COMET(This model is no longer in production and sales.)
SOSHIN CO., LTD.
Non-contact 3D measurement of molded objects, showing clear differences in the degree of error with color gradation
For industrial products that we come in contact with in our daily life, plastic parts are indispensable. Molds used for the manufacturing of plastic parts are just as important in the industrial arena. Among others, Soshin Co., Ltd. has been engaged in various fields that require molds, including cameras, AV equipment, medical devices, home appliances, and industrial machines, after gaining a reputation for high-quality mold manufacturing for ultraprecise plastic parts.
The company has been highly acclaimed for its capabilities of not only simply manufacturing and delivering molds but also providing a series of services from forming a mold on site using its molding machine and measuring it to giving product warranties. The main feature of the company is the ability to perform precise measurement at each step from mold production to a molded object, reducing the turnaround time compared to competitors.
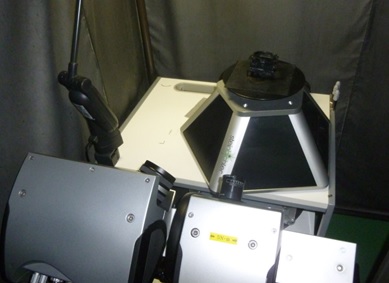
In order to streamline the mold measurement to meet increasing needs for accuracy in industry, the company has turned to the visualization function of COMET 5, a non-contact 3D measuring machine from Tokyo Boeki Techno-System. The system that can capture the surface shape of an object to be measured and output it as a cloud of high-density data points with 3D coordinate values is utilized by Soshin’s know-how and technological capabilities, enabling accurate measurement and judgement based on customers’ needs.
Soshin is often asked by its clients and others in the same trade for advice regarding how to measure and/or process a mold. This may be because they have a long-standing credibility accumulated by the knowledge and skills of the employees who are familiar with mold manufacturing, as well as scrupulous follow-up services.
We interviewed Soshin’s employees about how they utilize the non-contact 3D measuring machine, COMET5, at their company, which supports Japan’s industrial products.
Mr. Masao Matsuura
Belonging to the Sales Division 2nd Sect. as well as being in charge of the Material Procurement Division as its chief, he has been proactively involved in the new business development to extend the reach of the company while experiencing the actual mold manufacturing as a technician. Currently, he is engaged in the management over the entire business.
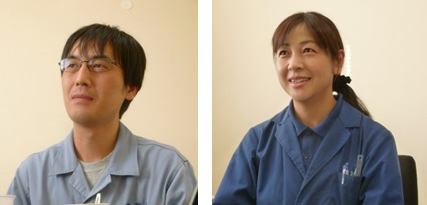
Mr. Takayuki Masuda (left) / Ms. Naoko Shiotsu (right)
They perform measurement using COMET5 in the development and production of molds. They test measurement methods according to the structure and shape of an object to be measured, meeting the needs of their customers.
Improved business results by meeting customers’ needs and responding to problems.
Interviewer (I): About mold manufacturing, what do you think is the biggest difference between Soshin and other companies?
Mr. Masao Matsushita (MM): In addition to delivering molds, we also offer a service of accepting any molded object, which was made with our mold and found to have any defect, and solve the problem. If our customer cannot make a molded object with specified scales, we will go back to its mold, examine it, repair it, and deliver it again. We can guarantee the precision with measurement accuracy.
Speaking of costs (expenses and time), people often focus on mold manufacturing, which directly yields a profit but not on the measurement step, which doesn’t directly yield a profit. In fact, however, tests and corrections up to the product delivery cost an enormous amount of money to check whether a shape that matches the specification has been achieved.
It may be true that our customers could check measurement by themselves; however, we can choose the most suitable tool, rapidly and accurately perform measurement to point out a problem, and solve it with our high technological capabilities in mold processing. We take pride in offering these services as a comprehensive package. Our customers can solve their problems much quicker by delegating the task to us than doing it by themselves. That’s how we have been able to establish long-standing credibility over many years. Now we are receiving large-scale projects as a mold manufacturer capable of producing highly-precise molded objects.
