- Mission
-
In truck manufacturing, accuracy of visual inspection done by inspectors before shipping is quite important to meet each detailed option request such as body colors, body parts, and other customization requests. There are various inspection items to see if the truck is exactly finished as ordered and it can be too complicated to complete the inspection without omission. Therefore, visual inspection accuracy is important to improve product quality.
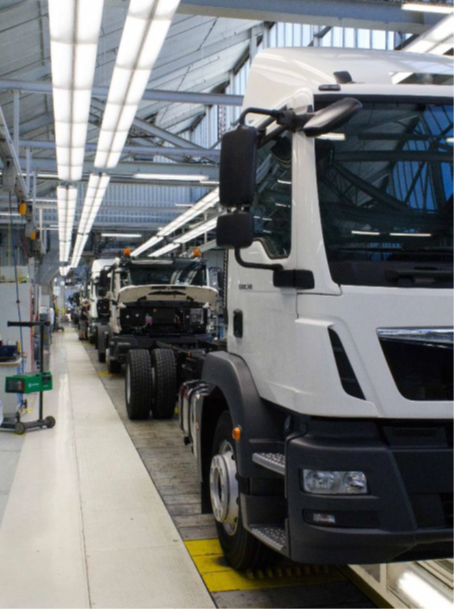
Proposal Contents
Solution:ATS Inspect
Digitally register appearance defects
At major gate points along the production line, ATS Inspect is used to perform a visual inspection of the vehicle. If operators find any defect such as a scratch, dent, or wrong part, they can register it easily with the image. With just a couple of clicks or screen touches, accurate position, type, severity can be recorded. This action can be done via either a PC at fixed work station or tablet, which means the operator can register the inspection result even while moving.
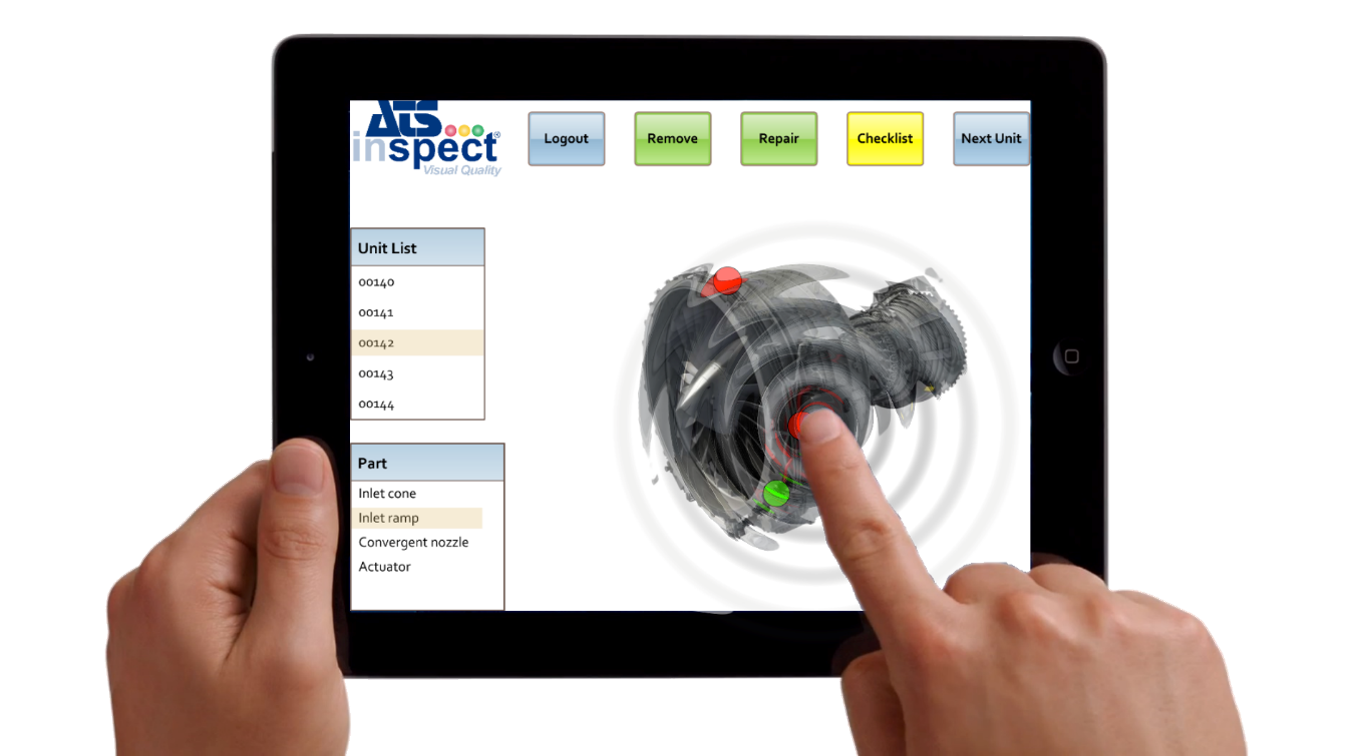
Quality control for mass customization
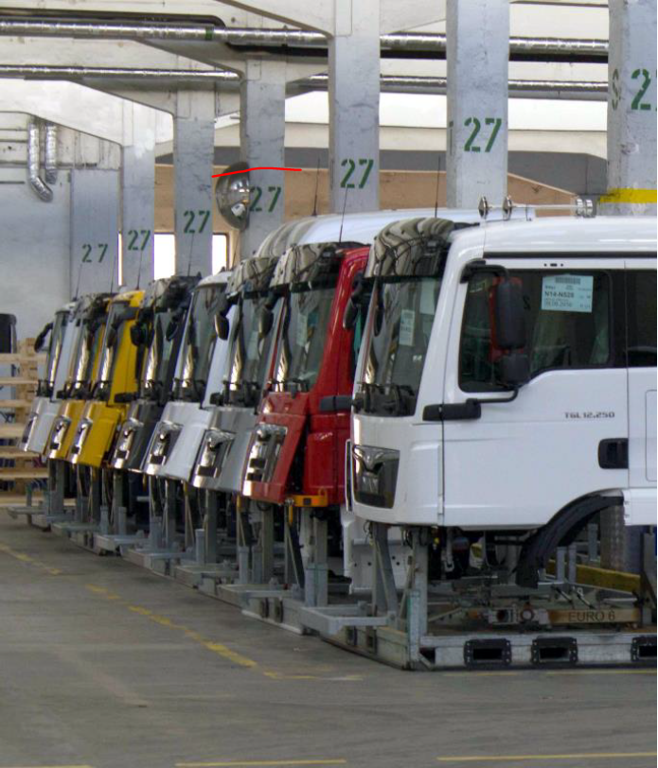
In a truck manufacturing process, each truck is finished with slight difference from others to meet each unique order from various customers.
For this kind of a large volume of customized vehicle inspection, ATS Inspect is a perfect solution.
When a truck on a production line reaches the inspection point, the serial number on a barcode of the truck is scanned. The identification information is sent to ATS Inspect, inspectors learn the inspection items which match the ordered specification for the truck, and they can proceed the inspection.
There is a choice of view in 2D image or 3D model corresponding to the vehicle type and configuration of the working station.
Inspectors can choose either type of view to register defects.
Digitalization of quality control checklist
ATS Inspect digitalizes a quality control checklist which inspectors use to check if all the customization is correctly done. It displays those dedicated checklist items for each model and specification dynamically.
Because of this feature, none of those trucks manufactured in this factory is shipped with wrong parts attached, even though each of them is finished in different specification.
