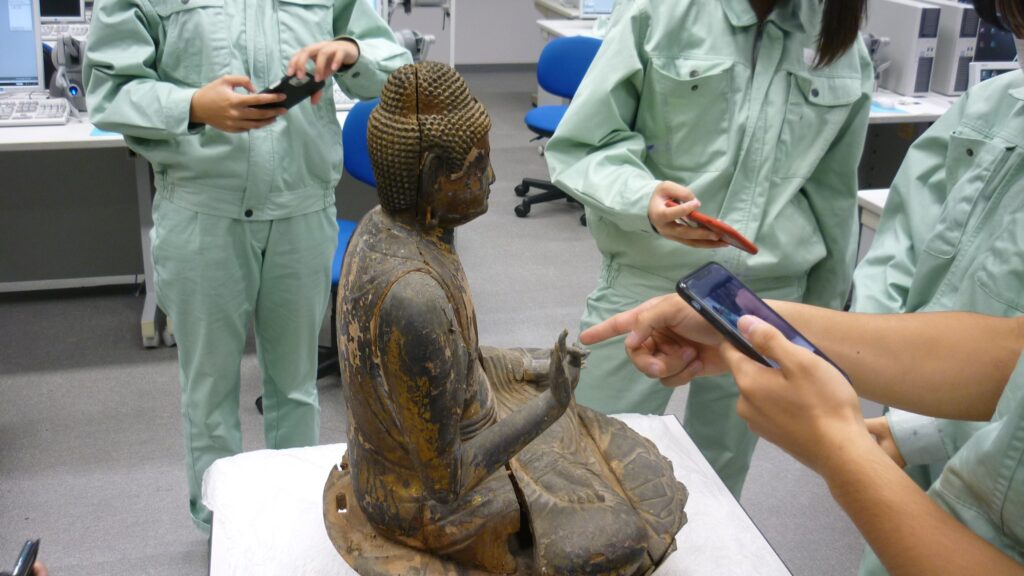
For example, holes in the earlobes and darkened areas on the sides are difficult to keep in the data, so they must be observed in detail and put into the data. I think their phone albums are full of photos of Buddhist statues (laughs).
Do you take on the challenge of creating large statues as well?
Yes, when we scanned a 180 cm tall the eleven-faced Kannon Statue, we took the equipment and students in my van to the museum. In this case, the statue could not be turned, so we had to put our scanner and computer on the dolly and take pictures in a circle around the statue. We all practiced together to see how much measuring range and angle we could move it to get a good shot.
The goal was “how accurately to convert the state of the object into data.
It is rare for a school to use a non-contact camera-type 3D scanner. What made you decide to introduce it?
When the Industrial Design Department was newly established in 2007, we wanted to take this opportunity to install a new equipment that would be the centerpiece of the latest technology. In 2009, we installed a 3D printer and a non-contact 3D scanner because we could expect to receive a budget from the prefecture. After that, we’ve been using it on a lease, so updating new equipment may be less hurdle than purchasing.
Considering the performance, we updated the equipment in 2016 and 2021. What we introduced in 2021 is “FLARE Standard”. The resolution of the previous model was 5M, but we chose 12M for the new model. The mainstream of the industry is moving to 12M, and I thought that the specs of the processing PC would not be a problem. Students use 200mm and 500mm lenses in class. We also have a dozen of 3D modeling software for data correction, so I am really grateful to be able to teach in such a state-of-the-art environment.
How did you feel when you switched to FLARE?
I thought, “It takes very clear and fast pictures. Also, compared to the previous model, there are no mechanical driving parts, and it runs very quietly. The scanning time is not much different from 5M, even though the resolution is doubled.
Unlike scanning in production, our goal is to reproduce every detail of the cultural artifact. If the object is a decaying statue, and it has been damaged over hundreds of years, we need to be able to reproduce “a statue that has been damaged over hundreds of years”.