I: What kind of problems did you have so far in measurement of molded objects?
Mr. Takayuki Masuda (TM): We originally had a contact 3D measuring machine. The machine only can tell the coordinate position when its terminal is put against an object to be measured. When we measure, we have to set measurement points based on our assumption, like “we may have to check near here.” So, if the cause of the problem is located somewhere unexpected, we may not find it, thus raising the possibility of not successfully solving the problem.
In the past, we only received a 2D paper drawing on site, so we had to guess the points to be measured and perform measurement based on them. For example, if the problem is a molded object not working smoothly, we have to guess a spot possibly containing the cause and measure the spot with the contact measuring machine. Although we can get 3D information these days, the step to guess a spot and measure it hasn’t changed much.
For delicate parts, contact measurement may move a molded object by the pressure from touching the machine to the object. Since we perform micron-level measurement, the problem was that even a little contact could affect the measurement result.
I: So, did you decide to bring in COMET5 because it is non-contact?
MM: We decided to bring in COMET5 because of feedback from a customer. When he came to join our factory tour, he told me that he has a problem measuring some molded object with a complicated shape. While if a molded object to be measured is simple in shape, you could perform measurement at a few points only, if a molded object has a complicated shape, you have to measure at many points. For that customer, what he showed me was as small as my palm, but he said that he had to perform measurement at thousands of points.
His story reminded me of COMET5 because I knew that there was a “non-contact measuring machine that could measure the whole object” from trade fairs and exhibitions. In fact, I heard from one of our customers that some major precision equipment manufacturer started using one, so we started checking it out, thinking although it is expensive it may be worth trying.
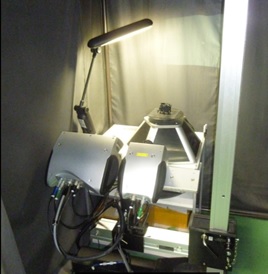
In the past, we examined a similar measuring machine, but we concluded that we couldn’t expect cost effectiveness due to its low accuracy. In addition, even if there is a very convenient measuring machine, if our client doesn’t trust it, it is useless for us to offer measurement data using it. However, COMET5 was chosen by the major manufacturer with a reputation for accuracy and precision, and as a result of interviewing them, we concluded that we could expect sufficient cost efficiency. Therefore, we started using COMET5 in April, 2010.
Color gradation makes it obvious, with easy information sharing
I: So, even if an object to be measured is small, the complicated shape makes measurement difficult.
Ms. Naoko Shiotsu (NS): We handle molds with various sizes and shapes. Complicated ones are rolls, like a tube framework for telescope. For example, there is a type of compact digital camera which lens sticks out when it is powered on. The smooth motion is achieved by accurate engaging of fine parts. Manufacturers ask for very high level of accuracy with these parts and we need to perform very complicated measurement.
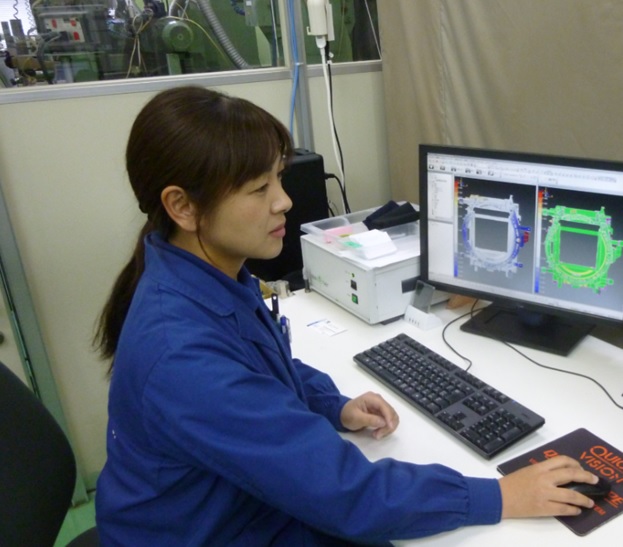
TM: In the case of initial complete measurement of a molded object with a complicated shape, the conventional method required several days even with several people working on it. Then, since we started dividing measurement points depending on the features of the measuring machine used and accepted COMET5 measurement data only for some parts, we could successfully reduce the number of points to be measured. I believe that we could accomplish that all thanks to our customers trusting COMET5 measurement data.
