カメラ式非接触3Dスキャナ ユーザー事例
省力化した未来の工場構築を目標としてロボット型自動3次元測定機を導入し、最大限のパフォーマンスを発揮する条件を検証中
富山県富山市に本社を置く田中精密工業株式会社は、1948年の創業以来、大手自動車メーカーの自動車・オートバイ部品などを製造販売してきました。主に携わるのはエンジンやミッション、シャーシなどスムーズな走りを左右する部品です。求められる性能が向上するにつれて部品に必要な精度や耐久性は上がりますが、田中精密工業は対応する技術を磨き、拠点を増やしてそのニーズに応えてきました。
現在は、塑形加工から施削・切削、熱処理、仕上、部品組立・検査までの一貫加工体制と、レース用部品まで製造できる高い技術力が評価され、富山県内有数の優良企業として知られる存在です。近年はさらに航空宇宙産業での部品作りに欠かせないISO9001、JISQ9001、JISQ9100認証を取得し、製造事業を拡大しています。
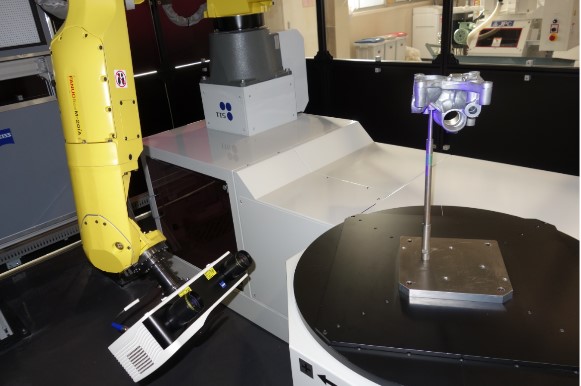
田中精密工業の活動として特筆すべきは2017年12月の「T-IReC(ティーアイレック)」設立です。富山市内の工場を改装して先端技術検証を専門とした施設を作り、将来の工場効率化・省人化を実現するため独自で研究を始めました。在籍する社員はそれぞれAIやマシニング自動化、稼働情報一元化などのテーマを1つ受け持ち、2022年の各拠点導入に向けて導入機械の機能や使用条件の検証を進めています。
その中で3次元測定システムの自動化研究において導入されたのが、東京貿易テクノシステムの非接触3次元測定機「COMET」です。ロボット・ソフトウエア・測定機がセットになったリーズナブルな製品で、ロボットのエキスパートでなくてもティーチングデータを作成できるソフトが附属しています。