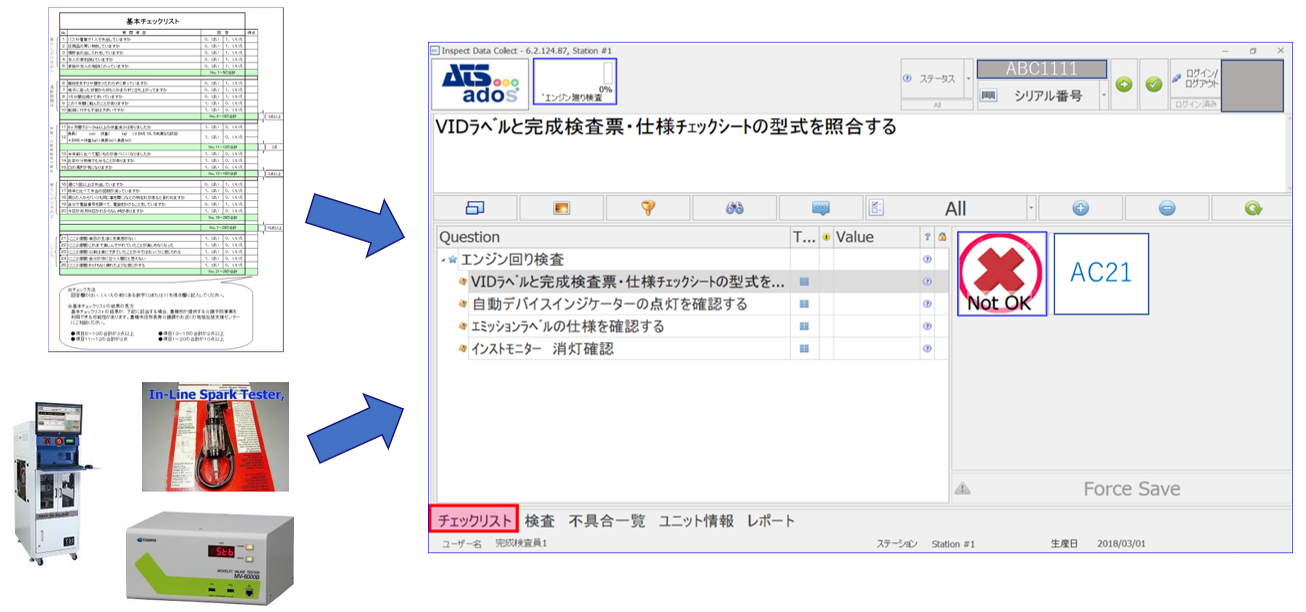
End-to-end traceability
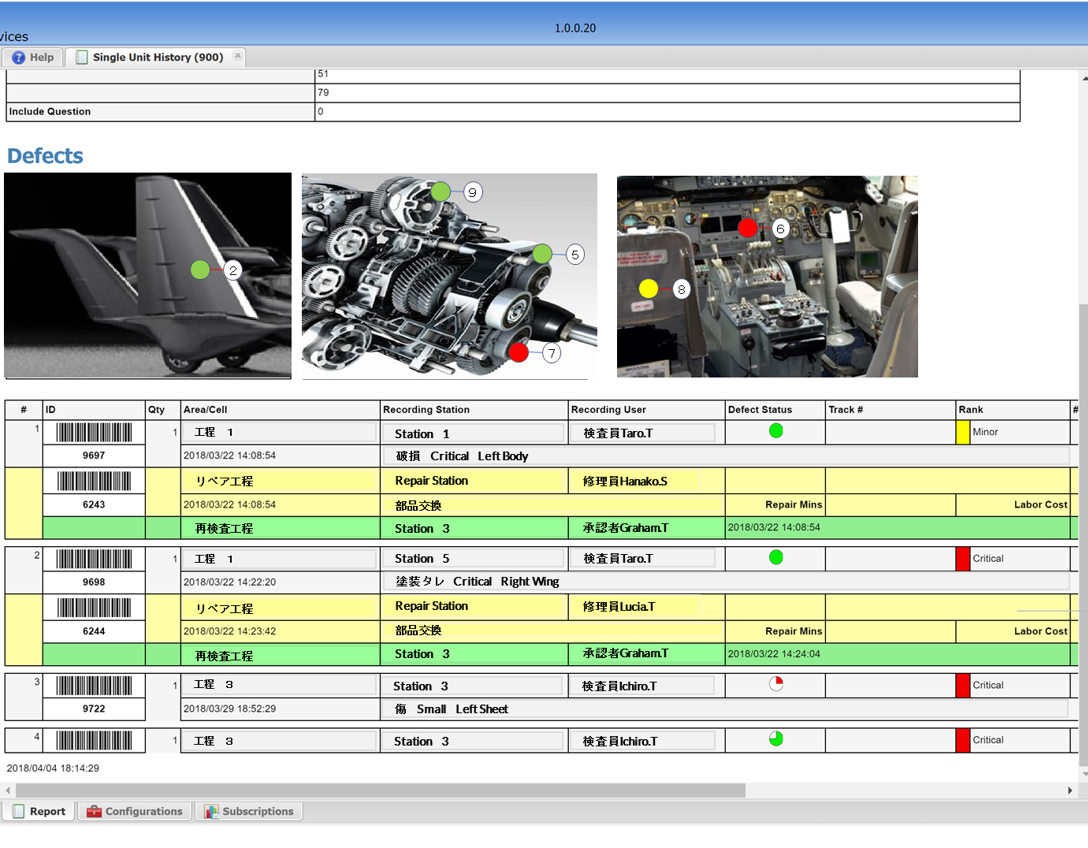
Since ATS Inspect also has end-to-end traceability, any unit produced in the factory can be traced. Every inspection station that a unit goes through records further information of the product quality, and the overall picture consisting of the current status and details of all the process that the unit has passed will be created.
