
複数の大型部品から構成される大型構造物の製造プロセスでは、それぞれの部品を最終設置場所に運搬してから組み立てるため、現地で部品同士が合わないとなると一大事で、現地までの搬送費や、組立のために押さえていた重機や作業員の工数が無駄になってしまいます。そのようなことを未然に防ぐため、出荷前に仮組立を実施し、本当に部品同士が結合できるかどうかを工場内で事前確認しています。しかし、仮組立は非常に大変な作業で、次のような課題があります。
- 仮組立に多大な時間を要する(場合によっては1週間以上)
大型構造物の仮組立は、通常クレーンを使用した作業となり、簡易溶接を実施する場合もあるため、大変大掛かりな作業です。仮組立による確認後はそれらのバラシ作業も同様に時間を要します。また、クレーンの使用状況によってはロスタイムも発生します。 - 複数人の工数・広い場所取りが必要
数m以上の大型部品同士の仮組立を行うには、複数人が同時に作業を行う必要があり、それを実施するための広いスペースを確保しておかなければなりません。 - 高所作業を伴う危険作業
大型構造物の仮組立は高所作業を伴うため、安全面のリスクがあります。不安定な場所での落下・転落を防ぐには、十分な安全対策が必要です。
通常の現場作業は下図の流れで実施されますが、仮組立でNGだった場合は、仮組立前の部品をそれぞれ修正してから再仮組立が必要となり、工数は倍増します。実際に仮組立を実施してみないと成否が判明しないため、仮組立を繰り返す回数によって納期にも影響が及びます。また、簡易溶接を伴う仮組立では、バラシ時に変形してしまうリスクも考えられます。
【現場作業の流れ】
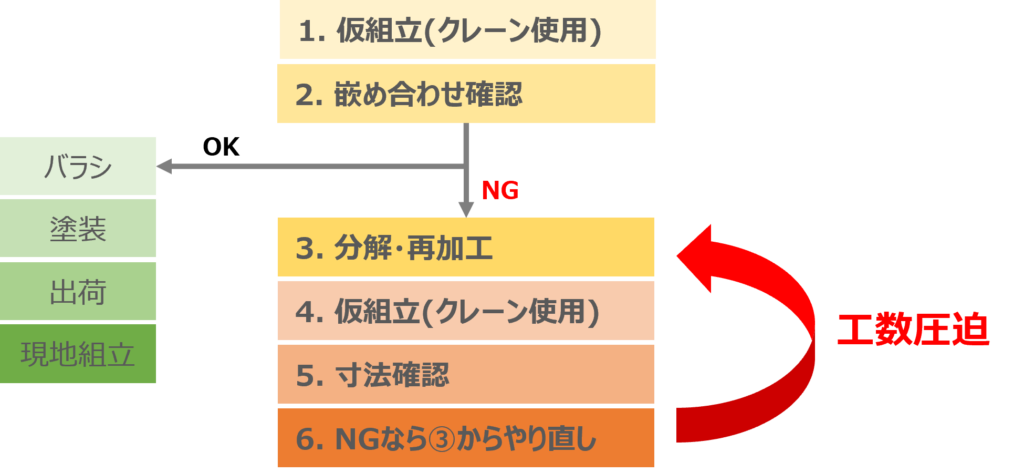
- 課題
-
- 大型部品の寸法・形状計測は困難で工数が掛かる
長さ・奥行・高さが数メートル以上、且つ重量が数トンを超えるような大型部品の寸法・形状計測は非常に困難で、多大な時間を要します。 - 大型ノギスによる寸法検査には限界がある
重量が15kg程ある大型ノギスを1つ扱うにも2人掛かりで作業する必要があり、寸法検査できる箇所にも限度があります。
計測プロセスにおいても、従来の計測手法では大型部品であるが故の課題があります。
- 大型部品の寸法・形状計測は困難で工数が掛かる
いかにアナログからデジタルにシフトし、現場作業の流れにある1~6をプロセスチェンジできるかが重要なポイントとなります。
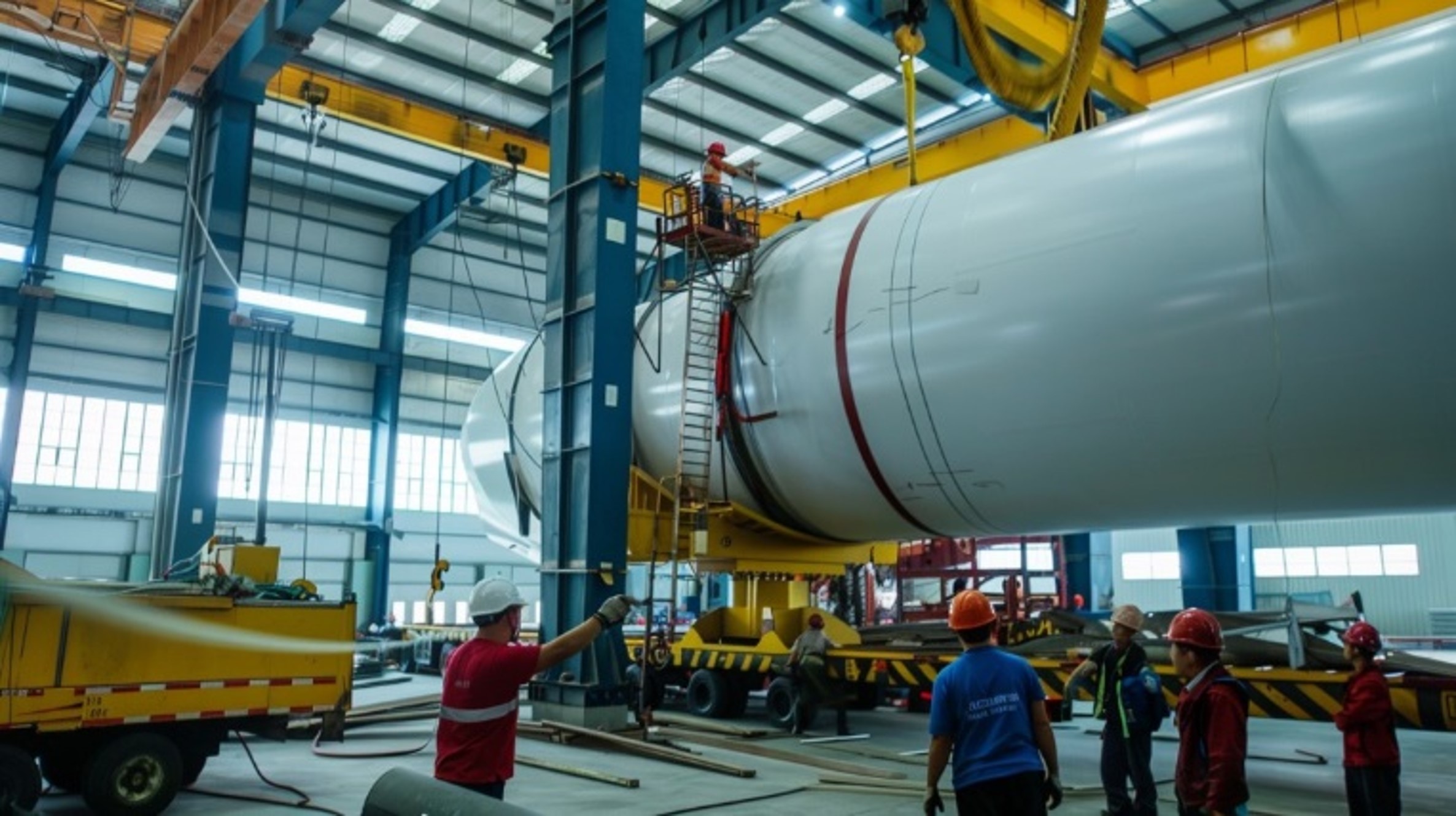
ソリューション
