・ポイントを押さえた自動化と自由度の高い設定でリバースモデリングが1/10の時間で完了
・CADソフトへのスムーズな連係で工数を大幅削減
愛知県名古屋市に本社を置くApex株式会社は2007年に創業、同年からオリジナル自動車後付けパーツブランド「Apexi」を立ち上げて製品の開発・製造・販売を進めてきました。米国でも販売サイトを開設して、国内だけでなく海外からの需要にも対応できる体制を作っています。
他社と比べて特徴的なのは全ての自動車メーカーに対応できること、そしてサーキットユースに代表される「マシンの性能向上」に特化したコンセプトです。自動車メーカー各社の部品・外装とのアライメント技術に優れ、品質の高さでファンを増やしてきました。
近年取り組んでいるのは3D技術を活用した新規事業です。2013年にアーム式レーザー非接触測定機、2015年にカメラ式測定機を導入、モデリングや3D CADのソフトウエアを連係させて高精度のリバースエンジニアリング事業を始めました。
現在携わる分野は、電気自動車の試作車や樹脂製品の開発、医療用器具のモデリングや開発用システム構築など多岐にわたります。これまでは加工や3D造形と接点がなかったクライアントにも豊富な開発経験とともに技術を提供し、リバースエンジニアリングの可能性を広げています。 東京貿易テクノシステムのリバースエンジニアリングソフトウエア「spScan」も、その事業拡大に大きく貢献しています。導入により何が変わったのか、今後の事業にどう活用していくのか、お話を伺いました。
- 課題
-
- 以前のソフトは大がかりで作業を始めるまでの設定に工数と時間が必要だった
- リバースエンジニアリングを受注しても納期までの時間が読みにくい
- 自由曲面が多い製品では目的の形状を得るためのプロセスが面倒だった
- 解決
-
- 「spScan」導入後、少ない手数で設定ができ十分な精度で出力できるように