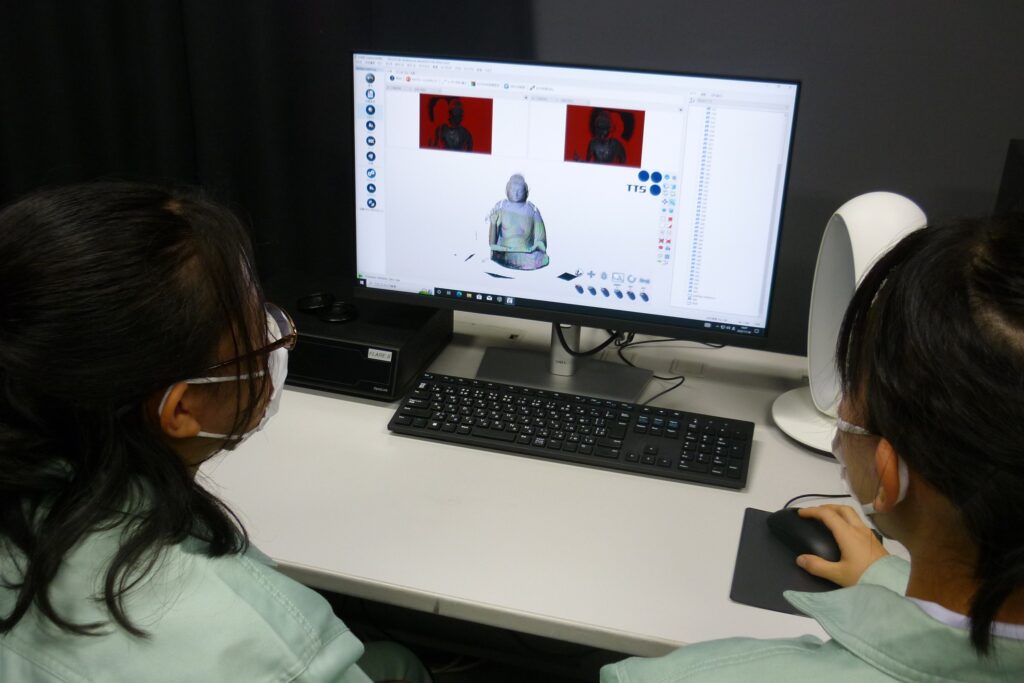
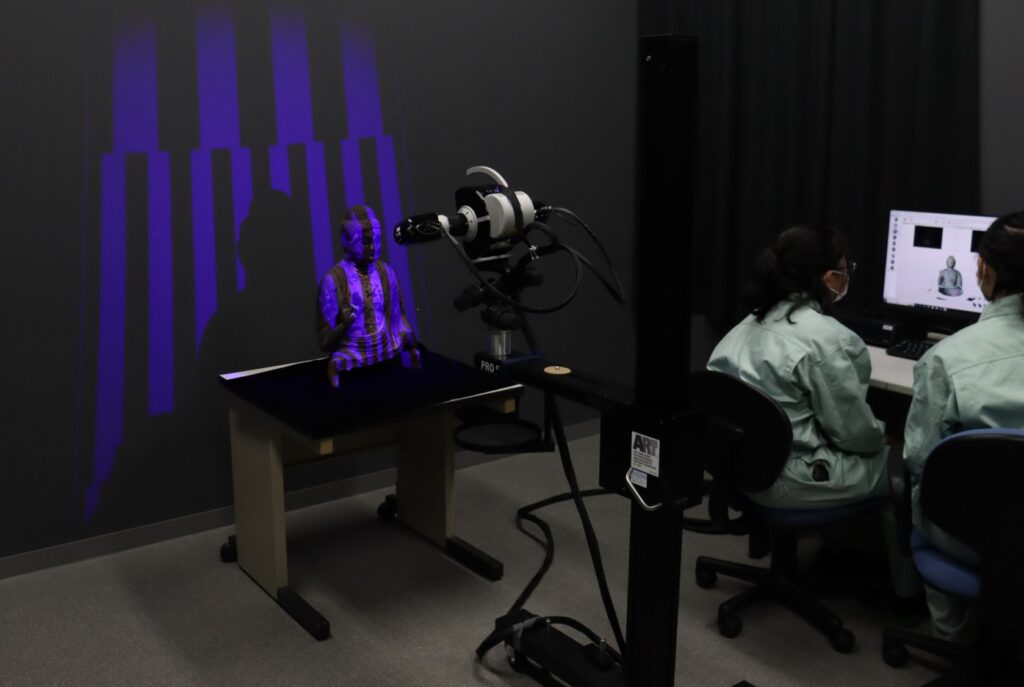
Whether it is possible to obtain clean data to reproduce them, which is with the bumpy texture of the Buddha’s spiral hair, the grain of the wood where the colors have faded, the roughness of the surface, and the subtle curvature of the surface, including small spikes and chips. That is why I was surprised at the accuracy and beauty of the data when I scanned with the 12M “FLARE” for the first time.
