TTS Smart Manufacturing
Measurement × Simulation
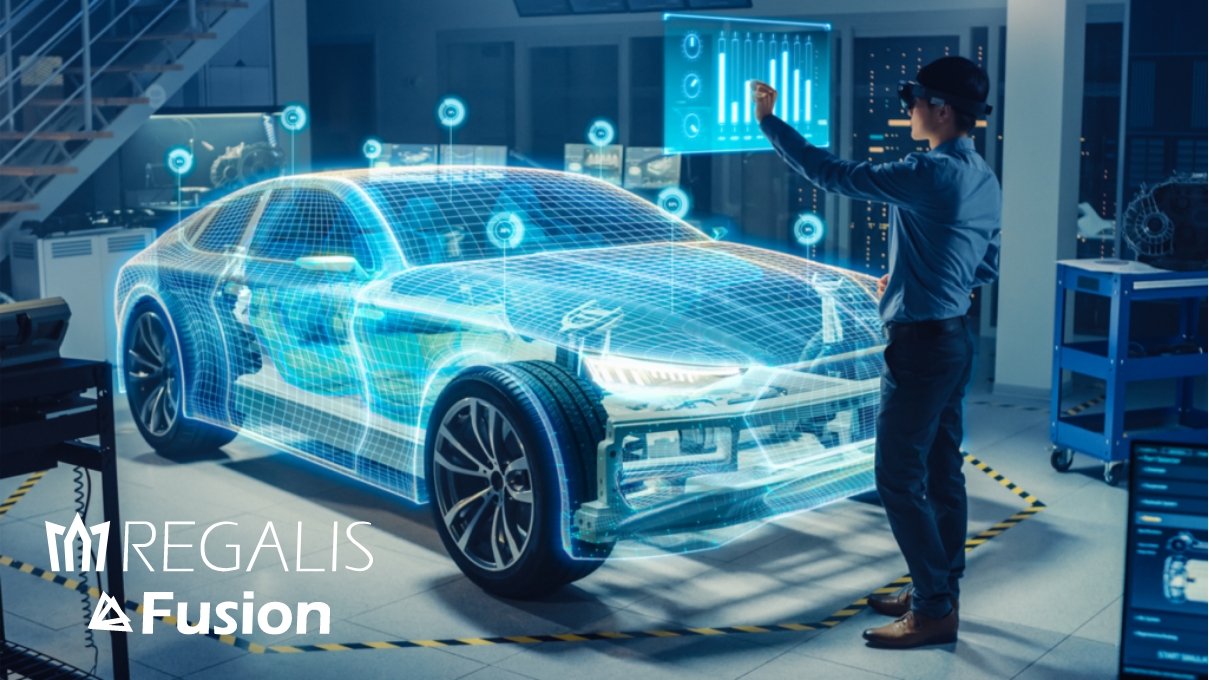
Realize Smart Manufacturing by combining the physical (actual) and virtual.
Through Smart Manufacturing, REGALIS Fusion aims to realize solutions for prototyping and production engineering departments in the manufacturing industry.
In order to tackle and realize Smart Manufacturing, it is necessary to build a digital twin and digital thread.
With REGALIS Fusion, “measurement data”(the digital twin of the shop-floor, actual product, and reality) and “simulation”(the principle) are combined in a digital thread to change the manufacturing process.
REGALIS Fusion contributes to productivity improvement, which is a major challenge in the manufacturing industry.
Digital Twin Digital Thread
- Allows construction of a digital twin for each process that reflects shape changes due to physical phenomena.
- Provides a digital thread that connects design and simulation data with actual measurement data.
Process change in the manufacturing process
- Realizes accuracy improvement of simulation by reflecting actual accuracy from measurement data to simulation model generated from design values.
- Possible to replace the actual inspection jig used to inspect the shape of a part with a virtual inspection jig. Users can greatly reduce the delivery time and cost of manufacturing actual inspection jigs, as well as the maintenance work and storage space required to maintain them.
Module Configuration
Morphing (MP) | Gives the accuracy of the actual product to the design data (FE model) and makes the simulation more accurate |
---|---|
Virtual CF (VCF) | Evaluates shapes by virtual inspection jig |
Contributes to increased productivity
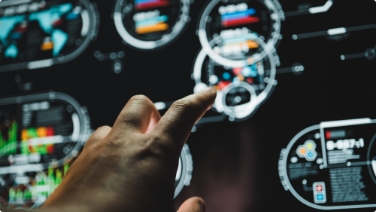
Reduces development lead time
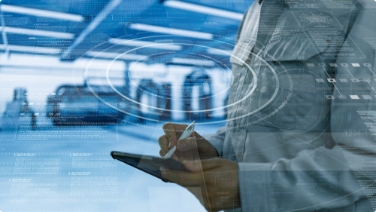
Reduces development costs
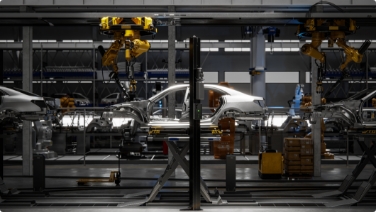
Improves manufacturing quality
Functional overview
Morphing module
Simulation from design geometry that differs from the actual product does not improve prediction accuracy.