さまざまな測定機からこの製品を選んだ理由と、未来の工場でどのように利用する予定なのか、そのためにどんな研究を行っているのかを詳しく伺いました。
企画部 事業企画ブロック FA推進チーム チームリーダー 久世健二さん
自動車に携わる仕事を目指して入社。2017年12月からは「T-IReC」を率いて、未来型の工場を構築するための機材選定や検証、使いこなす人材の育成、その後の普及までを視野に入れて活動している。
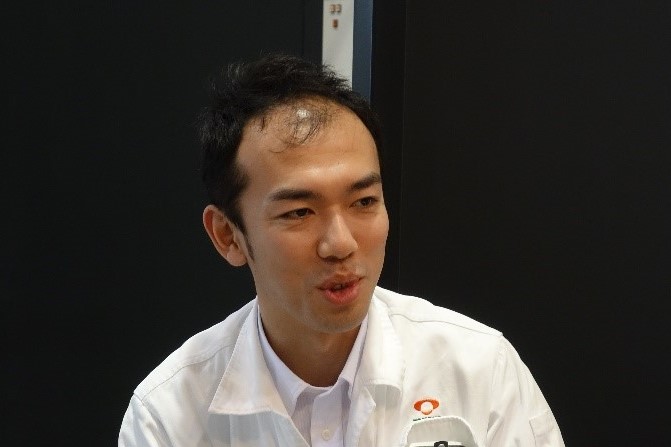
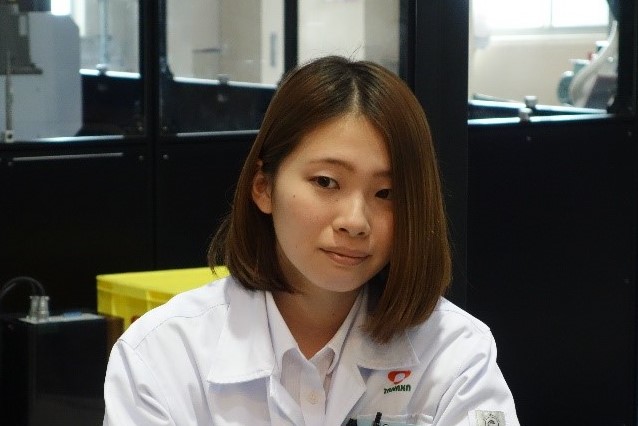
企画部 事業企画ブロック FA推進チーム 坪田美沙子さん
2018年1月に、効率的な自動計測プロジェクトを牽引する担当者として「T-IReC」チームの一員に抜擢される。機材導入後は日々さまざまなワークを行い、今後は各拠点での指導リーダーとしての活躍が期待されている。
2Dの図面ではなく3Dデータのみの受注が増えた
御社は長年、自動車やオートバイ部品の製造で実績をあげてきました。県内を代表する大きな企業になっていますね。
久世健二さん(以下、久世):2018年は弊社創業70年の節目の年でした。発動機や自動車・オートバイメーカーからのニーズに対応して、エンジンやシャーシ、ミッションなどの精密な小型部品の製造で評価を得ています。レース用の部品も担えるほど、技術的にも性能的にも高いレベルでの製品を作ってきた自信があります。
ただ、ここ数年で受注する案件のスタイルが変わってきました。これまでは2Dの図面で「こんな部品を作ってほしい」というオーダーがあり、その設計図から必要な寸法や材質の検討を進められました。しかし5年ほど前から、図面がなく3DCADデータのみでオーダーされる案件が増えてきました。
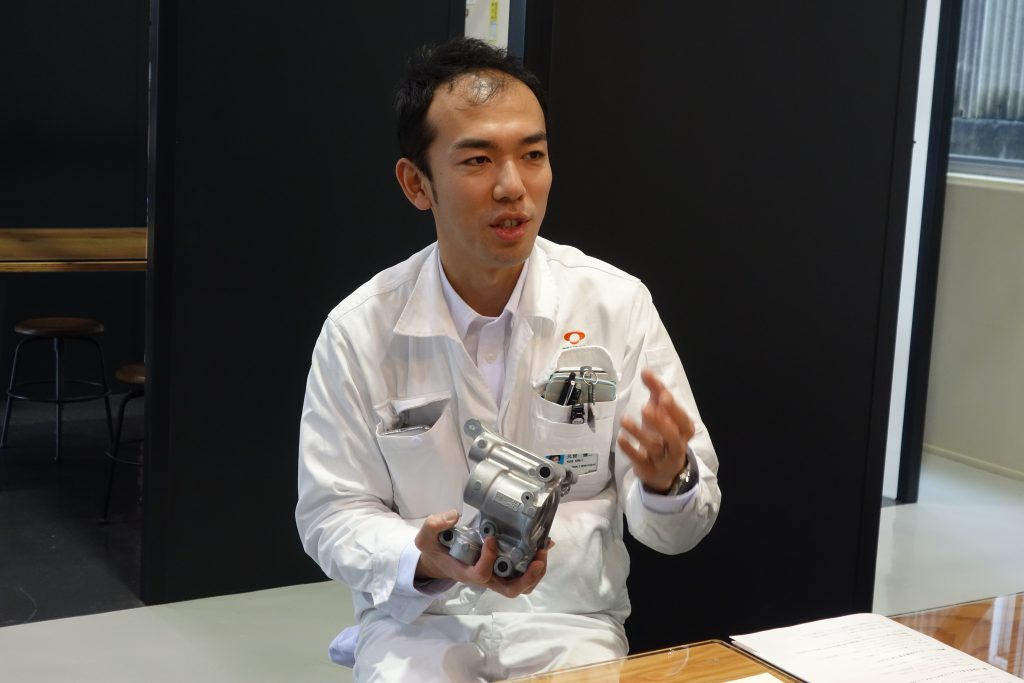