- 工数が減り、リバースエンジニアリングの作業プロセスを予測しやすくなった
- ソフトによる自動化と技術者による手動のハイブリッドで、手早く作業が完了
新規事業部 山﨑 淳一さん
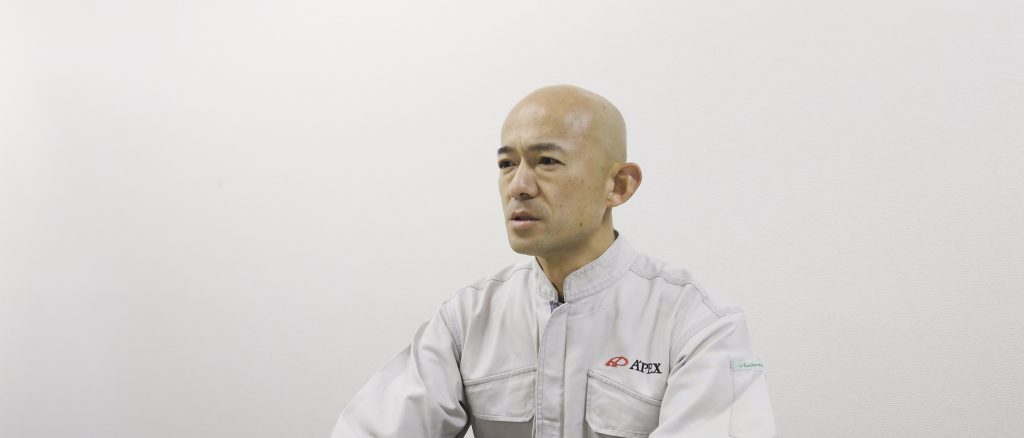
新規事業である3D技術サービスを担当。各種測定機器を使った計測や検査、設計、試作品の作成、システム構築など、リバースエンジニアリングに必要な一連の工程を行っている。
導入時からの長年にわたる「spScan」ユーザーでもある。
製造・販売に加え、量産前をサポートする新事業を展開
現在、「spScan」はどんなシーンで活用されているのでしょうか。
新規事業として展開している3D技術サービスで活用しています。当社では3Dスキャナーを使った計測から始まり、検査、リバースモデリング、モデルデータを使った流用設計や新規設計、試作品作成、試験などに必要なシステム構築を行っています。3D技術に関する全てを一貫して、自社で提供できるのが強みです。
モデリングで重要な役割を果たすのが専用ソフトウエアで、以前は他社製品を使っていましたが「spScan」導入後はこちらをメインで使うようになりました。
主力事業は自動車部品開発ですが、他の分野へも展開していると聞きました。
そうですね、もともとの事業はサーキットや車好きの方を主なターゲットにした改造部品の開発・製造・販売なのですが、私が担当する新規事業部は自動車以外の分野でも展開しています。
例えば、医療用器具を製造する企業から「量産に向けた試験を行いたい」という依頼があった際は、当社で部品の角度や径を何通りも試験できる機械を作って納めました。プラスチック製のパッケージを扱う企業からは、量産に向けた試作品の計測・検証を引き受けたケースもあります。