Where is the unit sent? When was it here?
ATS Inspect records all such information of each unit. It means it can determine a cause of problem by tracing back every record when a problem occurs as well as figure out all other units which have passed the same trouble spot.
Product quality analysis
Report generation with no organizing work
・Automatically generates any kinds of report!
・Utilizes fresh data!
・Prevents data tampering by digital traceability!
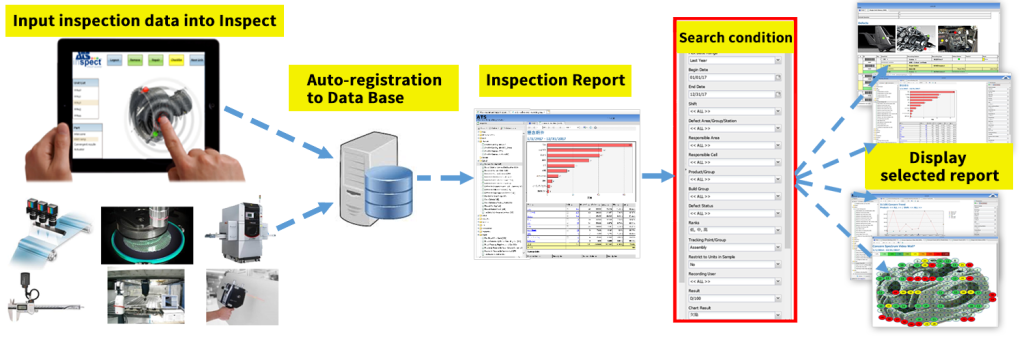
The key to automotive inspection solutions is the ability to analyze quality data. ATS Inspect is equipped with a powerful report generation function. As information input in ATS Inspect can be used for analysis right away, reports will be always fresh.
From all the inspection history of a single unit to trend overview of total defect number recorded in the previous month, there are many patterns of report templates for overall review of product quality.
Both workers and managers can use this function, so it is possible to share all the information to figure out the best solution quickly.
Those features of ATS Inspect would contribute to minimize man-hours for data collection so that workers can spend more time for other things to work on and determination of causes of defects and scrap.
As a result, not only significant reduction of product defect rate can be expected but also wide reduction of Cost of Quality will be possible by real-time analysis.
What ATS Inspect does is not solely data collection. ATS Inspect collects data and support to find out a way to improve process by using the data, which leads to cost reduction.
For more information on this solution, please contact us via CONTACT button on the screen, TTS Online, or any contact information at the bottom of this page.
System Configuration
System Image
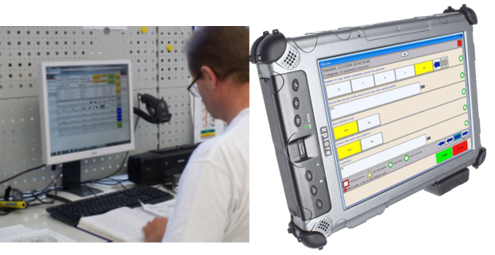
Sample: Defect registration
L: Fixed station R: Tablet
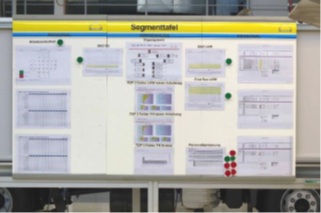
A monitor to display reports is placed at the production site. Workers can deal with a problem immediately when it occurs.