形状図面がないので、実際に現場でアルミダイカスト製品を作るには私たちが3Dデータ内で円弧や角度を確認しなければいけません。そして成型後は「ちゃんとデータと同じものができたか」を正確に測定して品質を保証する必要があります。当時使っていた接触型測定機だとその精度を維持するのが非常に難しい。「もっと早く、もっと正確に」を実現するために非接触型測定機は導入すべきだろうという意見が出てきました。
事業ではもう一つ、重要な流れがあります。弊社はこれまで小型部品を扱ってきたのですが、これからは大型部品や自動車・オートバイ以外の分野で部品作り行って事業を拡大したいと考えています。それらの受注を増やすには昔ながらの方法では対応しきれません。もっと根本的に、工場のあり方や人員配置まで見直す段階だと考えました。
そこで設立されたのが、新技術の研究施設「T-IReC」なんですね。
久世:はい、2017年に製造の技術開発とはまったく別の研究を専門にした組織を作り、具体的に機材を検討・検証するFA推進チームを立ち上げました。目標は、2022年までに弊社の国内外の拠点でさまざまな新機材を導入して、効率化と省力化を実現することです。在籍する社員はAI研究やマシニング自動化など1人1テーマを受け持って、それぞれ研究を進めています。
工場の将来を見据えた中で導入されたのが、非接触3次元測定機「COMET」でした。選定のポイントは何でしたか。
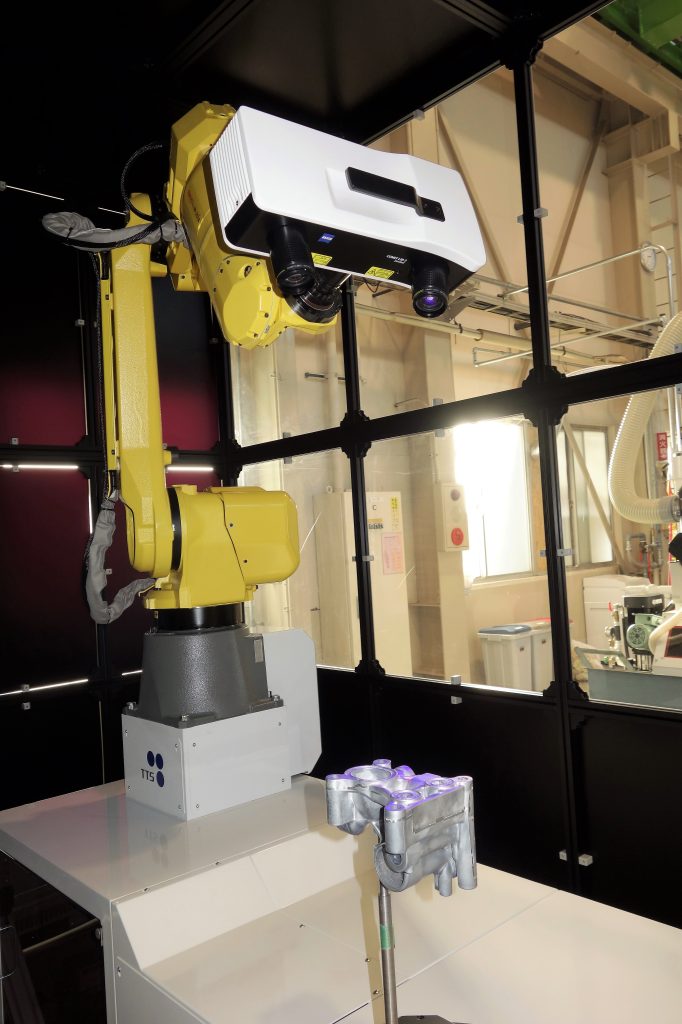
久世:検討を始めたのは2016年です。測定時間を大幅に縮めたかったので、非接触型で自動測定するのが大前提でした。あまり製品知識がなく、まず測定機メーカーが集まる展示会へ行って基本的な仕組みやトレンドの情報を仕入れました。そのとき弊社の用途を考えて20か30の機種は検討したと思います。