もちろん自動車関連のノウハウを生かした受託でも「spScan」が活躍しています。樹脂系部品の試作品についてCADデータと成果物のズレについて検証したり、車1台丸ごとのモデリングを行ったりした例もありました。このときは外装・内装・下回りや内部を含めて±0.1mm以内の精度で現車を計測・モデリングを行い、500時間ほどかけて納品しました。
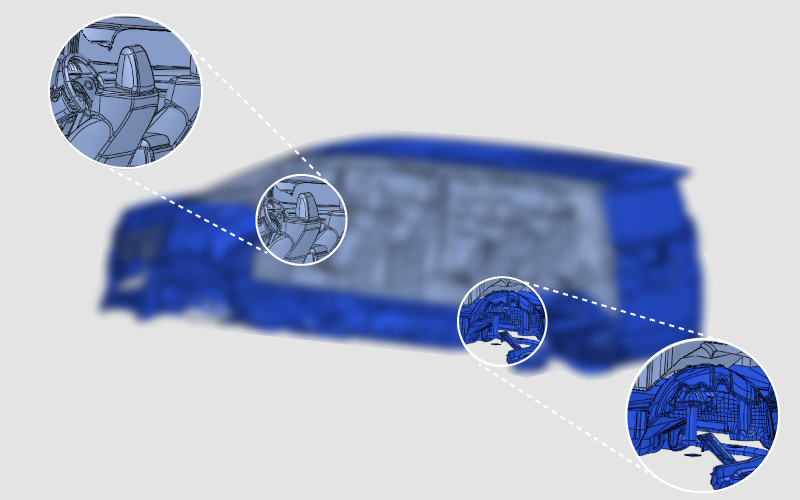
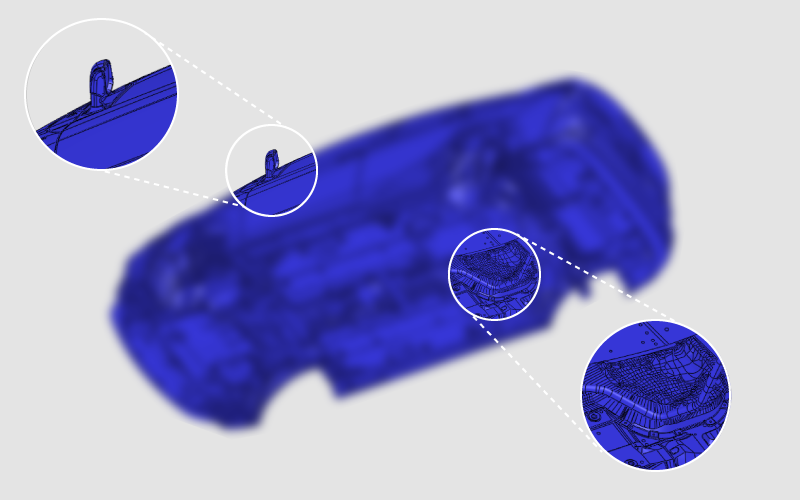
自動車1台丸ごとのリバースモデリング
※リバースモデリングの詳細についてはApex様にお問い合わせください。
部品開発では完成した製品をユーザーに届けますが、新規事業ではもっと工程の上流に関わる案件が多いのですね。
はい、プロダクトの企画や、開発に伴う試作品のためのモデリング、試験用の治具開発、システム構築などで実績を伸ばしています。当社がこれから広げていきたい領域です。
他社比較で断トツだった「spScan」
2015年に「spScan」を導入する前はどんな点が大変でしたか。
少し前に社内の3D環境を整えるためにハードやソフトを一括導入していました。「spScan」の競合製品にあたるソフトもこのときに使い始めたものです。
2013年にアーム式レーザー非接触測定機を導入し、このソフトを連係させてみたのですがあまりうまくいきません。もともとの用途がリバースではなく、自動車の外装モデリングをきれいに作るのが目的のソフトだったので「これでリバースエンジニアリングを進めるのは厳しいな」というのが正直な感想でした。
きれいな面データができて非常に高性能なのですが、使い勝手がとても大がかりで、何でもできるけれど全てを自分たちで作り込まなければいけない。1年ほど使っていてさすがにもっと手軽なツールに変えたいと思い、新たなソフトを探し始めました。
「spScan」以外にも他社製品を比較されたのでしょうか。