I: In what situation do you find COMET5 most useful?
NS: I would say that it is the initial measurement of a molded object. When you make a mold for the first time, you have no idea how the molded object may be deformed. So, we often use COMET5 when we say “let’s take a look at the finished product.” I fix a molded object in a measurement area, shed light on it, take photos from various angles, and measure it. When I measure more than one molded object, for contact measurement I have to make sure the arrangement should be the same, while for non-contact measurement I only need to fix the molded object.
By combining all the photos taken using the software, you can visualize a whole body from a cloud of points data, therefore being able to capture the whole picture and to compare 3D models (3D information) and a cloud of score data by color difference. If you set the color setting to tell that darker parts have larger errors comparing to 3D model, you could tell something is wrong at a darker part. This way, we can check general tolerance with large acceptance range visually rather than with numerical values.
In the past, we had to check the condition of a molded object by looking at a table for measurement results with a series of numbers and a graph made from numerical values. Now, we can see the degree of deformity, abnormal shape, and/or possible processing mistakes at a glance thanks to color gradation display. So, we can share what is to be corrected among our clients, designers, and technicians.
Even with a surface, it can never be a completely uniform planar surface; it should have some distortion and/or slope. Such distortion and/or slope was hard to see with a contact measurement, in which only a few points are measured. But now, thanks to COMET5, we can accurately assess each surface as a whole, which enables us to perform appropriate modification. We can get a rough idea of an object to be measured at the initial stage, leading to shortening of the following steps.
Some precision equipment manufacturer representatives only want to look at initial COMET5 measurement data of a molded object, leaving the measurement itself to us. You can tell the molding condition of a molded object simply by looking at the data, so I think they use what they see in the data for the future manufacturing schedule and project planning as well.
I: For fine adjustment after measurement, you use your high level of technological capabilities.
I believe that our current reputation came from not only introducing a high-performance measuring machine but also having technologies that can utilize the measurement results.
It was a long time ago, when we were only supplying molds, that we received a complaint from one of our customers about water leakage. The problem arose from the molding stage, in which we were not involved. However, we went straight to the president to tell him that we wanted to address this problem so that we won’t have the same problem again. As a result, we set up our own molding machine so that we could perform in-house verification. Similarly, as for measurement, we received a request from our customers that “if you measure molds, I want you to measure this,” which triggered our “Let’s try it and see” challenge of measuring. As a technician, I never want to say “I cannot do that.” The introduction of COMET5 is part of our challenge.
Our company has been developing the technologies and making achievements by addressing the requests from our customers. I think we should not only become able to make full use of the latest tools, but also continue to improve our technology to steadily apply measurement results to molds.
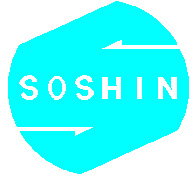
About Soshin Co., Ltd.
Founded in 1988, Soshin has been engaged in the development, manufacture, and sales of ultraprecise plastic molds and is currently operating in various fields, including camera parts, medical devices, houseware, food hygiene, home appliances, and industrial machines. As molded objects are becoming smaller and more precise, the company has been earning a good reputation with its processing technology to meet customers’ needs and long-standing on-site knowledge in the industry. Aiming for further quality improvement, industry-leading cutting-edge facilities are in operation at the new factory (started in 2000) and at Wakayama Soshin.
Product used in this case study
COMET
※This model is no longer in production and sales. We still offer support for our COMET users.
Please contact our sales staff for details. Also, please see the page of new camera-type 3D scanner FLARE series.