大型部品同士をバーチャルに仮組立が可能なLeicaレーザートラッカーATS600を用いることで、出荷前の仮組立レスを実現します。
1. 製造現場で素早く設置
部品の製造現場に設置してから電源投入後、自動で準備が完了し、わずか約3分で計測開始が可能です。
また、どのような態勢でも計測が可能なため、水平出しの必要がありません。
2. 高精度3次元計測・高品質データ
高精度なスキャニング計測、リフレクター計測、単点計測が可能です。
1.スキャニング計測(多点計測)
計測レンジ
1.5m~60m
計測精度:±0.3mm
(精度保証30mまで入射角45°まで)
2. リフレクタ計測
計測レンジ
0.8m~80m
計測精度:±15μm+6μm/m
3. バーチャル仮組立(仮組立レス)
嵌め合わせる部品の3D計測データを用いてソフトウェア上でバーチャルに嵌め合わせ状況が確認できるため、実物の部品同士を仮組立せずに成否判断が可能になります。NGだった場合は、具体的な不具合箇所の可視化により素早く修正作業に着手できます。
システム構成(提案例)
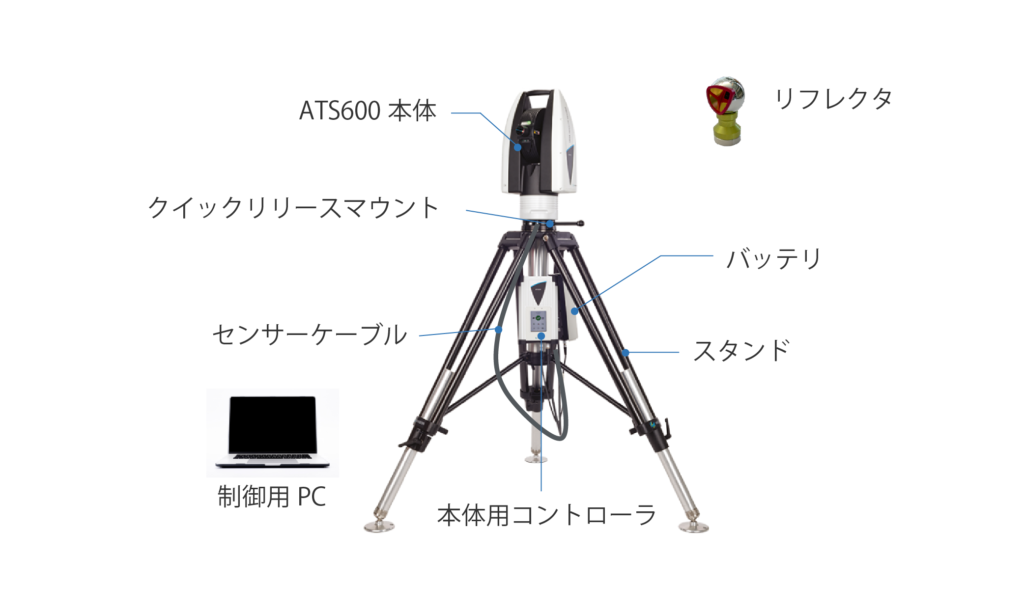
ATS600に関する製品情報はこちらをご確認ください
作業フロー(例)