「spScan」を含めた3社に同データを渡してリバースしたサンプルデータを送ってもらい、確認して選定しました。サンプルは10個はなかったと思いますが、あえて商品としては使わないレベルの複雑な部品も混ぜてどのくらい追従するか見ています。
重視したのは面の構成、送るSTLファイルに対しての偏差、面の結合部分などです。当社が扱うにはどうしてもリバースした面をソリッドにしなければいけません。接合部分が離れすぎていると後工程のCADが認識できないので、その処理に持っていけるかどうかは非常に重要でした。仮に離れていたとしても他のソフトでリカバリーできるのであれば問題ありません。その連係についても細かく精査しました。
面を構成している制御点の数や入れ方は、それぞれの特徴が出ていたと思います。担当の方の技術もあると思いますが、面の輪郭がきれいにつながっているか、部品に対してどんな面構成になったかなども注目しました。
「spScan」の成績はいかがでしたか。
最終的には「spScan」が断トツでしたね。
他社製品ではリバースデータをCADに流し込んだ時点で止まってしまう、複雑すぎて処理できない、データが化けたり切れたりして目的の形状になっていないものも散見されました。しかし「spScan」は安定して一番複雑な部品でもしっかりリバースしていたので「意外と全部できるんだな」と思った記憶があります。
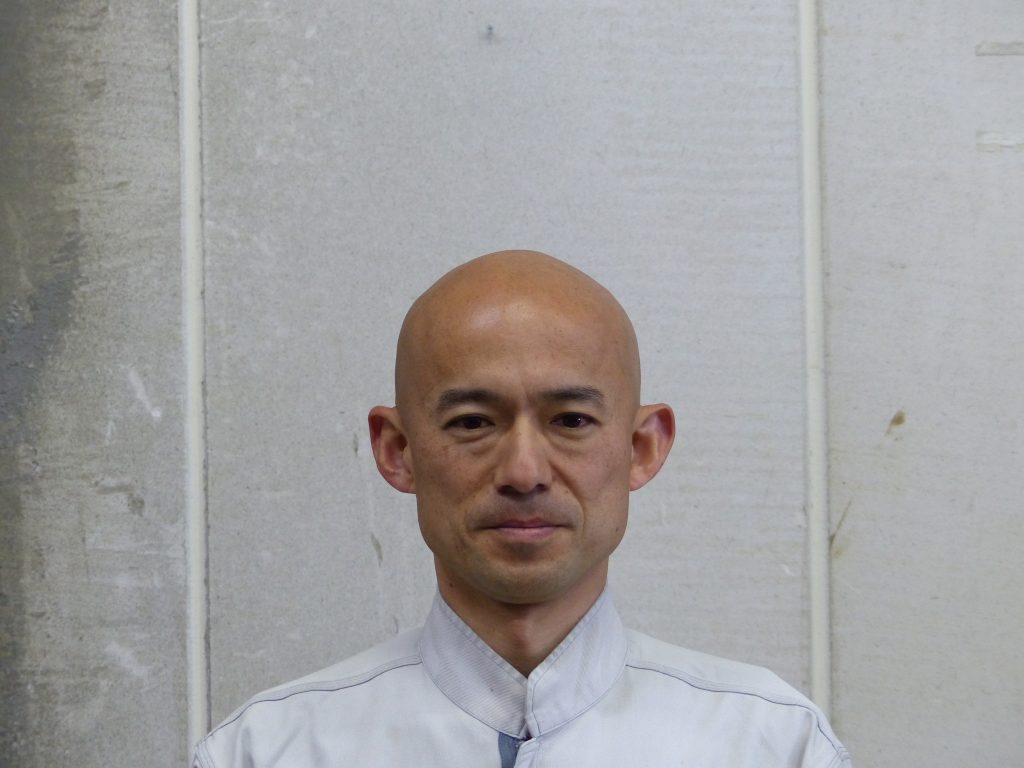
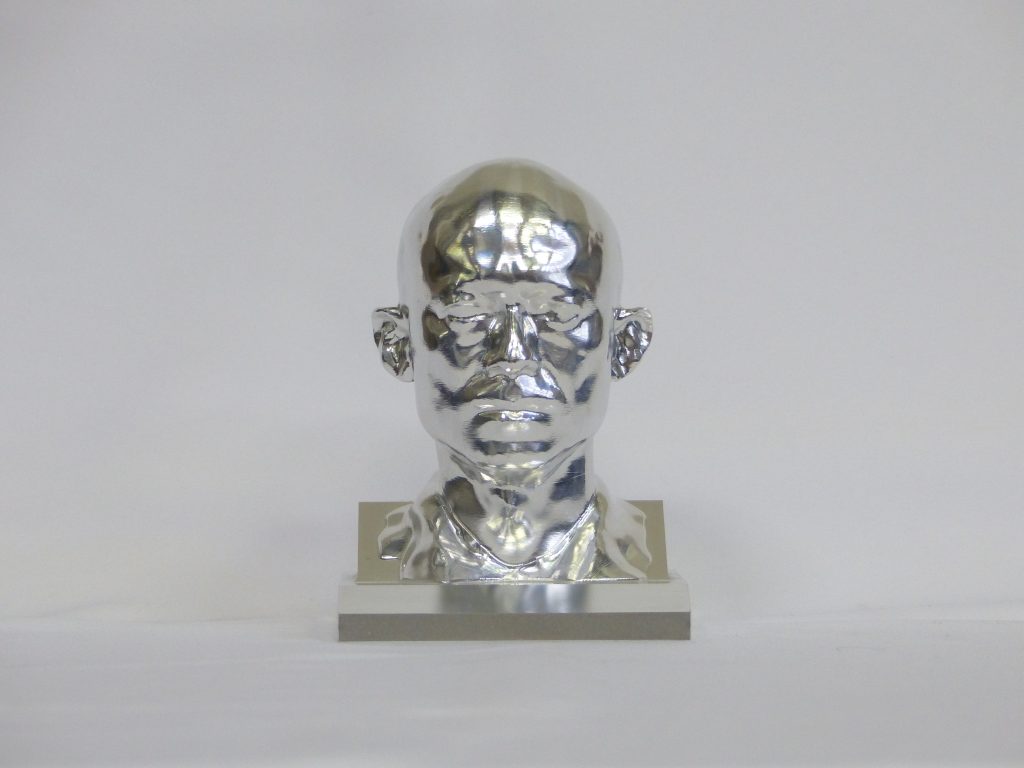
左:山﨑様/右:三次元非接触測定データのデータを修正して、ダイレクト切削加工した完成品
自由度の部分が優れていたのも「spScan」です。面を作り込みたいとき、私が意図した形状にすぐ整えられると言えばいいでしょうか。ある程度のところまでソフトに任せて自動や半自動で作りつつ好きな設定が細かくできます。シビアな自由曲面を持つ製品が多い中、自動と手動のハイブリッドがちょうどいい配分で柔軟に使える印象です。