実は2017年に、他社の測定機を先に1台導入しました。成型後の形状保証用途にマッチすると考えたからです。ただ、使い始めて1年ほど経った頃に現場から「製造プロセスの途中でも形状を確認したい」というニーズが上がってきました。他社測定機はたしかにさまざまな形状を正確に測る機械なのですが時間がかかりすぎます。最初の検討で「量産中にハイスピードで測定するならCOMETだな」と感じていたので、2台目はすぐ決まりました。
撮影するカメラが一眼である点も弊社にとってはメリットです。複眼の場合、ソフト上で重なった情報は間引きされてしまいます。しかし私たちが欲しい情報は目の前のワークの正確な形状。バグや歪みも含めて捉えるには一眼撮影の測定機が最適で、そのタイプは東京貿易テクノシステムにしかありませんでした。
各拠点で最大のパフォーマンスを発揮するために検証
測定機が「T-IReC」に入ったのは2018年8月末とのことですが、各拠点への導入はこれからですか。
久世:はい、今は自動測定を専門で研究する坪田が「T-IReC」内でさまざまなワークを行い、実際に工場へ導入したときどんな点を考慮すれば最大のパフォーマンスを発揮できるのか、条件を検証している段階です。
坪田さん(以下、坪田):製造現場での形状確認測定では、大幅に時間が短くなることがわかっています。たとえば前の測定機だと1日がかりだったワークが「COMET」だと30分かからず完了する。光沢面の測定にも想像以上に強い。ダイカストの金型は使用しているうちに変化するものなので、その変化が日々把握できれば品質管理に役立ちます。
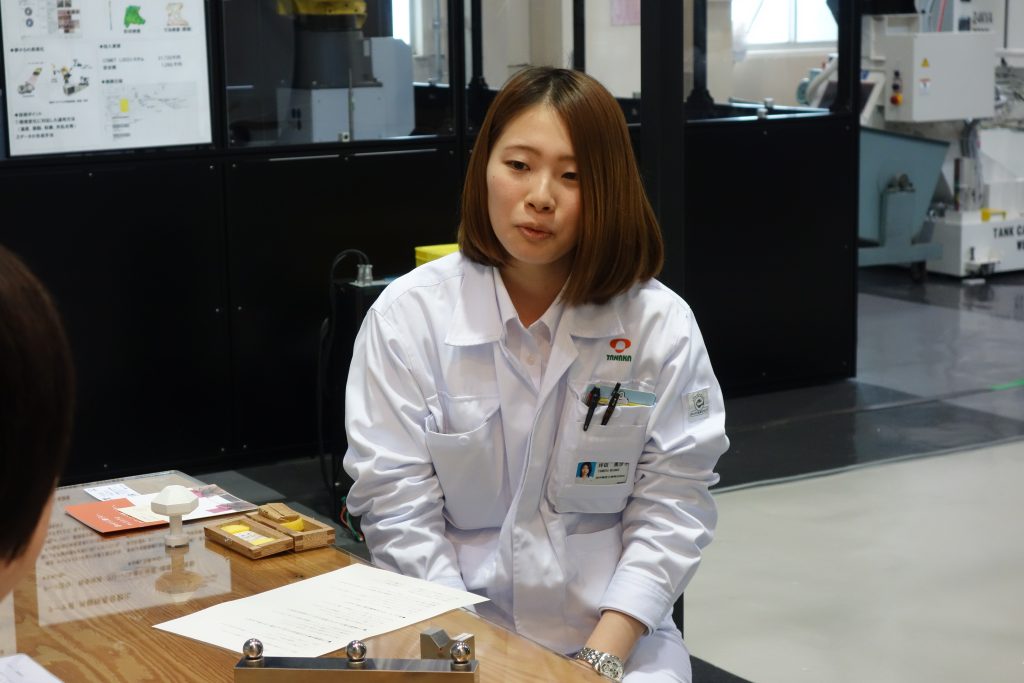
しかし各工場で最大効率を求めるとなると、使用条件をしっかり吟味しなければいけません。製造現場は油煙や粉塵、温度変化の幅、製造中の振動などが存在します。その中で正確な数値を測定するためにどんな環境を整えなければいけないのか、逆にどのくらいの条件幅なら測定値のブレを無視できるのか。場所によっても測定する製品によっても求めるものが違うので、各拠点の最適な使い方について検証を進めているところです。