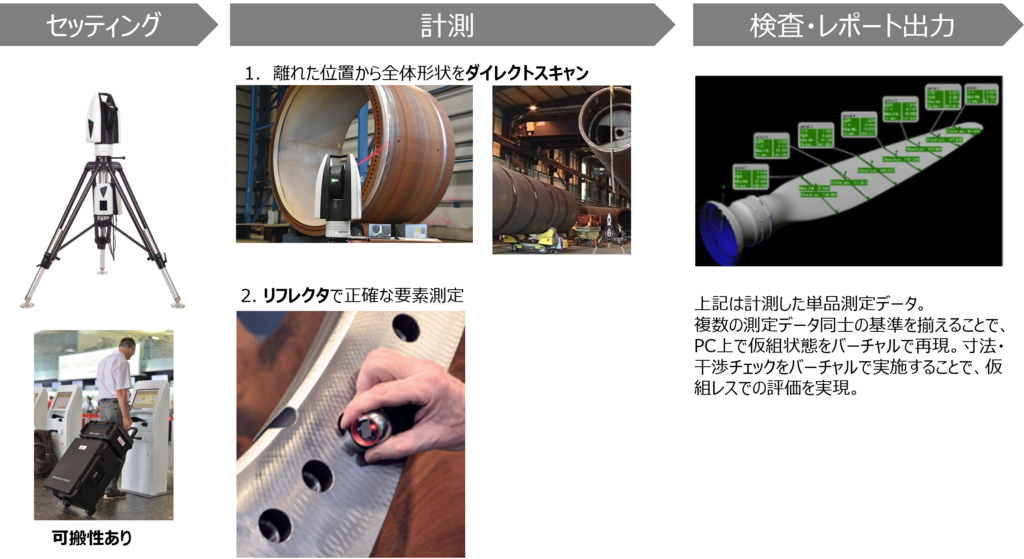
効果
広範囲計測に最適なATS600を使用することでPC上でバーチャルに仮組立状態を確認することが可能になります。従来は大掛かりな作業に対して、必要最低限の寸法情報しか得られませんでしたが、プロセスチェンジにより、部品形状全体をデータ化し、デジタル管理することで仮組立レスを可能にします。これにより、次のような効果が期待できます。
- 1. 次の加工までの待機時間の解消(効率の良い工程管理)
- 2. 加工品質の信頼性向上(3Dデータによる誤差をカラーマップ表示)
- 3. 適切な人員計画
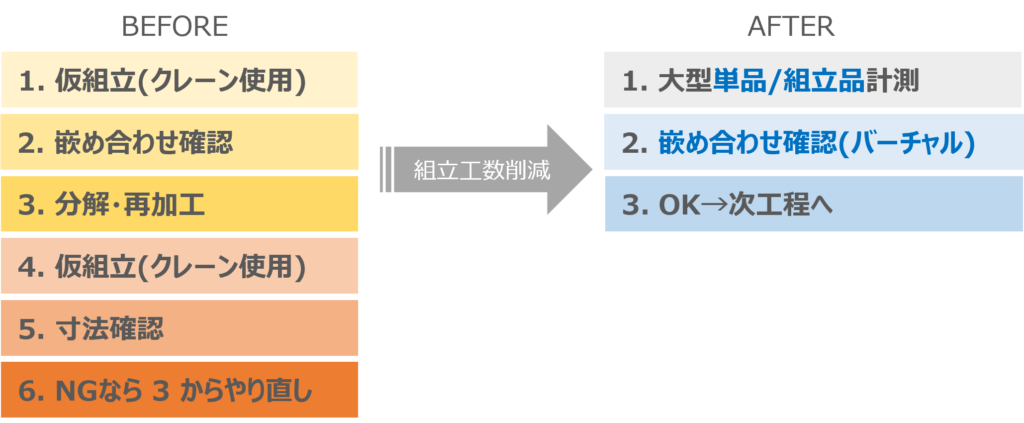
実際にATS600を導入したことで、従来作業の半分以上の工数削減を実現されているお客様もいらっしゃいます。また、何よりも大切な作業員の生命に関わる危険作業(高所作業等)を無くせたことに対する反響も多く頂いてます。
このように、ATS600は工数削減、品質向上、そして安全リスクを低減できるソリューションとしてご好評いただいております。
詳細につきましてはお気軽にお問合せください。
弊社ではご提案できるソリューションを多数用意しております。
ぜひ、お困りごとをお聞かせください!