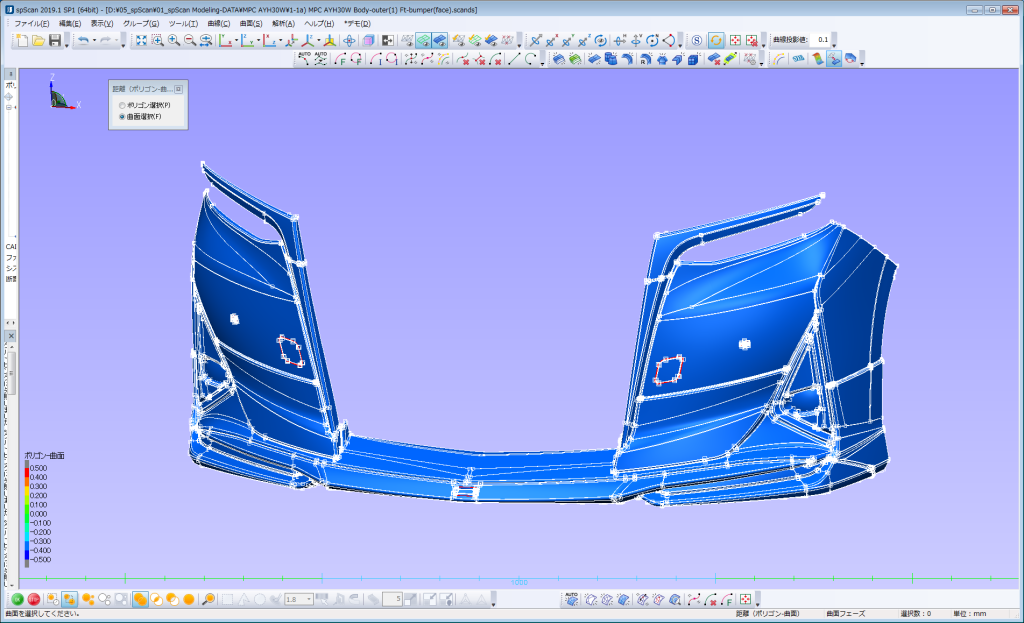
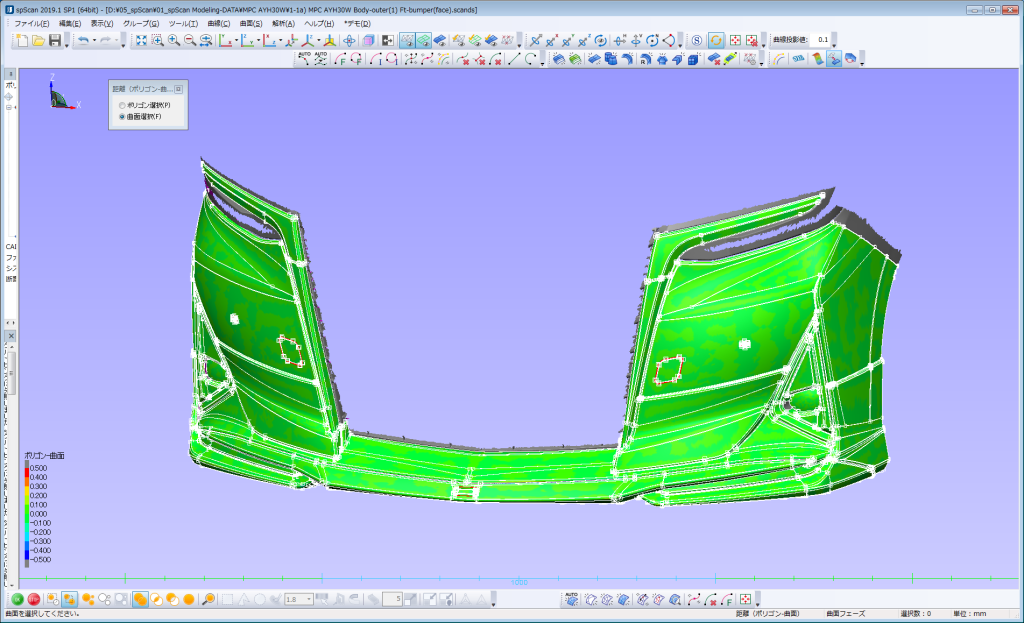
検査・寸法取得→曲面作成・誤差カラーマップ
来てくださった営業や技術担当の方からていねいに説明いただけたのもよかったです。当時は製品自体をよく理解していなかったので初歩的な質問もしたと思いますが、基本操作を含めてとても分かりやすく教えてもらいました。今も難度が高い質問にすぐ回答をいただけるので助かっています。
使いこなすほどリバースの質が上がっていくツール
実際に使い始めて、どんなメリットがありましたか。
モデリングまでの時間は、物にもよりますが1/5ほどに短縮しました。当然単価も下がってお客様に還元できています。リバース事業を始めたときは社内工数を見ると必ずしも黒字ではなかったのですが、工数が読めるようになって今は利益を出しながら提供できるようになりました。
リバースエンジニアリングでは測定データに対して面をどこまできれいに付けられるかがカギです。「spScan」はそういった「面を沿わせる作業」が得意で、自動で任せてもある程度のレベルまで整えてくれます。以前は全て手動だったのでこのプロセスと時間は大いに削減できました。
使い方はすぐに分かりましたか。
導入時はトレーニングに2日間来ていただいて、そこから1カ月か2カ月くらいでそれなりに使えるようになりました。以前から測定データに対して3方向座標や方向性はどうするか、面を構成するUV座標をどう置けばいいかなどの知識はあったので、比較的スムーズに導入できたと思います。
長く使っていると「注力すべきところ/任せてよいところ」が分かってくるので、最近はさらに習熟度が上がったかもしれません。例えば最初は測定データに完全に忠実にやらなければいけないと考えて面構成が粗くなったりしたのですが、今はソフトに任せてしまってもいいポイントが分かります。