久世:彼女は非接触3次元測定について何も知らない状態で配属されましたが、今は社内で一番のエキスパートですよ。
操作感や使い勝手はどうですか。
坪田:導入するとき東京貿易テクノシステムから指導する方がいらして、4日間マンツーマンで操作を教えてもらいました。そのほか、3次元測定の基礎知識や面の捉え方などの概念については県の職業能力開発センターで3日間の講習を受け、産業用ロボットの特別教育も配属後に受けました。
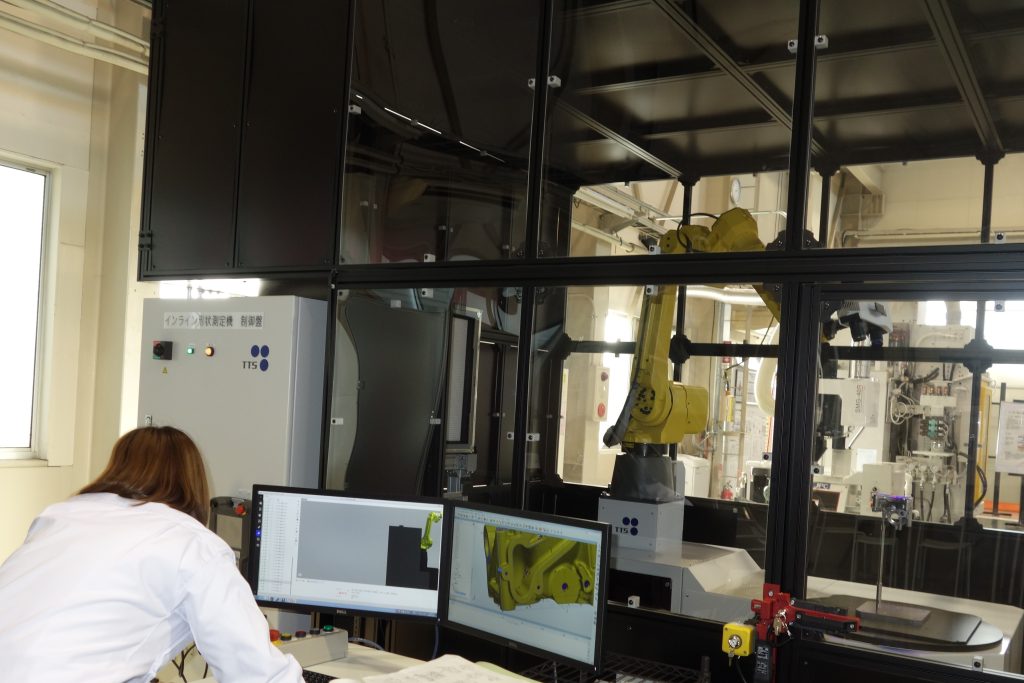
9月から使い始めて「この画面が出ているがどうすればいいか」など、初歩的なことでも何でも、とにかくわからなくなったらサポートセンターに連絡しています。画像つきのメールで送ったり、急ぐときは電話をしたり、すぐ回答が返ってくるので不安はありません。
久世:性能としても、測定プログラム作成までソフトで行ってくれるのは技術の進歩を感じます。シミュレーション上でワークをセットするとアームが自動でグルグルと回って測定ポイントを見つけ、ロボットへプログラムを送ってくれる。この手軽さは、今後全拠点に導入したときも人手不足を解消する大きなポイントになると思います。 それに一人の担当者がずっと窓口になってくれるので、弊社の使用環境や目的まで把握したアドバイスをもらえるのは心強いですね。一度トラブルがあったのですが、数通りの復旧プランを提示して隠すことなく状況を正確に教えてくれました。結局、想定よりかなり早く解決できましたが、対応力の高さを実感しました。
3次元測定機以外の機材の研究も進められていますが、今後はどのような展開を予定していますか。