It is also convenient to be able to accurately measure an object without a reference point (a special markers used to align measurement data). Cultural assets are difficult to touch, so it is nice to be able to obtain data simply by photographing them without having to prepare a special jig and reference point.
FLARE” is also useful as an educational tool.
It was refreshing to hear how high school students are using the 3D scanner.
In the beginning of the class, they scan their own faces and export them to control software. Everyone burst into laughter when the data was read into the 3D modeling software and displayed on the screen. From there, they learn how to manipulate the data by making the eyes bigger, the nose higher, and so on.
Other elective classes include “graphic design” and “LINE stamp production,” so the 3D modeling group’s work on the “substitute Buddha statue” is considered rather sober. However, everyone seems to be impressed when the scanned statues are turned into realistic and beautiful data, and when they are sculpted and colored to look just like the real thing.
Moreover, when the statues are dedicated to temples and shrines, the local people gather to perform a ceremony to put their souls into the statues and purify them. The students who participate in the project realize that “many people are pleased with our work,” and I think this gives them a great sense of satisfaction and accomplishment.
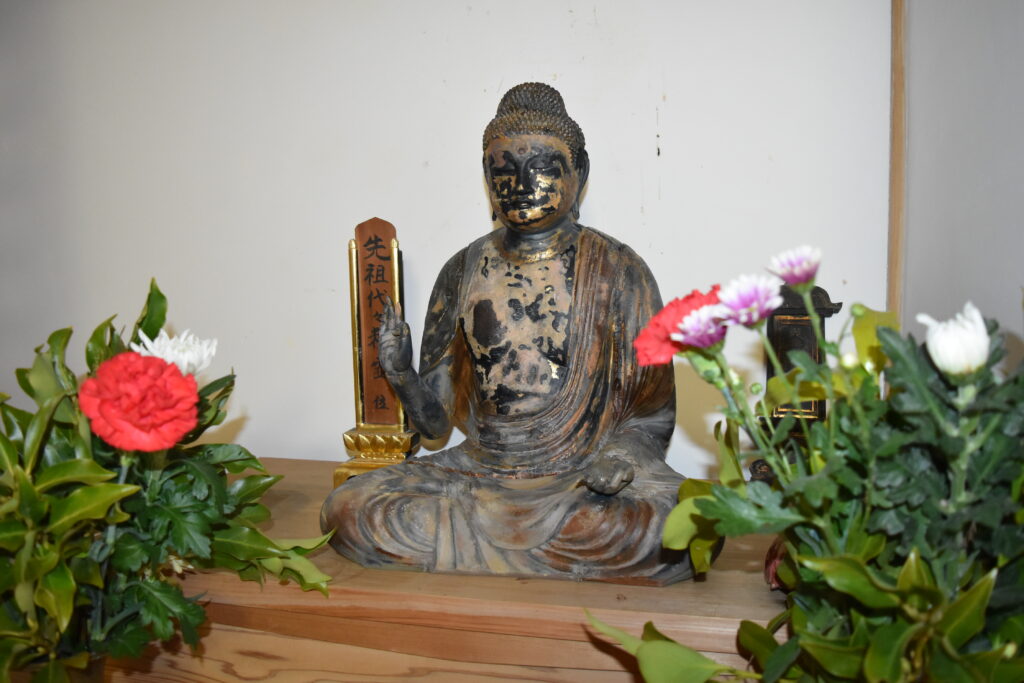
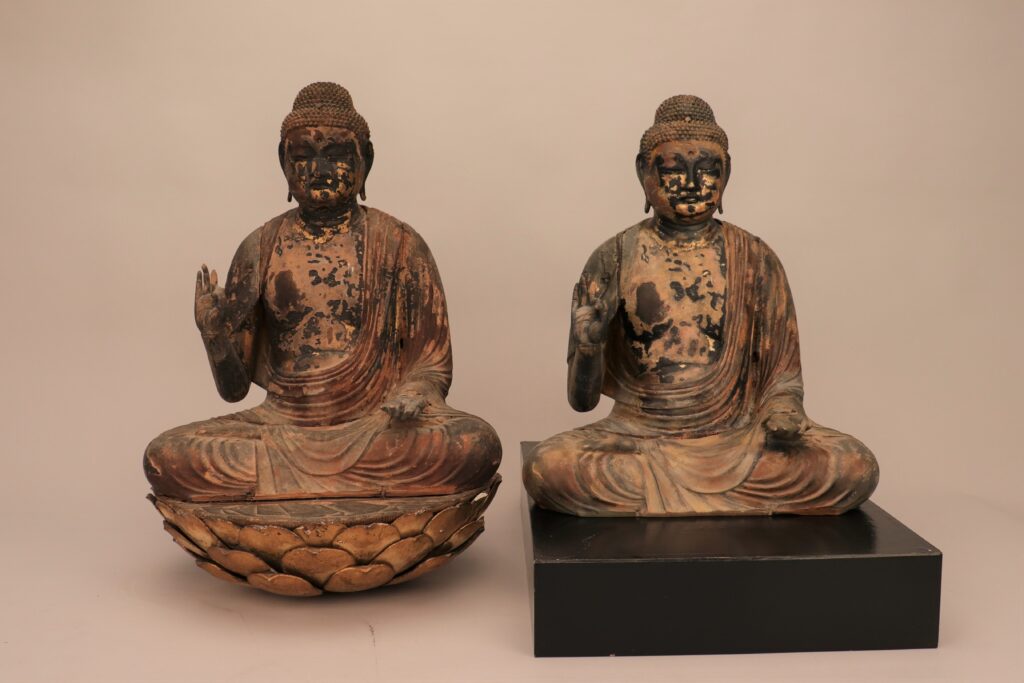
The elderly people are especially pleased to see that high school students, who are like their grandchildren, are treating their local cultural assets with such sincerity. Although the creation of the “Substitute Buddha ” was the initial impetus for the project, once we started it, we felt that it would also have an educational effect as an activity to connect generations and the community.
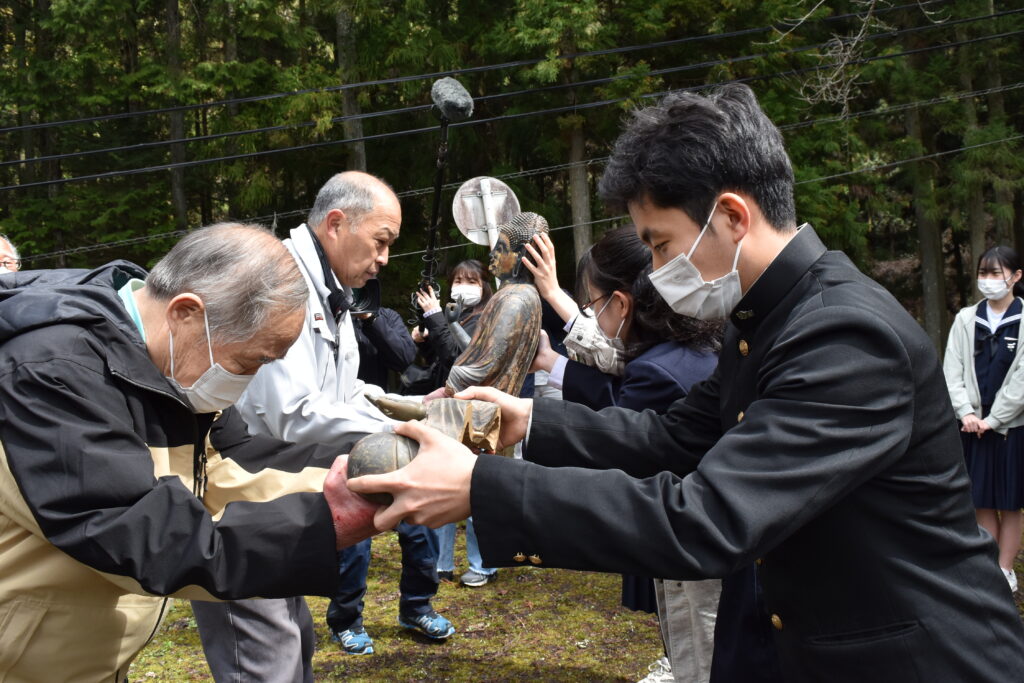
Local companies that learned about our activities asked us about reverse engineering, and some of the companies that came to observe our activities introduced 3D scanners, I think it is an interesting activity that is useful not only for the students but also for the local industry.