導入当時は1時間かかっていた処理も、今なら30分くらいでできるのではないでしょうか。それを考えると、「spScan」導入前と比べてリバースエンジニアリングにかける時間は1/10ほどになっています。
今後はどのような事業で活用していきたいですか。
先ほど述べたように、すでに自動車分野にとどまらない多分野での展開が始まっているので、そこで当社の技術が発揮できればと思っています。
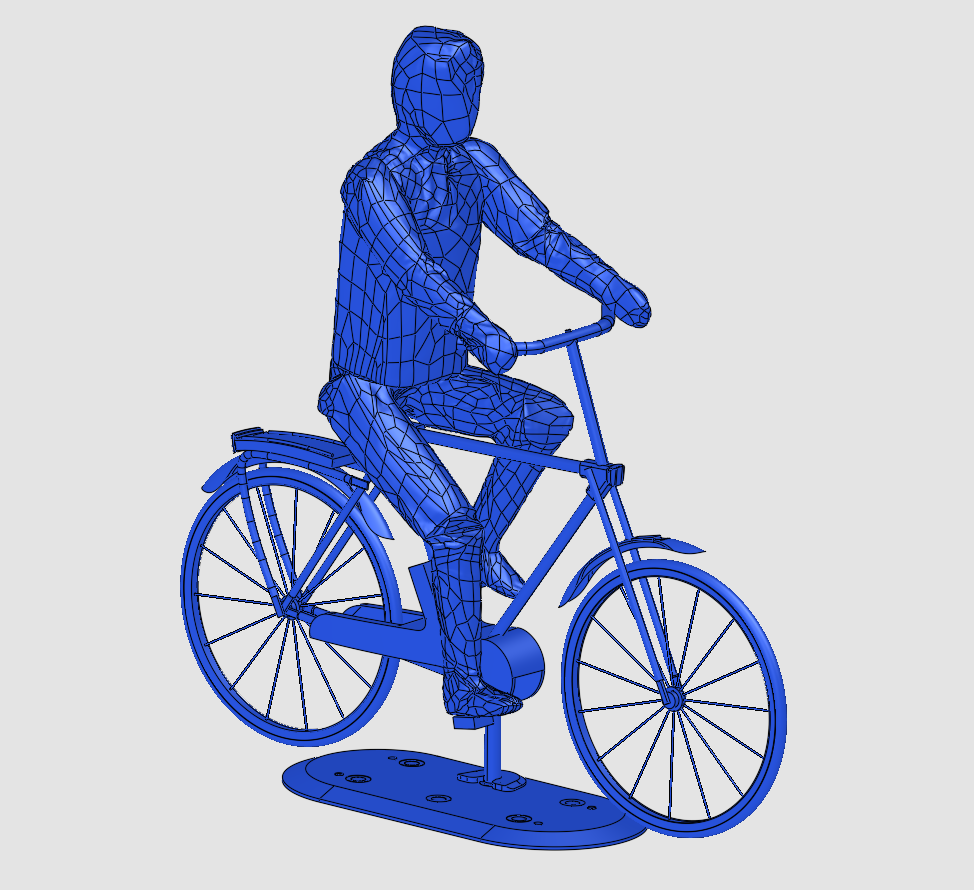
パッチ形状でのリバース例
ダミー人形のリバースモデルを衝突実験の解析に適用(自転車はCADでモデリング)
現在は工業系の引き合いが多く、図面や設計図がない古い部品のモデリング、樹脂部品を射出成形する型や石膏鋳造の型を測定してリバースする案件などを受けています。上場企業からの依頼もあれば個人からの依頼もあり、お客様の規模もさまざまです。
今後は、まだ加工や3Dが浸透していない分野で有効なアドバイスができると考えます。大小のパーツや複雑な機構部品などを開発してきた経験、これまで培った技術力と知見を生かして、多くの新しいお客様と出会っていければと思います。
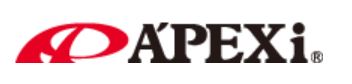
Apex株式会社様
2007年創業の自動車後付け部品開発メーカー。排気系や電子系を中心としたオリジナルブランド「Apexi」製品の開発・製造・販売を行い、マシンの性能向上に特化した品質は国内外のユーザーから信頼を集めている。近年は精密な造形技術や測定ノウハウを活用したリバースエンジニアリング事業を展開し、測定からデザイン設計、製造、検証まで一括で受託可能。自動車業界だけでなく、医療や製造の分野でも実績を伸ばしている。
【この事例で紹介された製品】spScan