Reflects actual measurement data in FE model.
Increased simulation accuracy
Measurement data allows the simulation model to reflect the accuracy of the actual product to improve prediction accuracy.
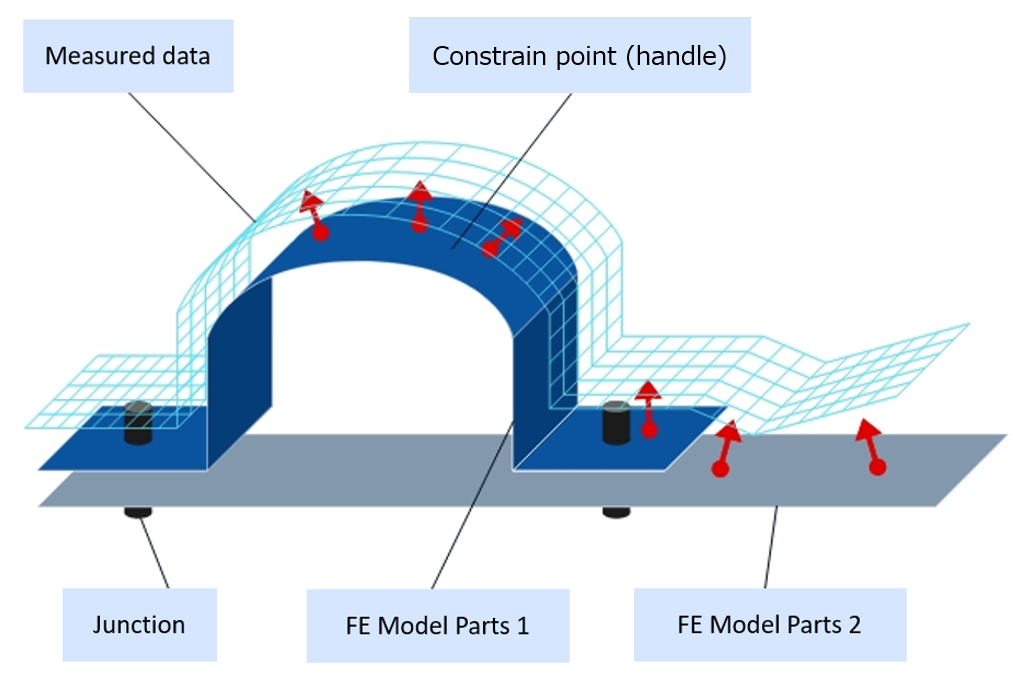
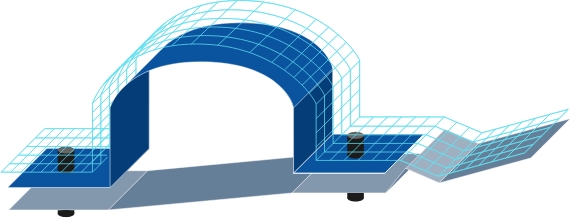
Morphing Process Flow
Error between design data and actual parts
Reflects measurement data in areas with large errors
Design data (FE model) with actual accuracy
Product Video
Virtual CF Module
- Delivery time/cost of special jig production
- Storage space for dedicated jigs
- Maintenance man-hours for dedicated jigs
- Variation by operator
- Convertible general-purpose jig
- Morphing
- Gravity Cancellation
- Simulation
- Reduction of production man-hours/costs
- Reduction of storage space
- Reduction of maintenance man-hours
- Highly accurate prediction of deformation by virtual test fixture
Replacement of specialized jigs with general-purpose jigs
The dedicated inspection jig is replaced with a general-purpose jig that can be converted to perform measurement with simple support.
The measurement data is reflected in the design data, and the deformation caused by the virtual fixture is predicted by applying weightless processing.
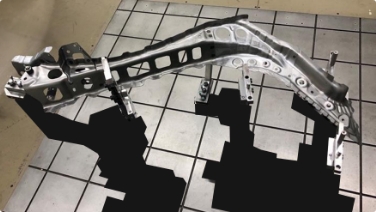
Dedicated testing equipment
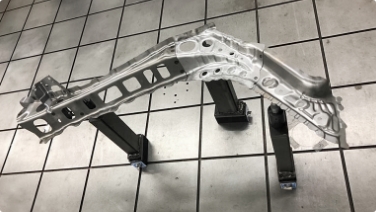
General-purpose jig
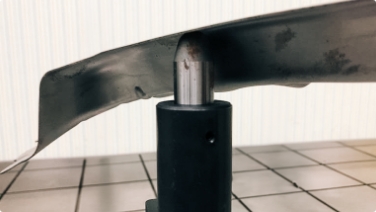
Simple support
Morphing Process Flow
Measurement of simple support with a general-purpose jig
Reflecting actual accuracy by morphing to FE model
Cancel Gravity
Predicts deformations by applying gravity and constraints in a new posture using a virtual test fixture.