Comments from 3rd year students of the Industrial Design Department
Mr. Y / Ms. T: It was only after I entered the school that I used a 3D scanner. When I saw the scanned data for the first time, I was surprised because it was reproduced quite realistically. I think it would be interesting to measure plants and fish from now on.
Mr. U/Y: It is difficult to learn the operation of taking detailed pictures, but I am happy when I get good data. I also feel a sense of accomplishment when the actual product I made is completed. I think it will be fun to try taking pictures of Western sculptures and food products in the future.
Mr. Kodama: The other day, I had the opportunity to scan an important cultural property for the first time. I would like to try national treasures next time.
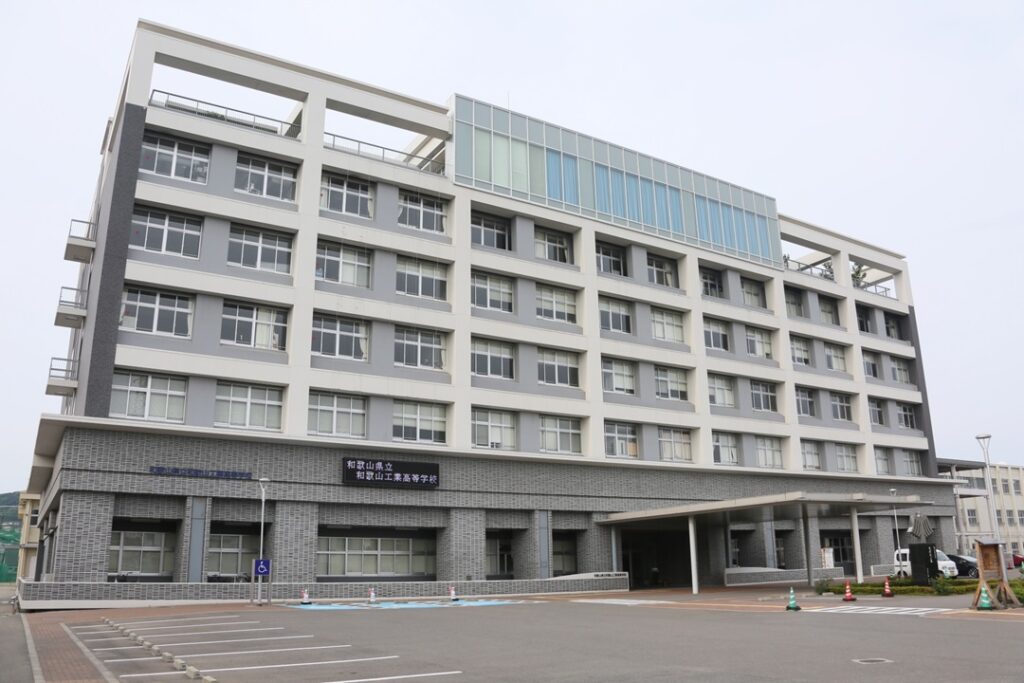
Wakayama Technical High School
Founded in 1914 as a prefectural technical school, the school merged with Nishihama Technical School in 1948, and changed its name to the current one in 1953, and is known as one of the largest public technical high schools in Japan. Currently, the school has seven full-time departments (architecture, machinery, electricity, civil engineering, creative technology, chemical technology, and industrial design) and two part-time departments (architecture, machinery, and electricity), with nine classes in three grades in the full-time program. In 2009, the Industrial Design Department began classes using 3D technology and community contribution activities, and in February 2023 received the “2022 Furusato-zukuri Grand Prize Group Award (by Minister of Internal Affairs and Communications)” from the Ministry of Internal Affairs and Communications.
Product used in this case study FLARE