久世:第一の目標は、各機材を最適な状態で拠点へ導入し、効率化と省力化を実現することです。機材の条件設定はこちらで行い、できるだけ現場の手を煩わせることなく製造ラインに投入したいと考えています。新人でもすぐ操作を覚えて現場で使えるようなレベルまで運用効率を引き上げたいですね。
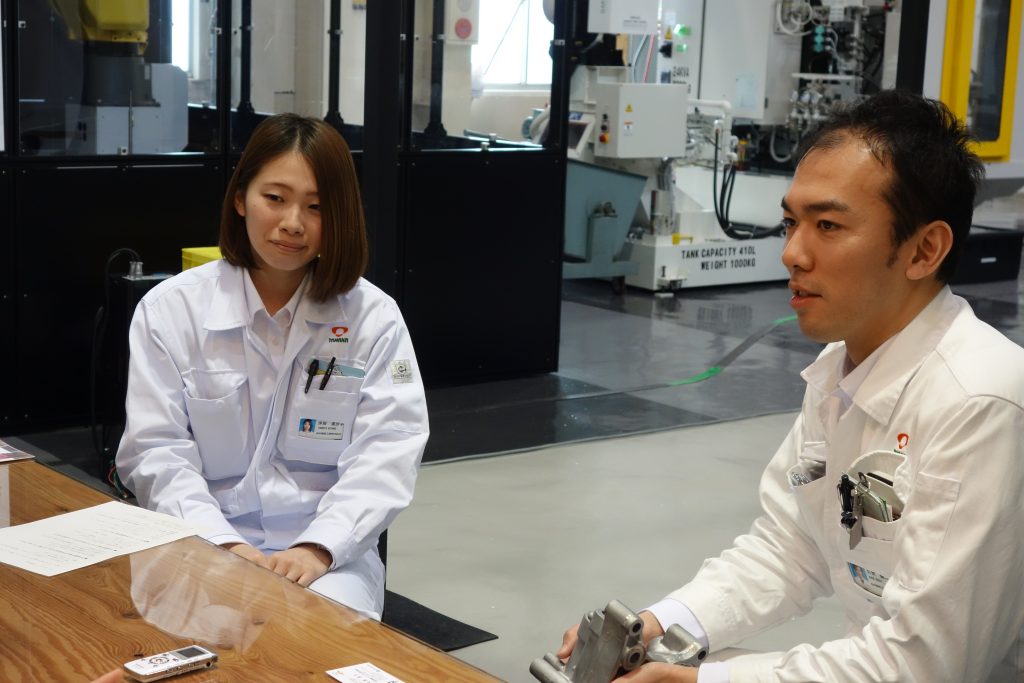
たとえば製品に2次元バーコードを打ってそれを読み込めば自動的に測定まで行えるとか、工場全体が自己診断の機能を持ってアイドリングまで自動で行うとか、いろんな技術を統合できたら省力化はさらに進みます。将来的には、弊社で開発した工場効率化のシステムそのものをパッケージとして販売する事業も視野にあります。
単に人手不足を解消するというより、機械に任せられる仕事は早く自動化して、人間がもっとクリエイティブな仕事に集中できる環境を作りたい。製造業にはその余地がまだまだあると思っています。
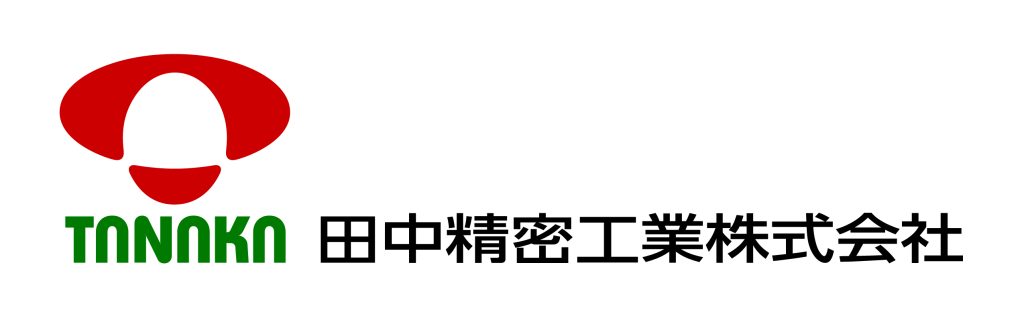
田中精密株式会社様
1948年に田中製作所として創業後、1951年に田中金属工業有限会社に。1955年に「田中精密工業」の名を掲げて1957年に株式会社化。自動車・オートバイ部品の製造販売を中心に事業を展開し、高精度・高性能部品のサプライヤーとして評価を得る。2017年12月に先端技術の研究施設「T-IReC」を設立、製造の技術開発とは別に将来の工場効率化・省力化を見据えた検証を行っている。研究成果は2022年までに国内外の拠点へ導入予定。
【この事例で紹介された製品】COMET
※同モデルは製造・販売を終了しております。なおサポートは継続しております。詳細については担当営業までお問い合わせください。
また、リンクよりカメラ式非接触3Dスキャナの新商品であるFLAREシリーズのページをご覧ください。